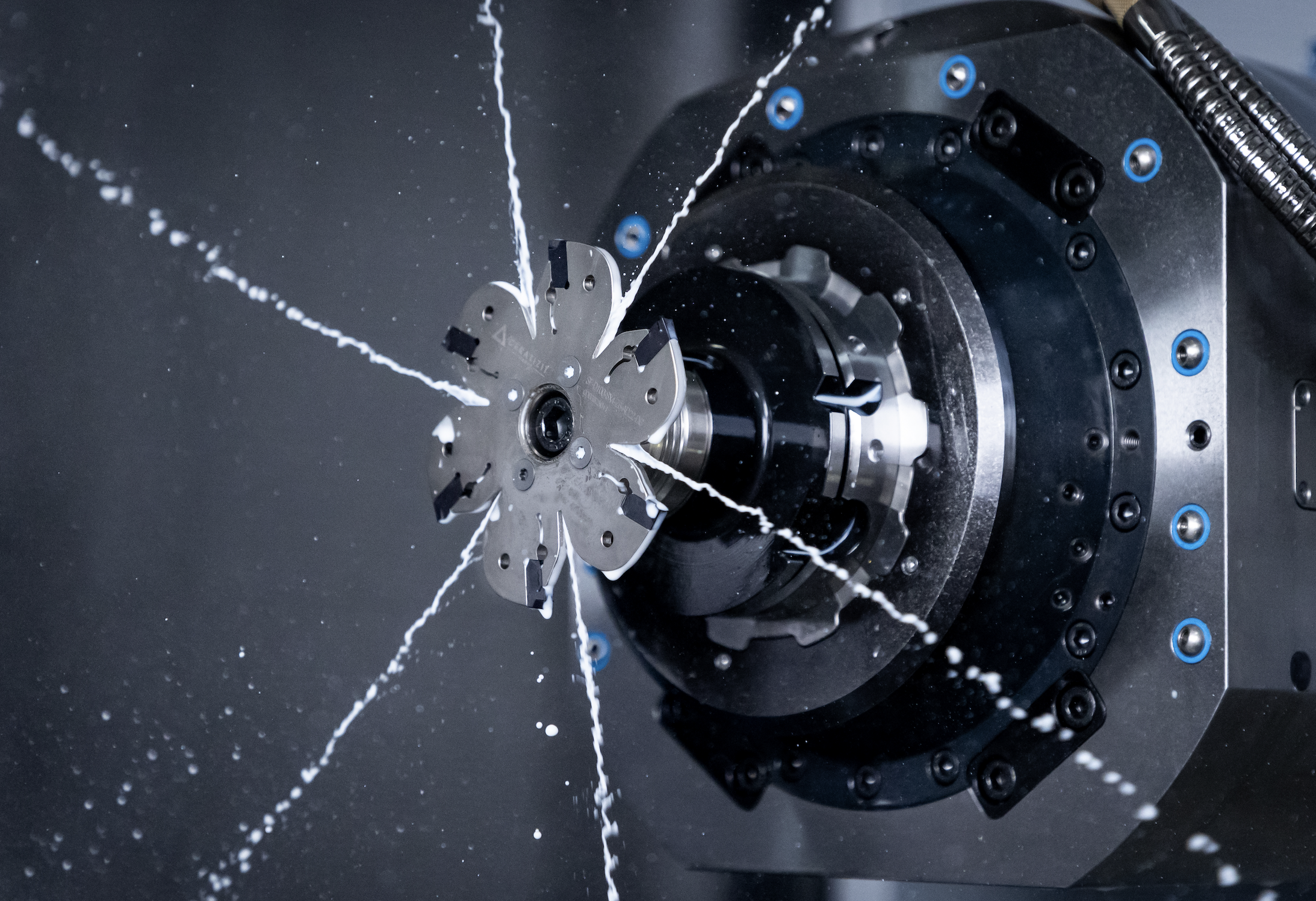
Job shops work hard to adapt and respond quickly to evolving customer needs, and shop readiness was top of mind when Ceratizit planned its lineup for Southtec from Oct. 24 to 26.
In booth #1509 at the Greenville, South Carolina, show, the company will feature innovative cutting tool solutions that prepare shops of all sizes to machine a broad spectrum of materials and improve sustainability.
“We listen to our customers,” said Dan Cope, executive vice president of cutting tools, Ceratizit USA. “Shops of all sizes are faced with machining a variety of materials or new materials to stay competitive, and we are meeting the challenge with them.”
For turning, Ceratizit will highlight indexable inserts and the KOMtronic U-axis system. With common steel turning operations in mind, Ceratizit’s standard coated-carbide ISO-P steel insert grades are highly engineered for increased productivity and feature advanced substrates and geometries.
From Ceratizit’s X7 Line of indexable inserts, the company’s CTPX710 and CRPX715 are designed specifically for difficult-to-machine materials. The X7 Line turning grades are next generation, high-performance substrates that offer outstanding performance when machining steel, stainless steel, superalloys and non-ferrous metals.
Both ISO-P and X7 Line inserts are reinforced with an AITin-based coating applied by the company’s proprietary Dragonskin coating technology. The microstructure of the coating has been optimized to resist heat, less tool wear and process security.
For non-rotationally symmetrical parts, Ceratizit’s freely programmable KOMtronic U-axis system makes any turning and contouring operation possible. When combined with custom-made front tools and the optimum selection of inserts, the system successfully performs contours in bores as well as external machining operations. Additionally, the system allows shops to use standard machines.
Southtec guests seeking milling solutions can visit Ceratizit’s booth for insert grades to machine heat resistant superalloys (HRSA), slot milling cutters and solid carbide end mills. Ceratizit’s CTCS245 and CTC5240 inserts also include Dragonskin coating technology and were specifically developed for milling applications of nickel-based and titanium-based alloys respectfully. The inserts crossover to other HRSA materials as well, including Inconel.
The MaxMill Slot-SX is a milling cutter system that closes the gap of milling tools with indexable inserts to machine steel, stainless steel, cast iron, non-ferrous and HRSA. Internal coolant holes ensure optimum chip control.
Ceratizit’s P007 and P556 solid carbide end mills are protected with the Dragonskin coating and built for roughing and finishing for a wide range of applications. The tools provide a high value-to-performance ratio, an H6 shank tolerance, unequal index and variable helix. Additionally, the four flute P007 and five flute P556 designs will set the stage for new products Ceratizit has planned in 2024.
“It is our responsibility on behalf of our customers to look to the future,” said Cope. “We will bring that forward thinking to the show in October.”
Contact Details
Related Glossary Terms
- alloys
alloys
Substances having metallic properties and being composed of two or more chemical elements of which at least one is a metal.
- coolant
coolant
Fluid that reduces temperature buildup at the tool/workpiece interface during machining. Normally takes the form of a liquid such as soluble or chemical mixtures (semisynthetic, synthetic) but can be pressurized air or other gas. Because of water’s ability to absorb great quantities of heat, it is widely used as a coolant and vehicle for various cutting compounds, with the water-to-compound ratio varying with the machining task. See cutting fluid; semisynthetic cutting fluid; soluble-oil cutting fluid; synthetic cutting fluid.
- gang cutting ( milling)
gang cutting ( milling)
Machining with several cutters mounted on a single arbor, generally for simultaneous cutting.
- microstructure
microstructure
Structure of a metal as revealed by microscopic examination of the etched surface of a polished specimen.
- milling
milling
Machining operation in which metal or other material is removed by applying power to a rotating cutter. In vertical milling, the cutting tool is mounted vertically on the spindle. In horizontal milling, the cutting tool is mounted horizontally, either directly on the spindle or on an arbor. Horizontal milling is further broken down into conventional milling, where the cutter rotates opposite the direction of feed, or “up” into the workpiece; and climb milling, where the cutter rotates in the direction of feed, or “down” into the workpiece. Milling operations include plane or surface milling, endmilling, facemilling, angle milling, form milling and profiling.
- milling cutter
milling cutter
Loosely, any milling tool. Horizontal cutters take the form of plain milling cutters, plain spiral-tooth cutters, helical cutters, side-milling cutters, staggered-tooth side-milling cutters, facemilling cutters, angular cutters, double-angle cutters, convex and concave form-milling cutters, straddle-sprocket cutters, spur-gear cutters, corner-rounding cutters and slitting saws. Vertical cutters use shank-mounted cutting tools, including endmills, T-slot cutters, Woodruff keyseat cutters and dovetail cutters; these may also be used on horizontal mills. See milling.
- shank
shank
Main body of a tool; the portion of a drill or similar end-held tool that fits into a collet, chuck or similar mounting device.
- superalloys
superalloys
Tough, difficult-to-machine alloys; includes Hastelloy, Inconel and Monel. Many are nickel-base metals.
- tolerance
tolerance
Minimum and maximum amount a workpiece dimension is allowed to vary from a set standard and still be acceptable.
- turning
turning
Workpiece is held in a chuck, mounted on a face plate or secured between centers and rotated while a cutting tool, normally a single-point tool, is fed into it along its periphery or across its end or face. Takes the form of straight turning (cutting along the periphery of the workpiece); taper turning (creating a taper); step turning (turning different-size diameters on the same work); chamfering (beveling an edge or shoulder); facing (cutting on an end); turning threads (usually external but can be internal); roughing (high-volume metal removal); and finishing (final light cuts). Performed on lathes, turning centers, chucking machines, automatic screw machines and similar machines.