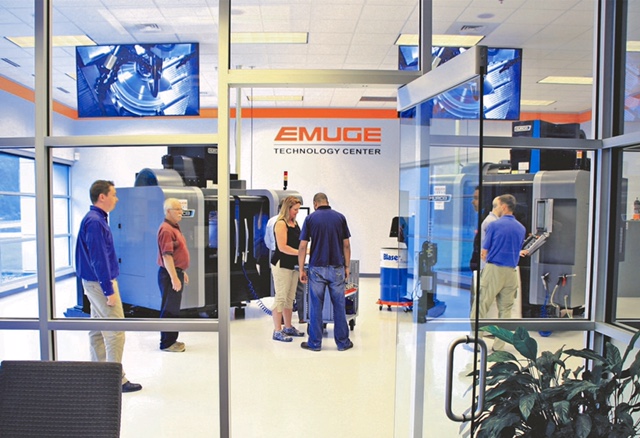
WEST BOYLSTON, Mass. – Emuge Corp. (www.emuge.com) announced on September 26th the opening of a new technology center, located at the company’s North American headquarters in West Boylston, MA, USA. The center, designed to be a full-service resource for manufacturers to apply cutting tool application strategies, is equipped with the latest 3 and 5-axis vertical machining centers, precision measuring devices and tool monitoring, in addition to an interactive classroom for training and seminars. The technology center will serve customers across the U.S. and Canada, enabling manufacturing professionals to test cut their applications and develop milling, drilling, and threading strategies to optimize tool life and performance and reduce cycle times.
“Our new Technology Center was conceived as a resource for manufacturers to test new machining concepts and tools without tying up their valuable machines and manufacturing time,” explained Bob Hellinger, President of Emuge Corp. “Our tooling engineers work directly with customers to replicate actual machining processes and develop new tooling and application parameters with complete documentation.”
Three major services offered at the Emuge Corp. Technology Center include Test Cuts, CNC Programming Assistance and Comprehensive Training:
For the Test Cuts Program, customers can provide Emuge sample parts and prints for evaluation by experienced Emuge tooling engineers. Once approved, test cuts are performed and documented, along with optimal recommended solutions and strategies developed by Emuge.
For CNC Programming Assistance, Emuge programmers work closely with industry leading CAD/CAM provides such as Mastercam, Open Mind and others, to help the user generate maximum machining performance and incorporate optimal tool designs. Emuge will provide customers programing assistance, a wide range of CAM tools for solving complex applications, efficient toolpaths, sub routines and optimization.
Emuge also provides Training and Development in an interactive classroom supported by CNC machining equipment for hands-on, real-time training. Training and seminars will be offered throughout the year on various topics, or custom training can be provided to meet the needs of individual companies.
Emuge has also recently introduced complete tool reconditioning services at the West Boylston, MA facility, which now also houses a state-of-the-art tool grinding/manufacturing center for refurbishing Emuge tools.
Related Glossary Terms
- centers
centers
Cone-shaped pins that support a workpiece by one or two ends during machining. The centers fit into holes drilled in the workpiece ends. Centers that turn with the workpiece are called “live” centers; those that do not are called “dead” centers.
- computer numerical control ( CNC)
computer numerical control ( CNC)
Microprocessor-based controller dedicated to a machine tool that permits the creation or modification of parts. Programmed numerical control activates the machine’s servos and spindle drives and controls the various machining operations. See DNC, direct numerical control; NC, numerical control.
- computer-aided manufacturing ( CAM)
computer-aided manufacturing ( CAM)
Use of computers to control machining and manufacturing processes.
- gang cutting ( milling)
gang cutting ( milling)
Machining with several cutters mounted on a single arbor, generally for simultaneous cutting.
- milling
milling
Machining operation in which metal or other material is removed by applying power to a rotating cutter. In vertical milling, the cutting tool is mounted vertically on the spindle. In horizontal milling, the cutting tool is mounted horizontally, either directly on the spindle or on an arbor. Horizontal milling is further broken down into conventional milling, where the cutter rotates opposite the direction of feed, or “up” into the workpiece; and climb milling, where the cutter rotates in the direction of feed, or “down” into the workpiece. Milling operations include plane or surface milling, endmilling, facemilling, angle milling, form milling and profiling.
- threading
threading
Process of both external (e.g., thread milling) and internal (e.g., tapping, thread milling) cutting, turning and rolling of threads into particular material. Standardized specifications are available to determine the desired results of the threading process. Numerous thread-series designations are written for specific applications. Threading often is performed on a lathe. Specifications such as thread height are critical in determining the strength of the threads. The material used is taken into consideration in determining the expected results of any particular application for that threaded piece. In external threading, a calculated depth is required as well as a particular angle to the cut. To perform internal threading, the exact diameter to bore the hole is critical before threading. The threads are distinguished from one another by the amount of tolerance and/or allowance that is specified. See turning.