Based in the Bavarian town of Waakirchen, Germany, Werkzeugschleiferei Hugo Limmer produces a variety of carbide, ceramic and cermet standard and custom cutting tools and provides resharpening services for the mechanical engineering, aerospace and medical industries.
To improve the toolmaker’s production processes, company founder Hugo Limmer wanted a grinding oil that reduced cycle times, grinding wheel dressing intervals, machine idle times and scrap while improving process security and worker health and safety. He contacted a business partner of Stuttgart, Germany-based Blaser Swisslube GmbH for a solution. Together, they examined the grinding processes, looked for ways to optimize operations and decided to test Blaser Swisslube’s Blasogrind GTC 7 grinding oil in one of the toolmaker’s grinders.
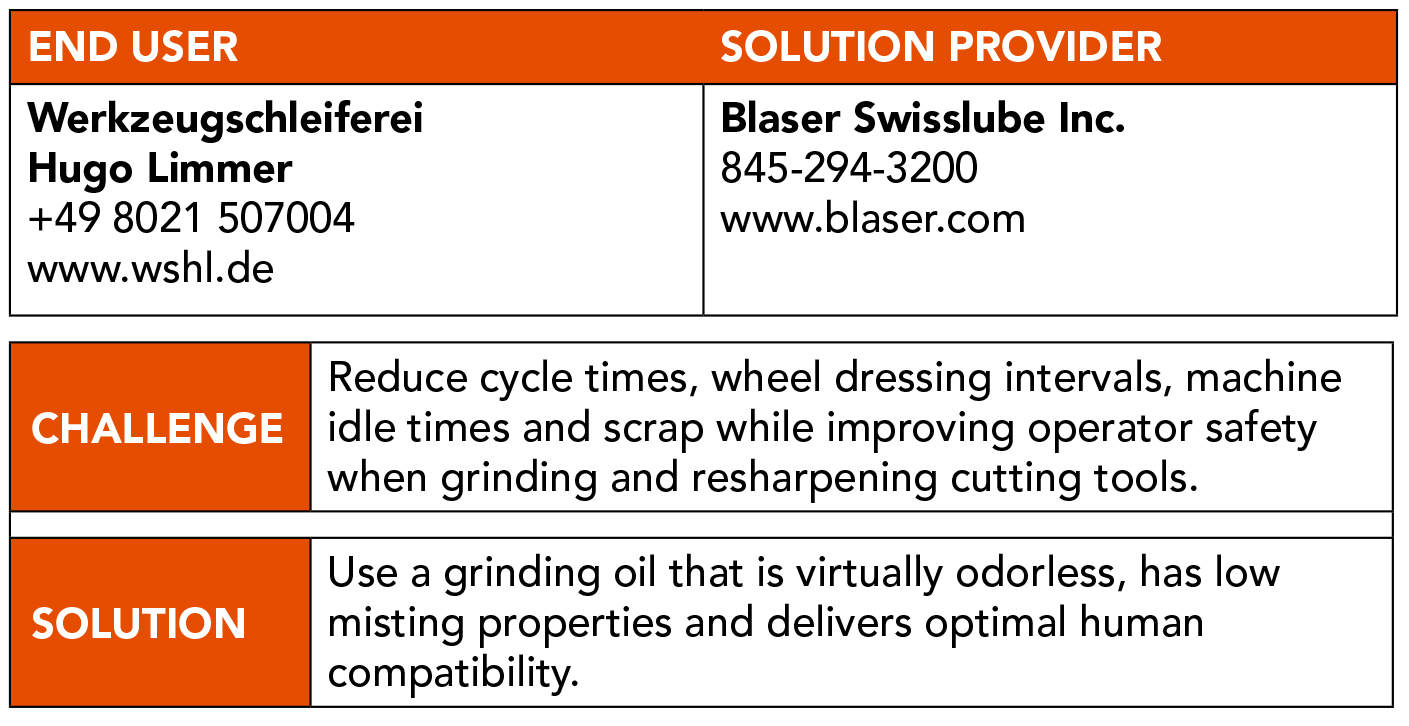
Tom Cappadona, product manager for gears, grinding and EDM at Blaser Swisslube Inc. in Goshen, New York, said the coolant manufacturer’s testing procedure involves performing a grinding operation with a Blaser Swisslube oil using the same parameters used for the competitor’s oil and then increasing the feed rate to reduce the cycle time when producing parts to the required level of quality, such as achieving the specified surface finish with no burns.
He said Blaser Swisslube’s Liquid Tool analyzer allows existing conditions and costs to be documented and enables a projection to be made of what the company believes that it can achieve, which it calls a value proposal.
“After the test is completed, we do what is called a value communication,” Cappadona said, “which verifies exactly what we were able to achieve, so the customer has one piece of paper showing the savings they can achieve.”
Limmer said the new oil needed to be virtually odorless, have low misting properties and deliver optimal human compatibility.
“At the same time,” he said, “we wanted to continuously improve productivity and quality to get the most out of the available resources and in this way add economic value.”
By switching to Blasogrind GTC 7 grinding oil, machine efficiency improved by 15%.
Cappadona said increasing throughput means that a manufacturer does not have to purchase additional machine tools and hire more workers to operate those machines as product demand increases.
“It clearly saves them money at the end of the day,” he said. “Time is the No. 1 thing we are after, and it always, always, always overcomes the cost of the oil. The oil may be more expensive, but you get the money back based on performance.”
Blasogrind GTC 7 reportedly contributes to a savings of nearly $80,000 per year at Werkzeugschleiferei Hugo Limmer.
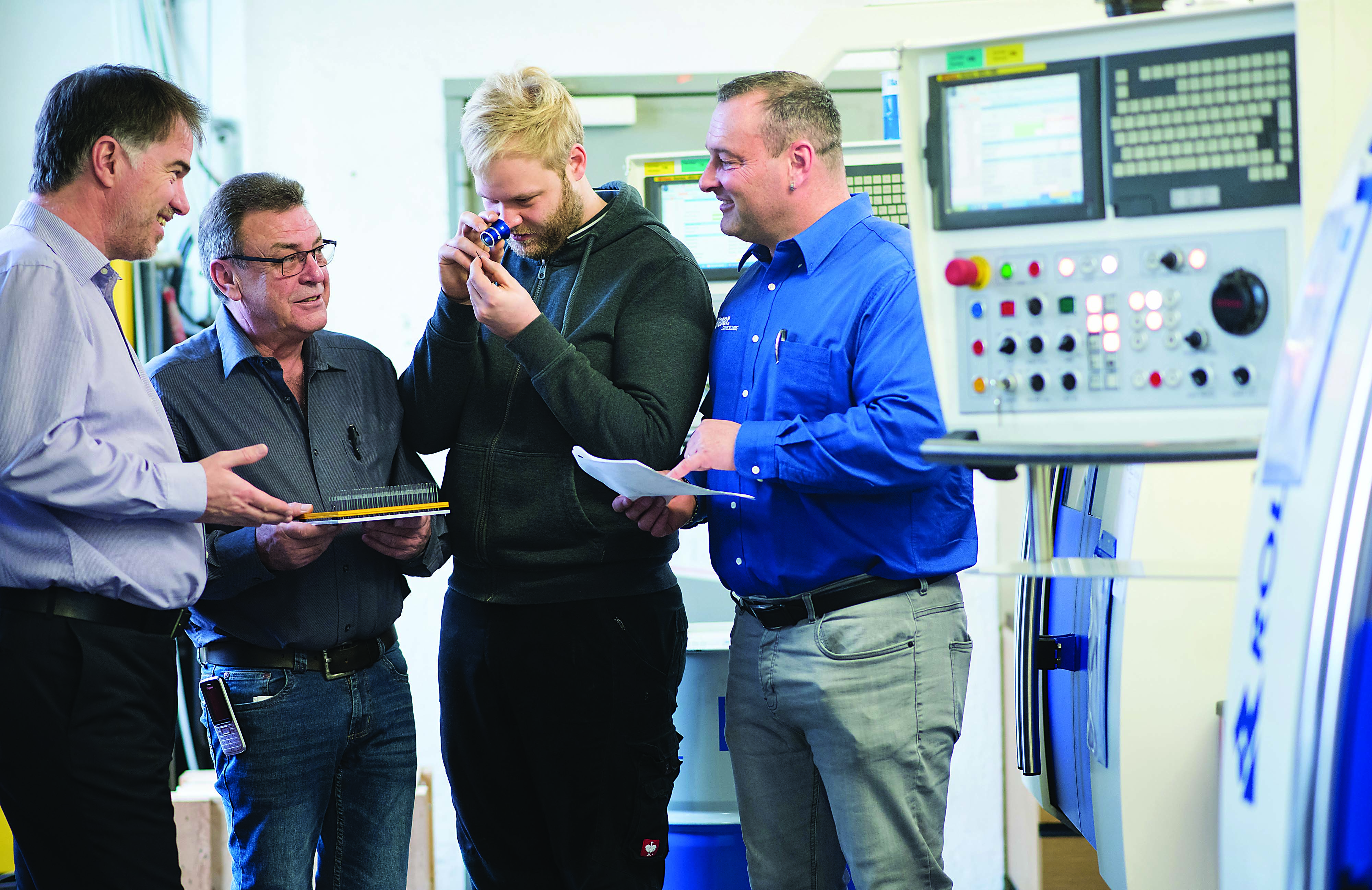
A grinding oil that is well matched to all parameters, including the workpiece material, grinding wheels, machines and machining environment, can significantly impact the entire production process, said Martin Reichhart, application engineer for Blaser Swisslube.
“That’s why we examine all the details in order to find the ideal metalworking fluid,” he said. “When used correctly and complemented by customized services, the right metalworking fluid increases overall productivity.”
According to Blaser Swisslube, Blasogrind GTC 7 is formulated to achieve high material removal rates, long dressing intervals and fine surface finishes. The oil also minimizes cobalt leaching, and fast air release promotes optimal cooling performance and prevents microcracks from forming in tools.
Cappadona said unlike some of the company’s predecessor products derived from crude oil, Blasogrind GTC 7 is a newer-generation gas-to-liquid product derived from natural gas.
“It starts out as natural gas,” he said, “eliminating all those impurities that come out of crude. We assemble those natural gas molecules to get the base oil that we want and then add the additives to get the formulation we are looking for. It is a much purer oil than some of the older-generation oils.”
Cappadona said if there is any mist with the gas-to-liquid oil, the droplets dissipate faster than those found in a fine mist, which can remain airborne and land on an operator if a grinding machine’s mist collection system isn’t adequate.
“It doesn’t feel oily,” he said. “It has a very gentle feel, and that is a benefit of the gas-to-liquid technology. It reduces skin irritation and dermatitis.”
Contact Details
Related Glossary Terms
- coolant
coolant
Fluid that reduces temperature buildup at the tool/workpiece interface during machining. Normally takes the form of a liquid such as soluble or chemical mixtures (semisynthetic, synthetic) but can be pressurized air or other gas. Because of water’s ability to absorb great quantities of heat, it is widely used as a coolant and vehicle for various cutting compounds, with the water-to-compound ratio varying with the machining task. See cutting fluid; semisynthetic cutting fluid; soluble-oil cutting fluid; synthetic cutting fluid.
- dressing
dressing
Removal of undesirable materials from “loaded” grinding wheels using a single- or multi-point diamond or other tool. The process also exposes unused, sharp abrasive points. See loading; truing.
- electrical-discharge machining ( EDM)
electrical-discharge machining ( EDM)
Process that vaporizes conductive materials by controlled application of pulsed electrical current that flows between a workpiece and electrode (tool) in a dielectric fluid. Permits machining shapes to tight accuracies without the internal stresses conventional machining often generates. Useful in diemaking.
- feed
feed
Rate of change of position of the tool as a whole, relative to the workpiece while cutting.
- grinding
grinding
Machining operation in which material is removed from the workpiece by a powered abrasive wheel, stone, belt, paste, sheet, compound, slurry, etc. Takes various forms: surface grinding (creates flat and/or squared surfaces); cylindrical grinding (for external cylindrical and tapered shapes, fillets, undercuts, etc.); centerless grinding; chamfering; thread and form grinding; tool and cutter grinding; offhand grinding; lapping and polishing (grinding with extremely fine grits to create ultrasmooth surfaces); honing; and disc grinding.
- grinding wheel
grinding wheel
Wheel formed from abrasive material mixed in a suitable matrix. Takes a variety of shapes but falls into two basic categories: one that cuts on its periphery, as in reciprocating grinding, and one that cuts on its side or face, as in tool and cutter grinding.
- land
land
Part of the tool body that remains after the flutes are cut.
- metalworking
metalworking
Any manufacturing process in which metal is processed or machined such that the workpiece is given a new shape. Broadly defined, the term includes processes such as design and layout, heat-treating, material handling and inspection.