Many trends affect the metalworking industry, including customer demands for the best quality, lowest cost and shortest delivery time. Design concepts for modular machine tools can address these expectations through general-function modules that can be combined to meet job requirements while reducing costs and lead times.
Modular machines benefit large production facilities with their ability to easily interlink and form work cells, while smaller facilities profit from their flexibility, with all users enjoying lower investment costs compared to custom, turnkey solutions. Available for chucked components and shaft workpieces, modular machines can increase production with their shared, basic designs.
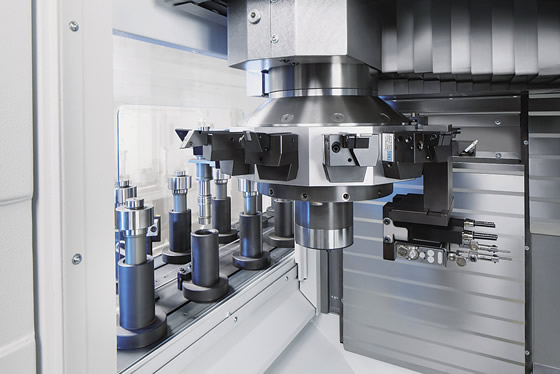
The work area of an EMAG modular machine tool. Image courtesy EMAG.
The goal behind EMAG’s modular concept was to develop a platform that enables engineers to form manufacturing cells easily while enhancing precision and productivity. Most importantly, modular machines offer more flexibility with the integration of a range of manufacturing technologies for an extensive product lineup, allowing quick and efficient changeover to meet evolving production requirements. This flexibility enables manufacturers to change the way they use modular machines over time.
The most obvious advantage is capitalizing on a shared operating and parts strategy. Regardless of the technology, these machines use identical components, from human/machine interfaces to drive controllers and motors, for their basic design. Not only does this allow end users to simplify operation, but also procurement because they reduce their spare-part inventories. This component-commonality strategy can increase profitability by reducing spare-part investment and warehousing costs.
Operators and mechanics benefit from the streamlined design as well. A modular machine speeds changeovers and maintenance to increase throughput. Because the base modules remain consistent, a modular design shortens the learning curve for new employees, as well as experienced workers when new machines are put into production.
Additionally, modular designs save floor space. Each machine has a compact design to minimize its footprint. This also allows them to be positioned close together. For loading and unloading workpieces, EMAG modular models feature integrated, automated pickup bands, or conveyor belts, at a uniform transfer height, simplifying the integration of robots and transfer units, if required.
Machine tool builders also see advantages to providing modular concepts. Not only do they benefit from the smaller component inventories that come with a common parts strategy, but a modular approach means less development time while still having the ability to integrate machine functions. Systems are broken down into small units, with the awareness that these units will be common to different applications, yet brought together as needed for the final design. An example is the VL and VT modular, vertical pickup lathes for chucked components and shafts that EMAG introduced in 2013.
All products must evolve, and a modular design shortens the development and redesign cycle to that end. This is because a machine tool builder can reuse most of the old modules for its latest-generation machine and change only the ones that need improvement.
EMAG has not only made advancements to the original VL and VT machines, but has integrated additional machining processes, such as grinding, skiving, gear hobbing, induction hardening and laser welding. For parts manufacturers and machine tool builders alike, challenges remain when responding to requests for quotes faster, reducing delivery times and lowering costs, but the implementation of a modular machine strategy can aid these goals.
As the market continues to demand increased performance despite decreasing budgets and an emphasis on a quick return on investment, the attractive price-performance ratio of modular machines will increase their market penetration. This shows that a simple concept can deliver the best solution. CTE
Related Glossary Terms
- grinding
grinding
Machining operation in which material is removed from the workpiece by a powered abrasive wheel, stone, belt, paste, sheet, compound, slurry, etc. Takes various forms: surface grinding (creates flat and/or squared surfaces); cylindrical grinding (for external cylindrical and tapered shapes, fillets, undercuts, etc.); centerless grinding; chamfering; thread and form grinding; tool and cutter grinding; offhand grinding; lapping and polishing (grinding with extremely fine grits to create ultrasmooth surfaces); honing; and disc grinding.
- hardening
hardening
Process of increasing the surface hardness of a part. It is accomplished by heating a piece of steel to a temperature within or above its critical range and then cooling (or quenching) it rapidly. In any heat-treatment operation, the rate of heating is important. Heat flows from the exterior to the interior of steel at a definite rate. If the steel is heated too quickly, the outside becomes hotter than the inside and the desired uniform structure cannot be obtained. If a piece is irregular in shape, a slow heating rate is essential to prevent warping and cracking. The heavier the section, the longer the heating time must be to achieve uniform results. Even after the correct temperature has been reached, the piece should be held at the temperature for a sufficient period of time to permit its thickest section to attain a uniform temperature. See workhardening.
- induction hardening
induction hardening
Surface-hardening process in which only the surface layer of a suitable ferrous workpiece is heated by electromagnetic induction to above the upper critical temperature and immediately quenched.
- metalworking
metalworking
Any manufacturing process in which metal is processed or machined such that the workpiece is given a new shape. Broadly defined, the term includes processes such as design and layout, heat-treating, material handling and inspection.
- modular design ( modular construction)
modular design ( modular construction)
Manufacturing of a product in subassemblies that permits fast and simple replacement of defective assemblies and tailoring of the product for different purposes. See interchangeable parts.