Contact Details
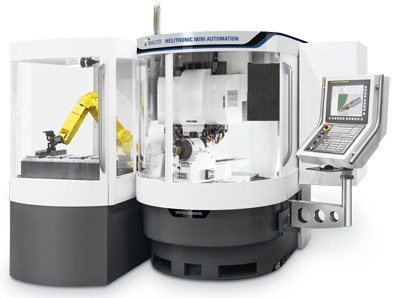
United Gringing has introduced its Walter Helitronic Mini Automation grinding machine. The 5-axis universal tool grinding machine brings maximum flexibility and precision to the high-volume production of rotationally symmetrical tools and production components.
The machine's double-ended spindle can accommodate up to three grinding wheels per end to process end mills, drills, step drills, step tools, woodworking tools, profile blades and profile tools from 0.04" (1mm) to 0.63" (16mm) in diameter. Maximum tool length is 7.3" (185mm), with a minimum diameter of 0.04" (1mm) for production blanks and 0.12" (3mm) for regrinding. Tool materials can include carbide, HSS, ceramic, cermet or CBN.
A FANUC control and Helitronic Tool Studio software combine to operate five CNC axes including linear X, Y, and Z ball screw axes, an A-axis with a torque motor, and a rotational C-axis with a worm drive. The machine's continuously variable grinding spindle drive features a 12-hp (9-kW) motor.
Engineered for high-production volumes, the machine has a robot loader that can handle up to 1,500 tools. An optional extension for a robot loader can hold four additional pallets for up to 2,000 tools, providing a total production capacity of 3,500 tools. Positioning via glass scales, the machine's solid gray-cast-iron base, and gantry-type construction ensure accuracy and consistency over long production runs.
Related Glossary Terms
- computer numerical control ( CNC)
computer numerical control ( CNC)
Microprocessor-based controller dedicated to a machine tool that permits the creation or modification of parts. Programmed numerical control activates the machine’s servos and spindle drives and controls the various machining operations. See DNC, direct numerical control; NC, numerical control.
- cubic boron nitride ( CBN)
cubic boron nitride ( CBN)
Crystal manufactured from boron nitride under high pressure and temperature. Used to cut hard-to-machine ferrous and nickel-base materials up to 70 HRC. Second hardest material after diamond. See superabrasive tools.
- grinding
grinding
Machining operation in which material is removed from the workpiece by a powered abrasive wheel, stone, belt, paste, sheet, compound, slurry, etc. Takes various forms: surface grinding (creates flat and/or squared surfaces); cylindrical grinding (for external cylindrical and tapered shapes, fillets, undercuts, etc.); centerless grinding; chamfering; thread and form grinding; tool and cutter grinding; offhand grinding; lapping and polishing (grinding with extremely fine grits to create ultrasmooth surfaces); honing; and disc grinding.
- grinding machine
grinding machine
Powers a grinding wheel or other abrasive tool for the purpose of removing metal and finishing workpieces to close tolerances. Provides smooth, square, parallel and accurate workpiece surfaces. When ultrasmooth surfaces and finishes on the order of microns are required, lapping and honing machines (precision grinders that run abrasives with extremely fine, uniform grits) are used. In its “finishing” role, the grinder is perhaps the most widely used machine tool. Various styles are available: bench and pedestal grinders for sharpening lathe bits and drills; surface grinders for producing square, parallel, smooth and accurate parts; cylindrical and centerless grinders; center-hole grinders; form grinders; facemill and endmill grinders; gear-cutting grinders; jig grinders; abrasive belt (backstand, swing-frame, belt-roll) grinders; tool and cutter grinders for sharpening and resharpening cutting tools; carbide grinders; hand-held die grinders; and abrasive cutoff saws.
- high-speed steels ( HSS)
high-speed steels ( HSS)
Available in two major types: tungsten high-speed steels (designated by letter T having tungsten as the principal alloying element) and molybdenum high-speed steels (designated by letter M having molybdenum as the principal alloying element). The type T high-speed steels containing cobalt have higher wear resistance and greater red (hot) hardness, withstanding cutting temperature up to 1,100º F (590º C). The type T steels are used to fabricate metalcutting tools (milling cutters, drills, reamers and taps), woodworking tools, various types of punches and dies, ball and roller bearings. The type M steels are used for cutting tools and various types of dies.