Contact Details
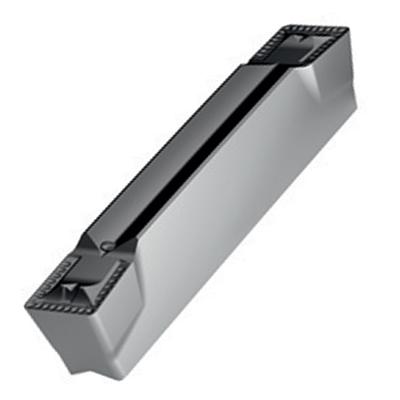
Walter USA LLC has introduced Walter Cut UD4, a new insert geometry for radial grooving and groove turning in the automotive and general metalworking industries that delivers maximum process reliability, optimal chip formation, high levels of productivity and reduced tooling costs.
The Walter Cut UD4 features a new multifunctional chip breaker design that provides superior chip control, thanks in part to its double geometry that delivers a large application area. It has a strong 0 degree primary chamfer that strengthens the cutting edge, a silver surface that makes for easy wear detection and full usage of cutting edges. It also features a new coating that delivers lower fiction and better wear resistance.
With a standard PVD coating there is typically a high rate of heat transfer into the cutting tool insert substrate, which leads to higher wear rates. With the Walter Cut UD4 Tiger-tec Silver PVD aluminum oxide coating there is less heat in the substrate, leading to higher tool life, reduced tool and tool change cost, increased process reliability and higher productivity, according to the company.
The main application area for the UD4 is grooving and groove turning on forged materials such as transmission components, gears and shafts. IT works especially well in low carbon steels where chip control is a particularly big challenge. Targeted workpiece materials are steel and cast iron (ISO P and ISO K).
Related Glossary Terms
- aluminum oxide
aluminum oxide
Aluminum oxide, also known as corundum, is used in grinding wheels. The chemical formula is Al2O3. Aluminum oxide is the base for ceramics, which are used in cutting tools for high-speed machining with light chip removal. Aluminum oxide is widely used as coating material applied to carbide substrates by chemical vapor deposition. Coated carbide inserts with Al2O3 layers withstand high cutting speeds, as well as abrasive and crater wear.
- carbon steels
carbon steels
Known as unalloyed steels and plain carbon steels. Contains, in addition to iron and carbon, manganese, phosphorus and sulfur. Characterized as low carbon, medium carbon, high carbon and free machining.
- grooving
grooving
Machining grooves and shallow channels. Example: grooving ball-bearing raceways. Typically performed by tools that are capable of light cuts at high feed rates. Imparts high-quality finish.
- metalworking
metalworking
Any manufacturing process in which metal is processed or machined such that the workpiece is given a new shape. Broadly defined, the term includes processes such as design and layout, heat-treating, material handling and inspection.
- physical vapor deposition ( PVD)
physical vapor deposition ( PVD)
Tool-coating process performed at low temperature (500° C), compared to chemical vapor deposition (1,000° C). Employs electric field to generate necessary heat for depositing coating on a tool’s surface. See CVD, chemical vapor deposition.
- turning
turning
Workpiece is held in a chuck, mounted on a face plate or secured between centers and rotated while a cutting tool, normally a single-point tool, is fed into it along its periphery or across its end or face. Takes the form of straight turning (cutting along the periphery of the workpiece); taper turning (creating a taper); step turning (turning different-size diameters on the same work); chamfering (beveling an edge or shoulder); facing (cutting on an end); turning threads (usually external but can be internal); roughing (high-volume metal removal); and finishing (final light cuts). Performed on lathes, turning centers, chucking machines, automatic screw machines and similar machines.
- wear resistance
wear resistance
Ability of the tool to withstand stresses that cause it to wear during cutting; an attribute linked to alloy composition, base material, thermal conditions, type of tooling and operation and other variables.