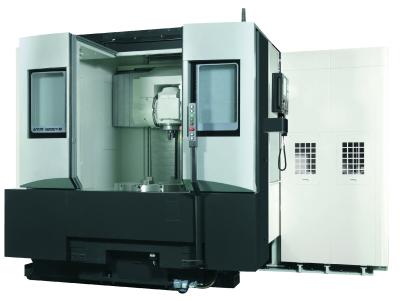
Okuma‘s VTM-1200YB multitasking CNC turning center is built to handle heavy-duty turning and cutting of large parts. The massive construction, extreme rigidity and powerful cutting capabilities of this machine make it ideal for machining large diameter workpieces, such as those in the aerospace and energy industries, according to the company.
The vertical design delivers high precision and accuracy and offers the advantage of “natural” part handling and excellent chip fall, while taking up minimal floor space. The VTM-12000YB cuts a variety of shapes, from turning to slope multitasking. It performs turning, vertical, horizontal and angled surface machining in one operation. The work spindle is supported at two locations by large diameter roller bearings that offer precise control for the production of complex parts. The high torque spindle is capable of sustaining heavy cutting that is necessary for large parts such as valve bodies.
This machine comes equipped with the new OSP-P300S control, Thermo-Friendly Concept to maintain thermal stability and Collision Avoidance System to prevent costly collisions.
Key Specs of VTM-1200YB CNC Turning Center
Max Turning Diameter 47.24” x 60.23 high
Lathe Spindle Speed min⁻¹ 5~500
Milling Spindle Speed min⁻¹ 10,000
Rapid Traverse (X/Y/Z) m/min (ipm) 32/32/32 (1,260/1,260/1,260)
Rapid Traverse (B/C) RPM 19.5/20
Contact Details
Related Glossary Terms
- computer numerical control ( CNC)
computer numerical control ( CNC)
Microprocessor-based controller dedicated to a machine tool that permits the creation or modification of parts. Programmed numerical control activates the machine’s servos and spindle drives and controls the various machining operations. See DNC, direct numerical control; NC, numerical control.
- gang cutting ( milling)
gang cutting ( milling)
Machining with several cutters mounted on a single arbor, generally for simultaneous cutting.
- lathe
lathe
Turning machine capable of sawing, milling, grinding, gear-cutting, drilling, reaming, boring, threading, facing, chamfering, grooving, knurling, spinning, parting, necking, taper-cutting, and cam- and eccentric-cutting, as well as step- and straight-turning. Comes in a variety of forms, ranging from manual to semiautomatic to fully automatic, with major types being engine lathes, turning and contouring lathes, turret lathes and numerical-control lathes. The engine lathe consists of a headstock and spindle, tailstock, bed, carriage (complete with apron) and cross slides. Features include gear- (speed) and feed-selector levers, toolpost, compound rest, lead screw and reversing lead screw, threading dial and rapid-traverse lever. Special lathe types include through-the-spindle, camshaft and crankshaft, brake drum and rotor, spinning and gun-barrel machines. Toolroom and bench lathes are used for precision work; the former for tool-and-die work and similar tasks, the latter for small workpieces (instruments, watches), normally without a power feed. Models are typically designated according to their “swing,” or the largest-diameter workpiece that can be rotated; bed length, or the distance between centers; and horsepower generated. See turning machine.
- milling
milling
Machining operation in which metal or other material is removed by applying power to a rotating cutter. In vertical milling, the cutting tool is mounted vertically on the spindle. In horizontal milling, the cutting tool is mounted horizontally, either directly on the spindle or on an arbor. Horizontal milling is further broken down into conventional milling, where the cutter rotates opposite the direction of feed, or “up” into the workpiece; and climb milling, where the cutter rotates in the direction of feed, or “down” into the workpiece. Milling operations include plane or surface milling, endmilling, facemilling, angle milling, form milling and profiling.
- rapid traverse
rapid traverse
Movement on a CNC mill or lathe that is from point to point at full speed but, usually, without linear interpolation.
- turning
turning
Workpiece is held in a chuck, mounted on a face plate or secured between centers and rotated while a cutting tool, normally a single-point tool, is fed into it along its periphery or across its end or face. Takes the form of straight turning (cutting along the periphery of the workpiece); taper turning (creating a taper); step turning (turning different-size diameters on the same work); chamfering (beveling an edge or shoulder); facing (cutting on an end); turning threads (usually external but can be internal); roughing (high-volume metal removal); and finishing (final light cuts). Performed on lathes, turning centers, chucking machines, automatic screw machines and similar machines.