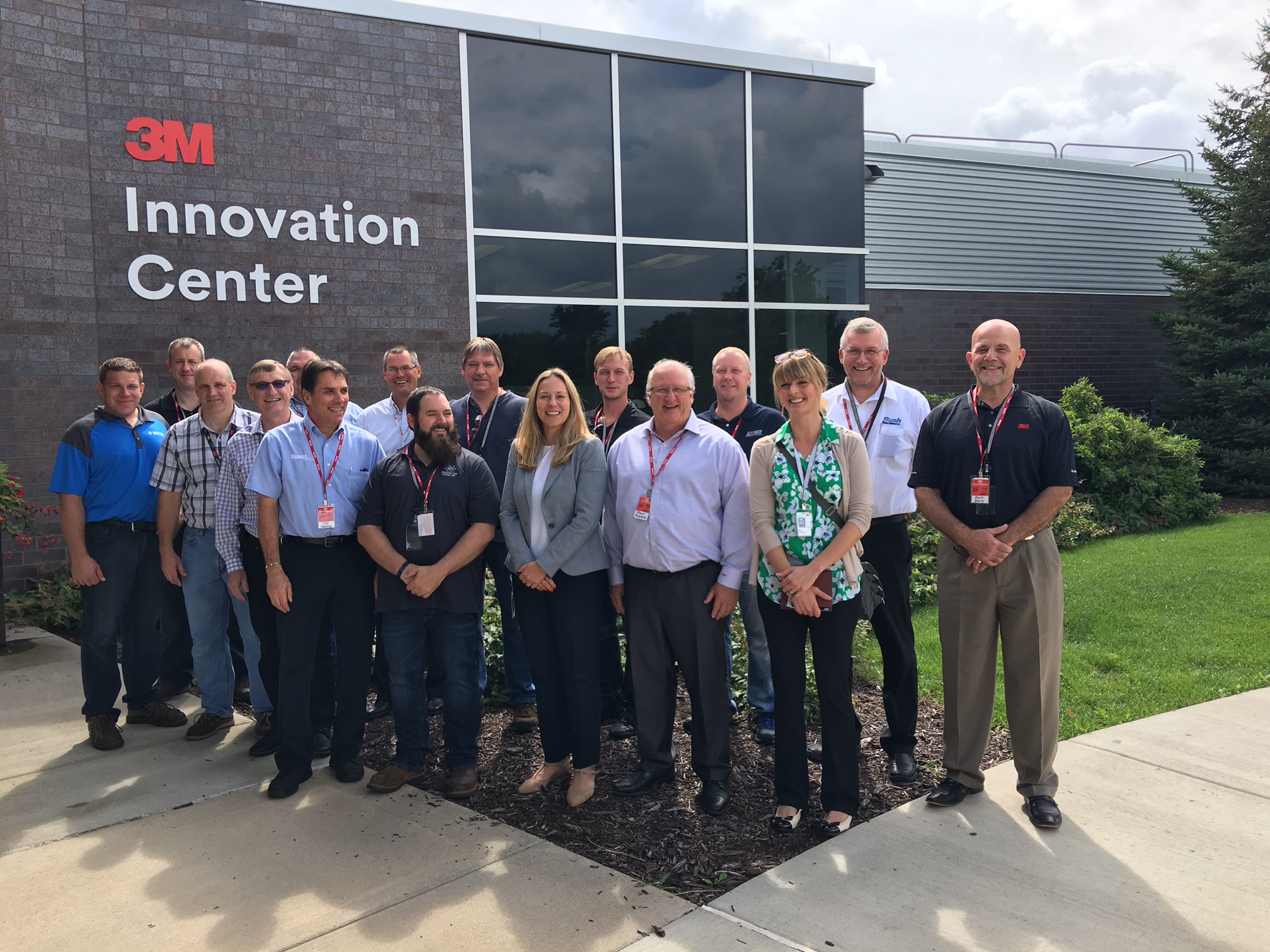
Historically, the round tool cutting industry hasn’t offered many educational events to customers for collaboration. 3M is on a mission to change that.
Aug. 10-11, 2017, 3M’s Precision Grinding & Finishing business hosted its first annual 2-day Round Tool Technology seminar at 3M’s headquarters in St. Paul, Minn., creating an open forum for customers, manufacturers and suppliers from across the country to come together and learn about tool grinding technologies.
“Technology is undeniably changing the tool grinding landscape, and we understand how our customers can benefit from learning about these advancements,” said Nick Orf, marketing manager for 3M Precision Grinding & Finishing. “Our interactive seminar gave participants the opportunity to get ahead in the industry—to learn from, and collaborate with, both peers and experts.”
ANCA Inc., Rush Machinery and Blaser Swisslube partnered with 3M for this event to present their best practices for grinding optimization, while also speaking to current issues facing customers.
Session topics covered many aspects of the grinding process from wheel design, technology and use by 3M manufacturing and application experts, Janusz Hajduk and Richard Crowley, to the future of CNC machine grinding technology presented by Russell Riddiford, president of ANCA. Grinding wheel profiling methods were outlined by Rob Robbins, sales manager at Rush Machinery and Paul Christy of 3M, while Jed DeJong, application manager at Blaser Swisslube, discussed the importance of coolant selection and application optimization techniques.
Throughout the seminar, sessions incorporated peer-driven group discussions as well as hands-on training in 3M’s Customer Abrasive Methods training center. Event attendees found value in the collaboration and productive technical discussions.
“What’s so vital about the collaboration is the support and confirmation from the industry experts,” said Joshua Weber, Superior Tool Service Inc. “We’re all doing our own research and testing, so to have a wheel dressing company and a grinding wheel company verify and back up your testing results is extremely beneficial. They might come across something and realize a variable that you don’t find or think about; then, that clicks and brings it all together.”
Mark Morrie, president of Scrimger Sales added: “The people here are very knowledgeable about our industry. Whether it’s offline dressing, fluting carbide, coolants―everything you need―the answers are right here for you. This type of back-and-forth, question and answer forum is very beneficial. And, the camaraderie with everyone is the best.”
For questions about the event or interest in attending 3M’s 2018 Round Tool Technology Seminar, contact Nicholas Orf, marketing manager for 3M ASD, Precision Grinding & Finishing, at [email protected].
Contact Details
Related Glossary Terms
- abrasive
abrasive
Substance used for grinding, honing, lapping, superfinishing and polishing. Examples include garnet, emery, corundum, silicon carbide, cubic boron nitride and diamond in various grit sizes.
- computer numerical control ( CNC)
computer numerical control ( CNC)
Microprocessor-based controller dedicated to a machine tool that permits the creation or modification of parts. Programmed numerical control activates the machine’s servos and spindle drives and controls the various machining operations. See DNC, direct numerical control; NC, numerical control.
- coolant
coolant
Fluid that reduces temperature buildup at the tool/workpiece interface during machining. Normally takes the form of a liquid such as soluble or chemical mixtures (semisynthetic, synthetic) but can be pressurized air or other gas. Because of water’s ability to absorb great quantities of heat, it is widely used as a coolant and vehicle for various cutting compounds, with the water-to-compound ratio varying with the machining task. See cutting fluid; semisynthetic cutting fluid; soluble-oil cutting fluid; synthetic cutting fluid.
- dressing
dressing
Removal of undesirable materials from “loaded” grinding wheels using a single- or multi-point diamond or other tool. The process also exposes unused, sharp abrasive points. See loading; truing.
- fluting
fluting
Cutting straight or spiral grooves in drills, endmills, reamers and taps to improve cutting action and remove chips.
- grinding
grinding
Machining operation in which material is removed from the workpiece by a powered abrasive wheel, stone, belt, paste, sheet, compound, slurry, etc. Takes various forms: surface grinding (creates flat and/or squared surfaces); cylindrical grinding (for external cylindrical and tapered shapes, fillets, undercuts, etc.); centerless grinding; chamfering; thread and form grinding; tool and cutter grinding; offhand grinding; lapping and polishing (grinding with extremely fine grits to create ultrasmooth surfaces); honing; and disc grinding.
- grinding wheel
grinding wheel
Wheel formed from abrasive material mixed in a suitable matrix. Takes a variety of shapes but falls into two basic categories: one that cuts on its periphery, as in reciprocating grinding, and one that cuts on its side or face, as in tool and cutter grinding.
- profiling
profiling
Machining vertical edges of workpieces having irregular contours; normally performed with an endmill in a vertical spindle on a milling machine or with a profiler, following a pattern. See mill, milling machine.