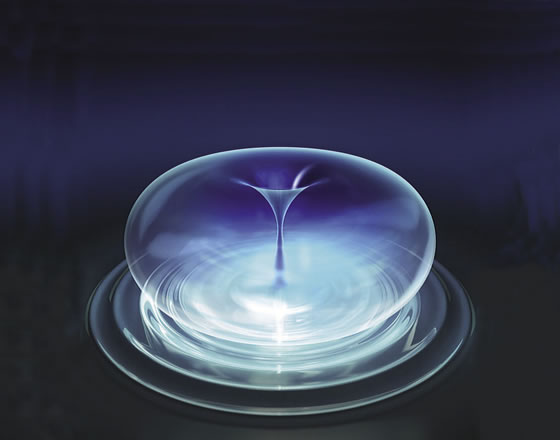
Courtesy of Blue Wave Ultrasonics
This illustration represents a single imploding microscopic bubble in an ultrasonic clearing system. These imploding bubbles create a scrubbing action on the surfaces of parts being cleaned, including intricate and hard-to-reach areas. For a video demonstration presented by Blue Wave Ultrasonics, click here.
Cutting fluid, grease and fine metal chips are unwelcome guests on freshly machined parts. To remove that debris, part manufacturers often employ ultrasonic cleaning, and the technology is also used for reclamation and maintenance cleaning. Ultrasonic cleaning can remove tough contaminants without damaging parts—even delicate ones—and is effective at reaching into small cracks and crevices to remove trapped soils from parts made of various materials, including metal, ceramic, glass and plastic.
One reason ultrasonic cleaning is so prevalent is that it can quickly clean batches of parts. Typical cleaning times vary, depending on the amount and type of contaminants on the parts and the level of cleanliness required, ranging from a couple of minutes to 10 minutes for new parts. “Oils and contaminants from the manufacturing process are light soils so they are not that difficult to remove,” said John Manley, general manager of Tierra Tech USA, an Alvarado, Texas-based manufacturer of ultrasonic cleaning equipment.
Ultrasonic cleaning also has become increasingly popular due to restrictions on the use of chlorofluorocarbons. “In the past 20 years, there have been more and more stipulations on what cleaning chemistries you can use in your plant,” said Kalvin Frank, sales engineer for equipment maker Blue Wave Ultrasonics, Davenport, Iowa. “For instance, 1,1,1, trichloroethane is an excellent cleanser, but has been phased out of production because of its classification as an ozone-depleting material by the Montreal Protocol.”
Ultrasonic energy introduces alternating high- and low-pressure phases into a cleaning solution, which creates millions of microscopic bubbles throughout the solution. Once the bubbles reach a critical size, they implode, creating an intense scrubbing action that, along with a detergent, removes part contaminants.
Obtaining the best results takes an understanding of the various factors that impact the ultrasonic cleaning process. “When dealing with any cleaning process, we look at three things: cleaning at the right temperature, the chemistry of detergents and the agitation, which, in this case, occurs with the cavitation process produced by the ultrasonic cleaning equipment,” Frank said. “If you have any one of these wrong, it can produce inadequate results.”
The combination of temperature and chemistry starts to break down the contaminants and loosen the bonds they have to the substrates. The cavitation removes them from the substrate, allowing the detergent to tie them up once they are in the solution, Frank added.
Temperature and Chemistry
In general, higher temperatures result in higher cavitation intensity and better cleaning for most materials. “Temperature is critical,” Frank said. “Sound travels easier through a heated solution, so it cavitates better at higher temperatures. And, the contaminants break down better at higher temps. However, once you approach the boiling point of the solution, the cavitation intensity begins to fall off.”
In addition, part materials can restrict the use of higher temperatures. For instance, aluminum, depending on the heat treatment, may not be able to withstand temperatures higher than 150° F for long, and ultrasoninic cleaning may start to darken or damage the surface finish, according to Charles P. Kaczorek, technology department manager, Crest Ultrasonics Corp., Trenton, N.J.
The choice of detergent depends on the parts being cleaned and the contaminants being removed. There are innumerable choices, but it is important to select a cleanser formulated for ultrasonic equipment.
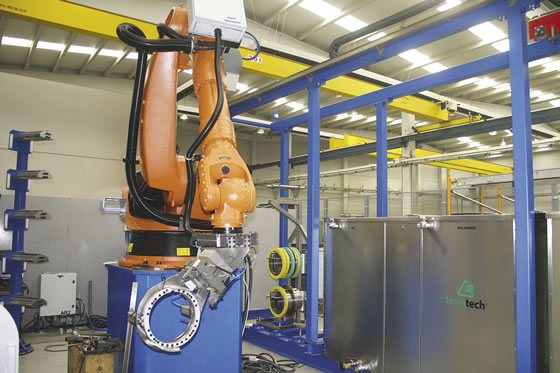
Courtesy of Tierra Tech
This ultrasonic cleaning tank is used to clean saw blades, with the aid of a robot.
“Most of the applications we work with can be cleaned with an industrial, water-based, biodegradable, alkaline detergent,” said Steve Myers, vice president of engineering and technical services for equipment provider Ultrasonic Power Corp., Freeport, Ill. “It can be used on most metals.”
The rule of thumb is to use an alkaline cleanser when removing oils and metal chips, Myers explained. When removing calcium deposits or rust, a phosphoric acid-based cleanser, which is nonaggressive, works well.
Another concern is proper cleanser concentration in the solution. “Not every soap is the same,” said Tierra Tech’s Manley. “We produce one where the soap is 3 to 5 percent or more of the solution. So it is important when adding detergent to add the correct amount per the manufacturer’s guidelines for temperature and safety.”
Eventually, the solution will be exhausted after cleaning a certain number of parts and a user needs to change, or “recharge,” the solution. The process is simple: Drain the tank, fill it with fresh water and add detergent. An ultrasonic tank cleans itself when parts are cleaned, but the user must keep the equipment consoles clean and thoroughly rinse the tank before switching cleansers.
Bubble Generation
The cavitation process is affected by the design and construction of the transducers, generators and, to a lesser extent, the tank.
An ultrasonic generator converts a standard 60 Hz electrical frequency into high-frequency pulses from 20 to 200 KHz that are applied to transducers mounted to the tank. Most industrial ultrasonic cleaning uses 40 KHz as the base frequency.
The transducers expand and contract with these pulses, creating acoustic energy in the solution. It is this acoustic energy that creates the alternating high- and low-pressure sound waves leading to cavitation. During the low-pressure phase, the bubbles grow from microscopic size until, during the high-pressure phase, they compress and implode.
Low frequencies produce large bubbles with strong implosions for heavy-duty cleaning. For the most part, low frequencies have more energy per cavitation than high frequencies. That means low frequencies are more aggressive and can damage delicate parts.
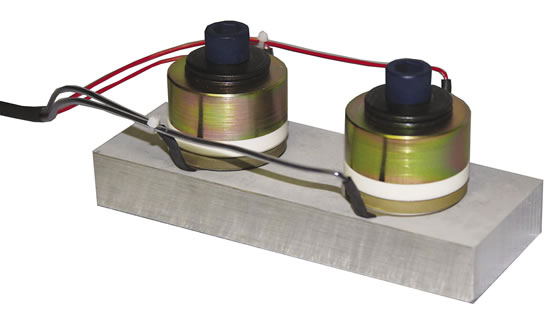
Courtesy of Ultrasonic Power
Multiple-frequency systems consist of two piezoelectric transducer stacks, which permit generation of simultaneous multiple frequencies.
The higher the frequency, the smaller the bubbles, with milder implosions for more delicate cleaning or for submicron-particulate removal.
“The lowest frequency we offer is 25 KHz,” said Crest’s Kaczorek. “On the high end, we offer 132 KHz, 192 KHz, 360 KHz, 470 KHz and even 1,000 KHz. Those units target specific industries and contaminants.”
Higher end ultrasonic cleaning systems use more advanced technologies, such as multiple frequency and sweep frequency. Multiple-frequency systems consist of two piezoelectric transducer stacks, which permit generation of simultaneous multiple frequencies.
“The two stacks resonate at 40 KHz,” UPC’s Myers said. “When they propagate into a bar in between the stack, in our case the Vibra-Bar, that bar’s natural kilohertz frequency mixes with the 40-KHz frequency, so you end up with a range of frequencies in the tank that go from the base frequency of 40 KHz up to 90 KHz. The higher frequencies initiate the cleaning by loosening contaminants in inaccessible areas, such as tapped holes and undercuts. This allows the lower frequencies to rapidly and thoroughly complete the cleaning operation.” Multiple-frequency systems from other high-end ultrasonic cleaning manufacturers operate somewhat differently, but the principle is the same.
Sweep-frequency circuitry drives the transducers between a bandwidth slightly greater and slightly less than the resonant frequency. This eliminates standing waves in the tank. “We have a set resonance frequency with a 1-KHz frequency sweep around that resonance,” Frank said. “Cavitation occurs between the high- and low-pressure waves. A single unswept frequency produces specific wavelengths within the solution, resulting in areas of high-intensity cavitation and dead spots where little to no cavitation occurs. Sweeping the frequency continuously changes the wavelength, resulting in even cavitation intensity throughout the tank.”
Depending on the manufacturer, sweep frequencies range from ±0.5 KHz to ±1 KHz to ±2 KHz.
There are two types of ultrasonic transducers used in ultrasonic cleaning systems: the more common piezoelectric and magnetostrictive. Blue Wave uses magnetostrictive transducers, which are known for their durability.
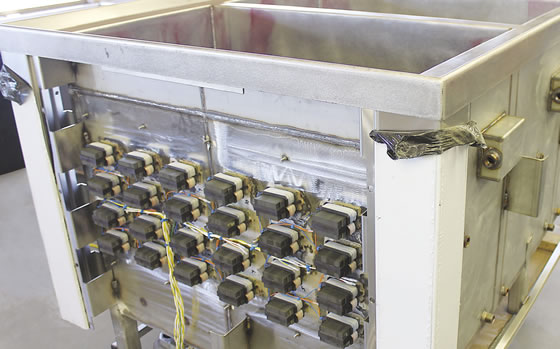
Courtesy of Blue Wave Ultrasonics
This Blue Wave ultrasonic cleaning tank is constructed with 24 magnetostrictive transducers welded directly to the tank wall.
Tank size depends on the size or quantity of the parts being cleaned. The number of transducers and generators employed is determined by the tank size. Typical tanks range from 5 to 1,000 gal., and some are even larger.
In general, smaller tanks require fewer watts per gallon or lower watt density. But the pressure waves required to create cavitation are reflected off the tank walls and tank surface. Larger tanks, with larger wall and surface areas, are more efficient at reflecting the pressure waves, lowering the watt density required to create effective cavitation. This is a general rule but tank geometry and parts to be cleaned should also be considered when determining the proper watt density.
Loading Parts
How the parts are placed in the tank is almost as important as the temperature, detergent and cavitation itself, according to Frank, who added that the solution must be able to contact every surface.
Some parts require individual fixturing to separate them for cleaning or subsequent processes. Large batches of small parts may require a rotating fixture that slowly tumbles the parts during the process, ensuring that all part surfaces are exposed to the ultrasonic cavitation.
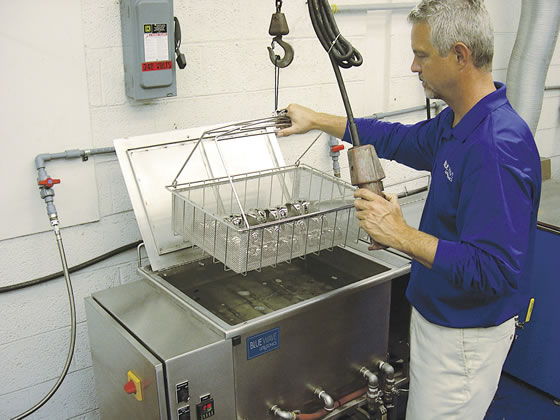
Courtesy of Blue Wave Ultrasonics
How parts are loaded in an ultrasonic cleaning system is important to make sure the solution contacts every surface.
In addition, Kaczorek recommends only filling a basket 30 to 40 percent full to achieve homogeneous distribution of the cavitation. Also, never place parts directly on the surface where the transducers are mounted because it would block the cavitation process. And there should be about an inch of space from the top of the tank to where the solution is for better efficiency.
The ultrasonic cleaning process also includes rinsing of residual detergent and drying parts. Rinsing may be as simple as using an ambient-temperature immersion rinse with tap water or a more involved process consisting of an ultrasonic rinse followed by multiple heated immersion rinse tanks utilizing deionized water.
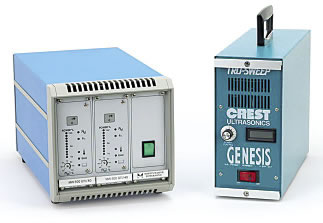
Courtesy of Crest Ultrasonics
An ultrasonic generator converts standard electrical frequency into high-frequency pulses that are applied to transducers mounted to the tank.
The drying process may involve simply blowing the parts with compressed air or may require a forced, heated-air dryer capable of temperatures hot enough to boil off excess rinse water.
If all this sounds complicated, it is. Most industrial ultrasonic cleaning equipment manufacturers have an applications lab where they can develop a proper ultrasonic cleaning process for an individual customer using past experience and trial and error on the new process.
“That is where some customers get frustrated,” UPC’s Myers said. “They buy a system but don’t talk to the manufacturer about how to make it work best. If they have an application that is pretty complex, that is where they want to look at tweaking the process.” CTE
About the Author: Susan Woods is a contributing editor for CTE. Contact her at (224) 225-6120 or [email protected].
Detecting proper cavitation via sensors—or aluminum foil
One way to ensure the best performance from ultrasonic cleaning equipment is to test if the unit is cavitating properly. Sensors placed in the tank to read the cavitation levels can be used to run that test.
Or, you can just use the aluminum foil test. “This test has been around forever but it’s still the easiest way to tell if you have good cavitation levels in your tank,” said Steve Myers of Ultrasonic Power Corp. “You take a sheet of aluminum, the cheapest one because it has the best resolution, and stick it in the tank for about 20 seconds. When you pull it out, it should look like an orange peel (a dimpled surface) consistently across the sheet. If not, there are dead zones [in the tank].”
This test is also suitable for periodic cavitation checks to determine if the equipment is working as it did when new. Myers said, “If you do a baseline test and keep it on file, then every 6 months or so you can do a test and compare the results to see if your system is losing performance.”
Contributors
Blue Wave Ultrasonics
(800) 373-0144
www.bluewaveinc.com
Crest Ultrasonics Corp.
(800) 992-7378
www.crest-ultrasonics.com
Tierra Tech USA
(214) 662-3692
www.tierratech.com
Ultrasonic Power Corp.
(800) 575-0168
www.upcorp.com
Related Glossary Terms
- cutting fluid
cutting fluid
Liquid used to improve workpiece machinability, enhance tool life, flush out chips and machining debris, and cool the workpiece and tool. Three basic types are: straight oils; soluble oils, which emulsify in water; and synthetic fluids, which are water-based chemical solutions having no oil. See coolant; semisynthetic cutting fluid; soluble-oil cutting fluid; synthetic cutting fluid.
- fixture
fixture
Device, often made in-house, that holds a specific workpiece. See jig; modular fixturing.
- sawing machine ( saw)
sawing machine ( saw)
Machine designed to use a serrated-tooth blade to cut metal or other material. Comes in a wide variety of styles but takes one of four basic forms: hacksaw (a simple, rugged machine that uses a reciprocating motion to part metal or other material); cold or circular saw (powers a circular blade that cuts structural materials); bandsaw (runs an endless band; the two basic types are cutoff and contour band machines, which cut intricate contours and shapes); and abrasive cutoff saw (similar in appearance to the cold saw, but uses an abrasive disc that rotates at high speeds rather than a blade with serrated teeth).
- tap
tap
Cylindrical tool that cuts internal threads and has flutes to remove chips and carry tapping fluid to the point of cut. Normally used on a drill press or tapping machine but also may be operated manually. See tapping.
- ultrasonic cleaning
ultrasonic cleaning
Method of cleaning metal or plastic parts by immersing them in an aqueous or solvent-based cleaning solution and imposing ultrasound energy on the bath to enhance cleaning by creating cavitation conditions at the part surface, which imparts a strong scouring action to remove tenacious soils.