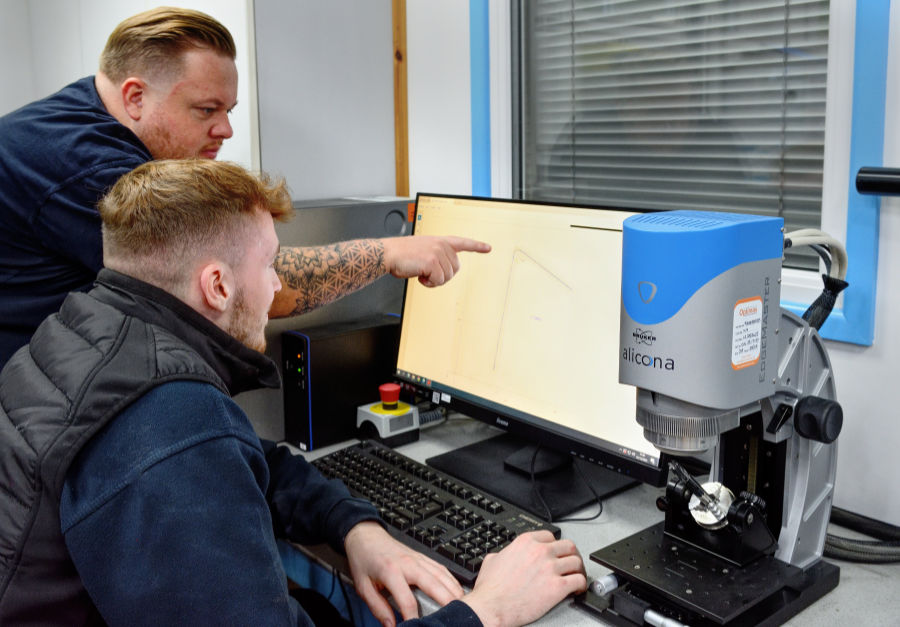
Surface finishing experts, Fintek, have in invested in a new Bruker Alicona EdgeMaster. The automatic metrology system for cutting tools is supplied and supported by Optimax Imaging Inspection & Measurement Ltd in the UK.
The efficiency and life of cutting tools are vastly improved by accurate edge preparation. Tool condition also directly affects the surface finish of a machined area and the need for additional post-processing to meet the required end product quality. Therefore, precise edge measurements are vital before and after surface finishing and edge rounding.
The high-resolution capabilities of the Alicona EdgeMaster confirm the precision of Fintek’s edge preparation services to cutting tool manufacturers and tool users. General manager, Jamie Phillips, explains, “Our previous system for measuring tool edges was straining to keep pace with high demand and current workflows. The EdgeMaster gives us faster measurement of cutting tool edges with increased accuracy. Having previously worked with Optimax, we know that the EdgeMaster comes with great support.”
“Cutting tool manufacturers go to great lengths to design and make their products effective for specific materials and workpieces. Drilling holes, for example, in composites, aluminum, steel, and hard or soft plastics all require cutting tools with different characteristics. With the EdgeMaster we can rapidly and accurately measure a tool before edge preparation. Using the data we then select the best combination of OTEC finishing machine, process media, and process parameters to achieve the target edge profile and finish. After post-processing, we quickly measure again to provide verification and traceability to customers. This is all documented in the Alicona software.” added Fintek production manager, Jason Hornby.
The EdgeMaster precisely measures edge radii >2µm as well as rake, wedge, and clearance angle for different types of tools, including waterfall and trumpet, inserts, milling cutters, and more. The accuracy of measurements is not affected by vibrations, temperature, or ambient light.
In addition to finishing services for tool manufacturers, Fintek reconditions worn tools – HSS, carbide, or coated – to the original manufacturer’s standard or even better. They are also a UK agent for OTEC Präzisionsfinish GmbH and distribute their comprehensive range of advanced surface finishing equipment to cutting tool makers throughout the UK.
Contact Details
Related Glossary Terms
- clearance
clearance
Space provided behind a tool’s land or relief to prevent rubbing and subsequent premature deterioration of the tool. See land; relief.
- composites
composites
Materials composed of different elements, with one element normally embedded in another, held together by a compatible binder.
- edge preparation
edge preparation
Conditioning of the cutting edge, such as a honing or chamfering, to make it stronger and less susceptible to chipping. A chamfer is a bevel on the tool’s cutting edge; the angle is measured from the cutting face downward and generally varies from 25° to 45°. Honing is the process of rounding or blunting the cutting edge with abrasives, either manually or mechanically.
- gang cutting ( milling)
gang cutting ( milling)
Machining with several cutters mounted on a single arbor, generally for simultaneous cutting.
- high-speed steels ( HSS)
high-speed steels ( HSS)
Available in two major types: tungsten high-speed steels (designated by letter T having tungsten as the principal alloying element) and molybdenum high-speed steels (designated by letter M having molybdenum as the principal alloying element). The type T high-speed steels containing cobalt have higher wear resistance and greater red (hot) hardness, withstanding cutting temperature up to 1,100º F (590º C). The type T steels are used to fabricate metalcutting tools (milling cutters, drills, reamers and taps), woodworking tools, various types of punches and dies, ball and roller bearings. The type M steels are used for cutting tools and various types of dies.
- metrology
metrology
Science of measurement; the principles on which precision machining, quality control and inspection are based. See precision machining, measurement.
- milling
milling
Machining operation in which metal or other material is removed by applying power to a rotating cutter. In vertical milling, the cutting tool is mounted vertically on the spindle. In horizontal milling, the cutting tool is mounted horizontally, either directly on the spindle or on an arbor. Horizontal milling is further broken down into conventional milling, where the cutter rotates opposite the direction of feed, or “up” into the workpiece; and climb milling, where the cutter rotates in the direction of feed, or “down” into the workpiece. Milling operations include plane or surface milling, endmilling, facemilling, angle milling, form milling and profiling.
- rake
rake
Angle of inclination between the face of the cutting tool and the workpiece. If the face of the tool lies in a plane through the axis of the workpiece, the tool is said to have a neutral, or zero, rake. If the inclination of the tool face makes the cutting edge more acute than when the rake angle is zero, the rake is positive. If the inclination of the tool face makes the cutting edge less acute or more blunt than when the rake angle is zero, the rake is negative.