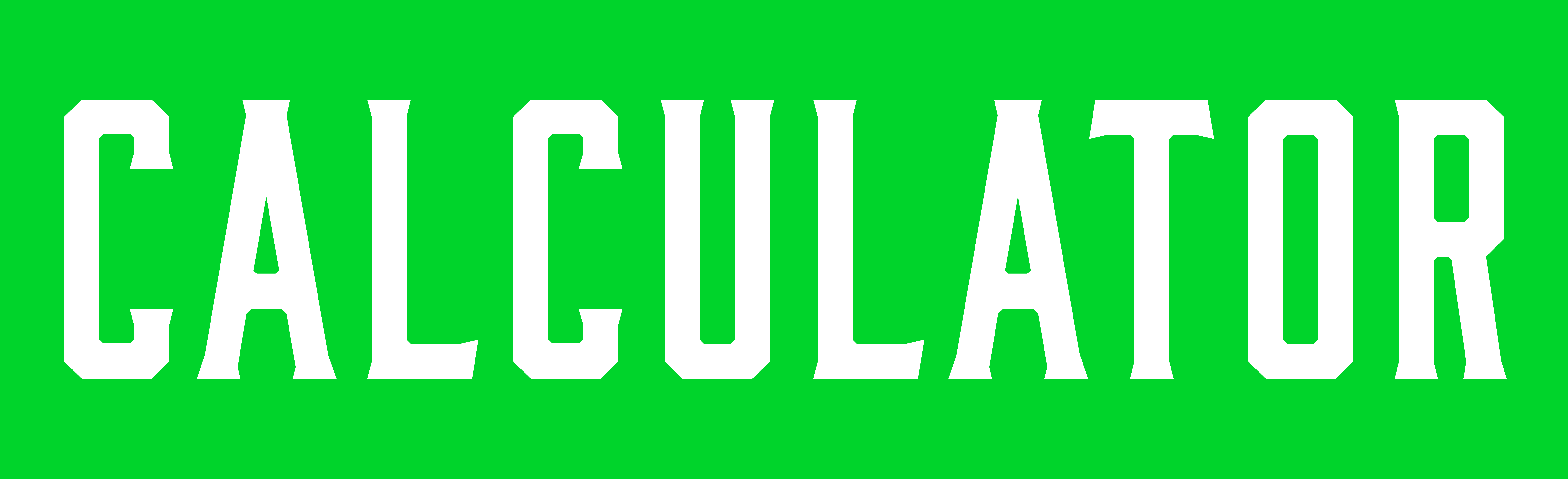
Using a new calculation for determining cutting force components and power when turning.
All images courtesy Kennametal
The cutting force when turning is a resultant force that combines tangential, feed and radial force components. These force components can be measured with a three-component force dynamometer. Metalcutting professionals consider Kistler dynamometers the most accurate.
Of the three cutting force components, the tangential force (FZ) is the greatest, the feed force (FY) is less in magnitude and the radial force (FX) is the least in magnitude. As a rule of thumb, the following relationships are used, but it is not a good practice because the results are not as accurate as they could be: FY = 0.50FZ and FX = 0.25FZ.
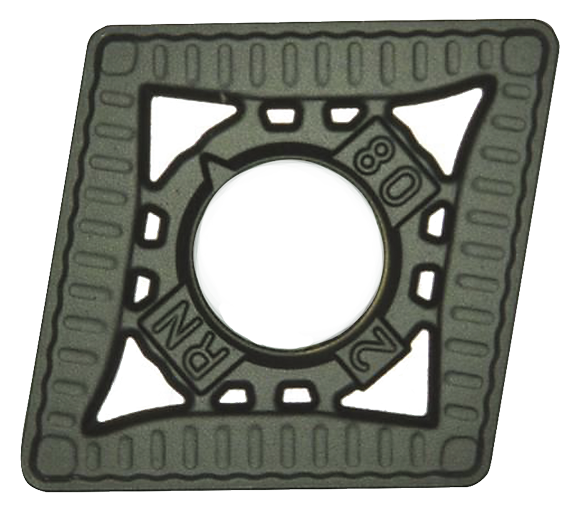
A Kennametal CNMG 120408 RN insert was applied for the roughing test.
On Oct. 25, 2012, Kennametal conducted lab tests at its facility in Fürth, Germany, turning 218-HB alloy steel AISI 4140 (DIN 1.7225 42CrMo4), with the following indexable inserts (ISO specification is in the metric system):
• CNMG 120408 RN for roughing, carbide grade is KCP10;
• CNMG 120408 MN for semifinishing, carbide grade is KCP10; and
• CNMG 120408 FP for finishing, carbide grade is KCP10.
A Boehringer VDF315C CNC lathe and a Kistler quartz-crystal, three-component toolholder dynamometer, type Z15814, were used for the lab tests. The lathe has 80kW (107 hp) of power, 1,400 Nm (1,032 ft.-lbs.) of torque and a VDI 60 turret. The cutting force components (FX, FY and FZ) were recorded (Charts 1, 2 and 3 for roughing below) and tabulated (Tables 1, 2 and 3 below).
The ratios of the feed force to tangential force and the radial force to tangential force are (Table 1):
Test No. 1: FY ÷ FZ = 2,309.42 ÷ 5,358.77 = 0.43; FY = 0.43FZ; FX ÷ FZ = 887.13 ÷ 5358.77 = 0.17; FX = 0.17FZ
Test No. 2: FY ÷ FZ = 2,219.69 ÷ 5,119.33 = 0.43; FY = 0.43FZ; FX ÷ FZ = 919.39 ÷ 5,119.33 = 0.18; FX = 0.18FZ
Test No. 3: FY ÷ FZ = 2,247.57 ÷ 5,113.66 = 0.44; FY = 0.44FZ; FX ÷ FZ = 958.56 ÷ 5,113.66 = 0.19; FX = 0.19FZ
These ratios are 14 to 32 percent lower than those defined by the rule of thumb.
Similar ratios for the cutting force components are (Table 2):
Test No. 1: FY ÷ FZ = 1,479.75 ÷ 3,060.21 = 0.48; FY = 0.48FZ; FX ÷ FZ = 556.12 ÷ 3,060.21 = 0.18; FX = 0.18FZ
Test No. 2: FY ÷ FZ = 1,482.56 ÷ 3,038.97 = 0.49; FY = 0.49FZ; FX ÷ FZ = 576.00 ÷ 3,038.97 = 0.19; FX = 0.19FZ
Test No. 3: FY ÷ FZ = 1,507.77 ÷ 3,063.95 = 0.49; FY = 0.49FZ; FX ÷ FZ = 600.88 ÷ 3,063.95 = 0.20; FX = 0.20FZ
These ratios are 4 to 28 percent lower than those defined by the rule of thumb.
The ratios of the cutting force components are (Table 3):
Test No. 1: FY ÷ FZ = 491.08 ÷ 957.37 = 0.51; FY = 0.51FZ; FX ÷ FZ = 234.86 ÷ 957.37 = 0.25; FX = 0.25FZ
Test No. 2: FY ÷ FZ = 483.72 ÷ 941.74 = 0.51; FY = 0.51FZ; FX ÷ FZ = 236.17 ÷ 941.74 = 0.25; FX = 0.25FZ
Test No. 3: FY ÷ FZ = 496.01 ÷ 957.27 = 0.52; FY = 0.52FZ; FX ÷ FZ = 240.11 ÷ 957.27 = 0.25; FX = 0.25FZ
These ratios are similar to those defined by the rule of thumb.
As shown in Tables 1, 2 and 3, the formula developed by Edmund Isakov provides 96.1 to 99.0 percent accuracy when calculating tangential force. Such accuracy satisfies engineering requirements for metalcutting.
The method of calculating power requirements using tangential force (FZC) and cutting speed (VC) is more accurate than the conventional, rule-of-thumb method, which is based on the unit power values (UP) and the metal-removal rates. A comparison of these two methods of calculation illustrates the difference.
Power Requirements
Calculating the power requirement P using FZC and VC is the advanced method. As an example, the calculations are performed using cutting parameters shown in Table 1 for roughing.
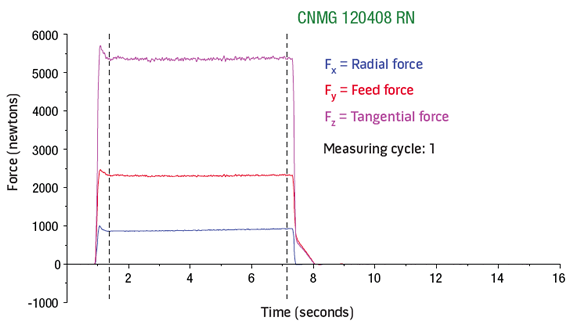
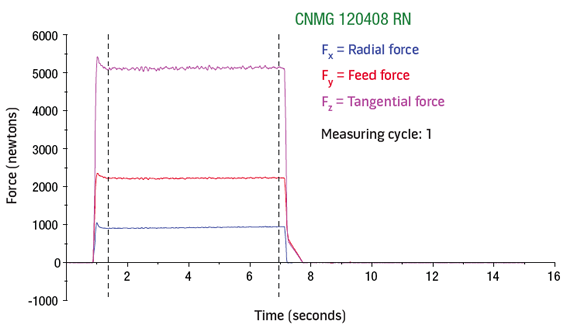
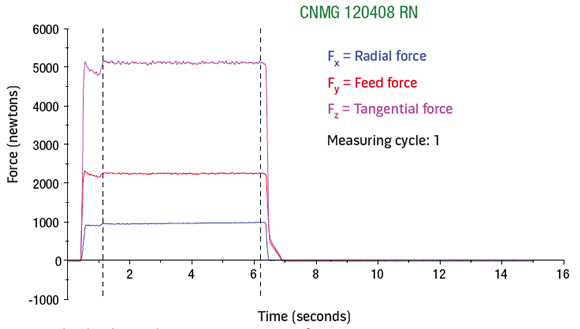
Charts 1 (top), 2 (middle) and 3. Measuring data for roughing output by the dynamometer.
Calculated tangential force FZC = 1,172.42 lbs. (5,215.18 N)
Cutting speed VC = 800 sfm (244 m/min.)
The U.S. units of measurement are:
P = FZC × VC ÷ 33,000 = 1,172.42 × 800 ÷ 33,000 = 28.42 hp
The metric units of measurement are:
P = FZC × VC ÷ 60,000 = 5,215.18 × 244 ÷ 60,000 = 21.21kW
Calculating the power requirement P using UP and mrr is the conventional method.
The unit power values for turning on 218-HB alloy steel 4140 (DIN 1.1724) are taken from Table 4.
The U.S. units of measurement are:
P = UP × mrr, where UP = 0.98 hp/in.3/min. (for a sharp tool)
mrr = DOC × f × 12 × VC = 0.200 × 0.020 × 12 × 800 = 38.40 in.3/min.
Power requirement is P = 0.98 × 38.40 = 37.63 hp
The metric units of measurement are:
P = UP × mrr, where UP = 0.044 kW/cm3/min. (for a sharp tool)
mrr = DOC × f × VC = 5.08 × 0.51 × 244 = 632.16 cm3/min.
The power requirement is P = 0.044 × 632.16 = 27.82kW
The results of calculating the power requirements are shown in Table 5, which indicates the conventional method overestimates the power requirements by 32 percent.
Because of a possible patent pending for the method of determining tangential force, the power requirement and a calculator operating in accordance with the method, the formula for the tangential force is not disclosed in this article.
As shown in Table 4, a given unit power value can be used for wide ranges of feed rate and hardness. For example, the unit power of 0.98 hp/in.3/min. is applicable for feed rates from 0.005 to 0.020 ipr and hardness numbers from 85 to 200 HB. The unit power data shown in Table 4 was determined in the late 1970s and those values were based on the cutting tool materials and geometries available at that time. If current cutting tool materials and geometries were used, the unit power values would be 30 to 40 percent lower. Therefore, the conventional method of calculating power requirements is not recommended. CTE
Turning Operation Power Requirement Calculator
Advanced Method (Tangential Force and Cutting Speed)
Tangential Force (FZC) in pounds-force (lbs):
Cutting Speed (VC) in surface feet per minute (sfm):
Power Requirement (hp):
Conventional Method (Unit Power and Material Removal Rate)
Unit Power (UP) in hp/in³/min:
Depth of Cut (DOC) in inches:
Feed Rate (f) in inches per revolution (ipr):
Cutting Speed (VC) in surface feet per minute (sfm):
Power Requirement (hp):
Formulae:
Advanced Method: Power (hp) = (Tangential Force, FZC × Cutting Speed, VC) ÷ 33,000
Conventional Method: Power (hp) = Unit Power, UP × Material Removal Rate, MRR
Where MRR = Depth of Cut (DOC) × Feed Rate (f) × 12 × Cutting Speed (VC)
About the Authors: Edmund Isakov (pictured), Ph.D., is a consultant, writer and frequent CTE contributor. He is the author of the books “Mechanical Properties of Work Materials” (Modern Machine Shop Publications, 2000); “Engineering Formulas for Metalcutting” (Industrial Press, 2004); “Cutting Data for Turning of Steel” (Industrial Press, 2009); the CD-ROM “International System of Units (SI)” (Industrial Press, 2012); and the software “Advanced Metalcutting Calculators” (Industrial Press, 2005). For more information, call (561) 369-4063 or visit www.edmundisakovphd.com. Kent P. Mizgalski is manager product engineering – turning for Kennametal Inc., Latrobe, Pa. Stefan Brand is a staff engineer in global machining technology for Kennametal GmbH, Fürth, Germany. For more information about the toolmaker’s products, call (800) 446-7738 or visit www.kennametal.com.
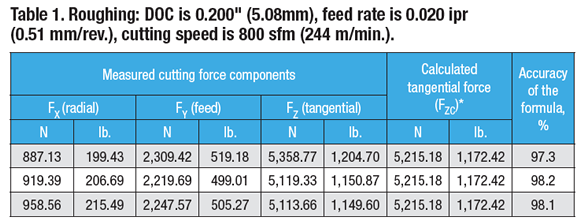
*Calculation of tangential force was performed using the formula developed by Edmund Isakov.
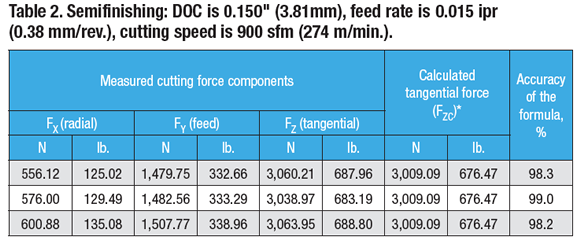
*Calculation of tangential force was performed using the formula developed by Edmund Isakov.
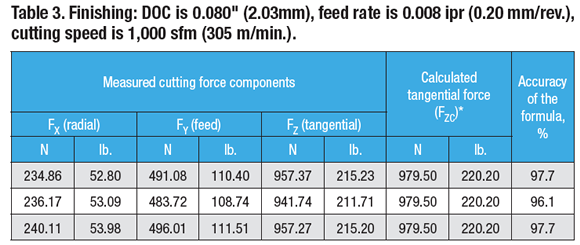
*Calculation of tangential force was performed using the formula developed by Edmund Isakov.
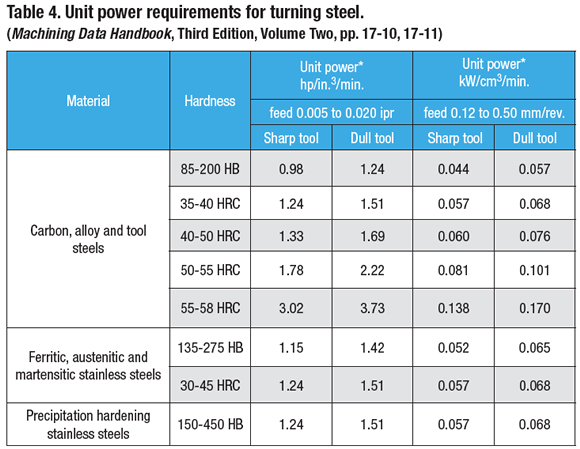
*Power requirements at the spindle drive motor, corrected for 90 percent spindle drive efficiency.
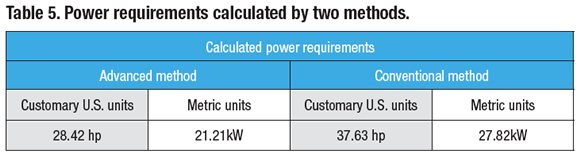
Related Glossary Terms
- Brinell hardness number ( HB)
Brinell hardness number ( HB)
Number related to the applied load (usually, 500 kgf and 3,000 kgf) and to the surface area of the permanent impression made by a 10mm ball indenter. The Brinell hardness number is a calculated value of the applied load (kgf) divided by the surface area of the indentation (mm2). Therefore, the unit of measure of a Brinell hardness number is kgf/mm2, but it is always omitted.
- computer numerical control ( CNC)
computer numerical control ( CNC)
Microprocessor-based controller dedicated to a machine tool that permits the creation or modification of parts. Programmed numerical control activates the machine’s servos and spindle drives and controls the various machining operations. See DNC, direct numerical control; NC, numerical control.
- cutting force
cutting force
Engagement of a tool’s cutting edge with a workpiece generates a cutting force. Such a cutting force combines tangential, feed and radial forces, which can be measured by a dynamometer. Of the three cutting force components, tangential force is the greatest. Tangential force generates torque and accounts for more than 95 percent of the machining power. See dynamometer.
- cutting speed
cutting speed
Tangential velocity on the surface of the tool or workpiece at the cutting interface. The formula for cutting speed (sfm) is tool diameter 5 0.26 5 spindle speed (rpm). The formula for feed per tooth (fpt) is table feed (ipm)/number of flutes/spindle speed (rpm). The formula for spindle speed (rpm) is cutting speed (sfm) 5 3.82/tool diameter. The formula for table feed (ipm) is feed per tooth (ftp) 5 number of tool flutes 5 spindle speed (rpm).
- cutting tool materials
cutting tool materials
Cutting tool materials include cemented carbides, ceramics, cermets, polycrystalline diamond, polycrystalline cubic boron nitride, some grades of tool steels and high-speed steels. See HSS, high-speed steels; PCBN, polycrystalline cubic boron nitride; PCD, polycrystalline diamond.
- depth of cut
depth of cut
Distance between the bottom of the cut and the uncut surface of the workpiece, measured in a direction at right angles to the machined surface of the workpiece.
- dynamometer
dynamometer
When drilling, a device for measuring the generated torque and axial force (thrust). When milling, a device for measuring the generated torque and feed force. When turning, a device for measuring the tangential, feed and radial forces.
- feed
feed
Rate of change of position of the tool as a whole, relative to the workpiece while cutting.
- hardness
hardness
Hardness is a measure of the resistance of a material to surface indentation or abrasion. There is no absolute scale for hardness. In order to express hardness quantitatively, each type of test has its own scale, which defines hardness. Indentation hardness obtained through static methods is measured by Brinell, Rockwell, Vickers and Knoop tests. Hardness without indentation is measured by a dynamic method, known as the Scleroscope test.
- lathe
lathe
Turning machine capable of sawing, milling, grinding, gear-cutting, drilling, reaming, boring, threading, facing, chamfering, grooving, knurling, spinning, parting, necking, taper-cutting, and cam- and eccentric-cutting, as well as step- and straight-turning. Comes in a variety of forms, ranging from manual to semiautomatic to fully automatic, with major types being engine lathes, turning and contouring lathes, turret lathes and numerical-control lathes. The engine lathe consists of a headstock and spindle, tailstock, bed, carriage (complete with apron) and cross slides. Features include gear- (speed) and feed-selector levers, toolpost, compound rest, lead screw and reversing lead screw, threading dial and rapid-traverse lever. Special lathe types include through-the-spindle, camshaft and crankshaft, brake drum and rotor, spinning and gun-barrel machines. Toolroom and bench lathes are used for precision work; the former for tool-and-die work and similar tasks, the latter for small workpieces (instruments, watches), normally without a power feed. Models are typically designated according to their “swing,” or the largest-diameter workpiece that can be rotated; bed length, or the distance between centers; and horsepower generated. See turning machine.
- mechanical properties
mechanical properties
Properties of a material that reveal its elastic and inelastic behavior when force is applied, thereby indicating its suitability for mechanical applications; for example, modulus of elasticity, tensile strength, elongation, hardness and fatigue limit.
- metalcutting ( material cutting)
metalcutting ( material cutting)
Any machining process used to part metal or other material or give a workpiece a new configuration. Conventionally applies to machining operations in which a cutting tool mechanically removes material in the form of chips; applies to any process in which metal or material is removed to create new shapes. See metalforming.
- toolholder
toolholder
Secures a cutting tool during a machining operation. Basic types include block, cartridge, chuck, collet, fixed, modular, quick-change and rotating.
- turning
turning
Workpiece is held in a chuck, mounted on a face plate or secured between centers and rotated while a cutting tool, normally a single-point tool, is fed into it along its periphery or across its end or face. Takes the form of straight turning (cutting along the periphery of the workpiece); taper turning (creating a taper); step turning (turning different-size diameters on the same work); chamfering (beveling an edge or shoulder); facing (cutting on an end); turning threads (usually external but can be internal); roughing (high-volume metal removal); and finishing (final light cuts). Performed on lathes, turning centers, chucking machines, automatic screw machines and similar machines.