Honing, alongside grinding and lapping, is one of the primary finishing processes used in most machine shops. Of the three, honing is often the most capable yet underutilized operation, offering precision and versatility in a variety of applications.
What is Honing?
Honing removes material from a workpiece through abrasion, utilizing tools embedded with abrasives like aluminum oxide, CBN, and diamond. These abrasives are typically formed into solid shapes, commonly referred to as “stones.” Unlike grinding, which operates at cutting speeds starting around 5,000 sfm (1,524 m/min), honing is performed at much lower speeds, starting at about 65 sfm (19.8 m/min).
Advantages of Honing Over Other Processes
- Material Removal Rates: Honing matches or exceeds the material removal rates of grinding for fine finishes.
- Precision: Honing is ideal for accurately removing small amounts of material with tolerances as tight as 0.0002" (0.051 mm).
- Heat Management: Lower cutting speeds generate less heat, preventing damage to delicate parts like gear teeth.
- Portability: Honing tools can be used outside the shop with simple electric drill motors.
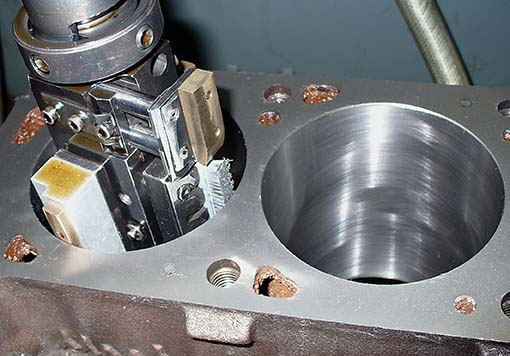
Engine reconditioned with a Sunnen CV-616 automatic cylinder hone. Image courtesy of Galloway Engine Reconditioning.
Applications of Honing
1. Cylinders and Hydraulic Components
Honing is synonymous with finishing cylindrical components, such as engine and hydraulic cylinders. This process imparts a crosshatched surface pattern, which effectively holds lubricant while preventing leaks under high pressure. For example, honing enables precision in hydraulic pumps operating at pressures up to 5,000 psi (345 bar).
2. Correcting Geometry Issues
Honing tools use long stones with significant engagement in the bore, allowing them to self-center and correct out-of-roundness or misaligned holes. This capability is particularly useful for deep bores with high length-to-diameter ratios, which can be challenging to machine with other processes.
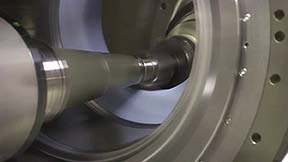
Gear honing with a Gleason-Hurth 150SPH-L Spheric gear honing machine. Image courtesy of Gleason Corp.
3. Gear Teeth Finishing
Honing is increasingly used in automotive gear manufacturing to produce quieter, longer-lasting gears. Unlike grinding, honing eliminates heat-related issues, such as heat-affected zones, while improving the surface finish and geometry of gear teeth. This is especially critical in hybrid and electric vehicles, where gear noise is more noticeable.
Cost Effectiveness of Honing
Honing can be a cost-effective process, particularly for smaller or manual operations. Used machines suitable for aerospace or industrial components can be purchased for under $2,500. Abrasive stones, mandrels, and other tools are widely available, keeping operational costs manageable. For larger-scale operations requiring automation, the costs may rise but remain competitive compared to other machining methods.
Conclusion
Honing stands out as a versatile, precise, and cost-effective finishing process. Whether you're finishing cylinders, correcting bore geometry, or perfecting gear teeth, honing offers unique advantages that make it indispensable in modern manufacturing. Its combination of low heat generation, high precision, and portability ensures it remains a valuable tool for both industrial and field applications.
Contact Details
Contact Details
Related Glossary Terms
- abrasive
abrasive
Substance used for grinding, honing, lapping, superfinishing and polishing. Examples include garnet, emery, corundum, silicon carbide, cubic boron nitride and diamond in various grit sizes.
- aluminum oxide
aluminum oxide
Aluminum oxide, also known as corundum, is used in grinding wheels. The chemical formula is Al2O3. Aluminum oxide is the base for ceramics, which are used in cutting tools for high-speed machining with light chip removal. Aluminum oxide is widely used as coating material applied to carbide substrates by chemical vapor deposition. Coated carbide inserts with Al2O3 layers withstand high cutting speeds, as well as abrasive and crater wear.
- cubic boron nitride ( CBN)
cubic boron nitride ( CBN)
Crystal manufactured from boron nitride under high pressure and temperature. Used to cut hard-to-machine ferrous and nickel-base materials up to 70 HRC. Second hardest material after diamond. See superabrasive tools.
- grinding
grinding
Machining operation in which material is removed from the workpiece by a powered abrasive wheel, stone, belt, paste, sheet, compound, slurry, etc. Takes various forms: surface grinding (creates flat and/or squared surfaces); cylindrical grinding (for external cylindrical and tapered shapes, fillets, undercuts, etc.); centerless grinding; chamfering; thread and form grinding; tool and cutter grinding; offhand grinding; lapping and polishing (grinding with extremely fine grits to create ultrasmooth surfaces); honing; and disc grinding.
- lapping
lapping
Finishing operation in which a loose, fine-grain abrasive in a liquid medium abrades material. Extremely accurate process that corrects minor shape imperfections, refines surface finishes and produces a close fit between mating surfaces.