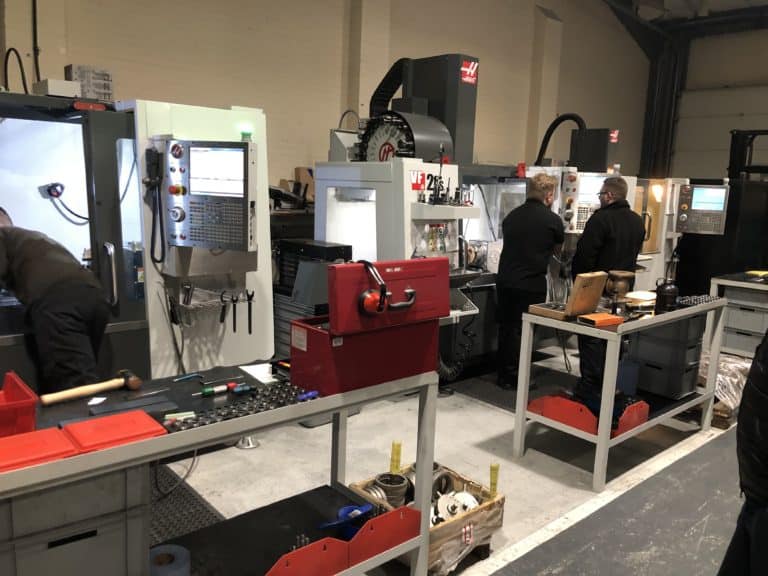
Article from Geomiq
Computer numerical control machining is an exercise where software controls how machinery moves as it produces an object. For example, when you want an automotive device from Geomiq.com, written codes are fed into the system whereby the machine runs as instructed. Consequently, your automotive item will be ready without the intervention of humans because the program runs independently.
Overview of the CNC Machining Procedure
CNC machining procedure starts by you or your CAD designer, creating 2D or 3D CAD design. The CAD/CAM software allows you to add dimension and geometry of the part you want to be manufactured. Other things to design with this software are the thickness, size and features.
The design is then run through CAM software to extract the geometry of the part. Consequently, the software will produce programming codes, which will be used to control how CNC machine to create your designed piece.
The other step is the setting up of the CNC machine after feeding it with programming codes. The process involves fixing the material from which your part will be produced, and other machine components.
Once the operators confirm that the machine is set up, they execute the program. Note that the program manipulates the machine on what direction to take and at what speed it manufactures the part designed.
Types of CNC Support Software
CNC machining uses software to achieve precision, accuracy and optimization. The first program is the CAD, which is used to design 2D vectors and 3D substantial parts. Other things you create using this software are the specification and properties.
The other software used in CNC machining is the CAM, which extracts program codes from CAD necessary for manipulating the production of a part. The program is responsible for aiding the CNC machine to function without human assistance.
Engineers also use computer-aided engineering software to support in designing, simulation, diagnosis and analysis. It helps engineers to identify a problem and repair it. The three are integrated into one program that manages the entire process of designing and manufacturing a part.
Choosing Material
Choosing a material from which a part will be cut depends on its specification and application. For instance, you can't use plastic bolts in a car engine: You need metal. Any material is suitable for machining but, metals, plastics, composites and wood are suitable for CNC machining. These materials must have the ability to withstand chemicals and high temperatures and have tensile and shear strength.
The material also determines how the program will be coded: the speed, depth of cut and cutting feeding degree. The CNC machine roughly prints the design on the material then takes deeper cuts to achieve precision and the strict requirement as per the codes fed onto it.
Size Deliberation
CNC machining applies to different industries, including automotive, electronics and aerospace. There are standard parts used across all three sectors. But the size and heaviness of each are different depending on the industry.
In other words, size consideration is an essential factor in CNC machining. How? It affects the setup of the machine, placing of specialized equipment, qualified and dedicated operator, among other factors. Manufacturing some parts might be more challenging than others. Nonetheless, CNC machining gets the job done.
CNC machining is a procedure for producing different parts for different industries like surgical equipment and automotive parts. There are three main ways of achieving how each of these parts looks.
CNC milling
This the process where the multiple-point cutting devices rotate in the same direction on the workpiece removing unwanted material from it. The process is used to achieve threads, shallows and flat surfaces.
CNC turning
The single point cutting device moves in a linear direction as it removes unwanted material from the workpiece. The tools move around the circumference of the workpiece until it achieves the internal and internal features of a part. The process completes threads, tapers and slots.
CNC drilling
Drill bits are employed on the workpiece to create cylindrical holes. A drill bit moves perpendicularly or angularly to a workpiece until the desired cylinder is achieved.
Other operations like honing, sawing and broaching are also used to achieve the specification drawn by the CAM software.
Take Away
Some things were impossible and impractical to design. However, since the introduction of CNC machining, these products can be manufactured accurately and precisely. Nonetheless, since this process depends on the codes written by an expert, you have to evaluate and choose the company with the best services. Check their success rate and rule whether the company is capable of handling your custom part.
Related Glossary Terms
- broaching
broaching
Operation in which a cutter progressively enlarges a slot or hole or shapes a workpiece exterior. Low teeth start the cut, intermediate teeth remove the majority of the material and high teeth finish the task. Broaching can be a one-step operation, as opposed to milling and slotting, which require repeated passes. Typically, however, broaching also involves multiple passes.
- composites
composites
Materials composed of different elements, with one element normally embedded in another, held together by a compatible binder.
- computer numerical control ( CNC)
computer numerical control ( CNC)
Microprocessor-based controller dedicated to a machine tool that permits the creation or modification of parts. Programmed numerical control activates the machine’s servos and spindle drives and controls the various machining operations. See DNC, direct numerical control; NC, numerical control.
- computer numerical control ( CNC)2
computer numerical control ( CNC)
Microprocessor-based controller dedicated to a machine tool that permits the creation or modification of parts. Programmed numerical control activates the machine’s servos and spindle drives and controls the various machining operations. See DNC, direct numerical control; NC, numerical control.
- computer-aided design ( CAD)
computer-aided design ( CAD)
Product-design functions performed with the help of computers and special software.
- computer-aided engineering ( CAE)
computer-aided engineering ( CAE)
Engineering functions performed with the help of computers and special software. Includes functions such as determining a material’s ability to withstand stresses.
- computer-aided manufacturing ( CAM)
computer-aided manufacturing ( CAM)
Use of computers to control machining and manufacturing processes.
- depth of cut
depth of cut
Distance between the bottom of the cut and the uncut surface of the workpiece, measured in a direction at right angles to the machined surface of the workpiece.
- flat ( screw flat)
flat ( screw flat)
Flat surface machined into the shank of a cutting tool for enhanced holding of the tool.
- gang cutting ( milling)
gang cutting ( milling)
Machining with several cutters mounted on a single arbor, generally for simultaneous cutting.
- milling
milling
Machining operation in which metal or other material is removed by applying power to a rotating cutter. In vertical milling, the cutting tool is mounted vertically on the spindle. In horizontal milling, the cutting tool is mounted horizontally, either directly on the spindle or on an arbor. Horizontal milling is further broken down into conventional milling, where the cutter rotates opposite the direction of feed, or “up” into the workpiece; and climb milling, where the cutter rotates in the direction of feed, or “down” into the workpiece. Milling operations include plane or surface milling, endmilling, facemilling, angle milling, form milling and profiling.
- numerical control ( NC)
numerical control ( NC)
Any controlled equipment that allows an operator to program its movement by entering a series of coded numbers and symbols. See CNC, computer numerical control; DNC, direct numerical control.
- sawing
sawing
Machining operation in which a powered machine, usually equipped with a blade having milled or ground teeth, is used to part material (cutoff) or give it a new shape (contour bandsawing, band machining). Four basic types of sawing operations are: hacksawing (power or manual operation in which the blade moves back and forth through the work, cutting on one of the strokes); cold or circular sawing (a rotating, circular, toothed blade parts the material much as a workshop table saw or radial-arm saw cuts wood); bandsawing (a flexible, toothed blade rides on wheels under tension and is guided through the work); and abrasive sawing (abrasive points attached to a fiber or metal backing part stock, could be considered a grinding operation).
- shear strength
shear strength
Stress required to produce fracture in the plane of cross section, the conditions of loading being such that the directions of force and of resistance are parallel and opposite although their paths are offset a specified minimum amount. The maximum load divided by the original cross-sectional area of a section separated by shear.
- turning
turning
Workpiece is held in a chuck, mounted on a face plate or secured between centers and rotated while a cutting tool, normally a single-point tool, is fed into it along its periphery or across its end or face. Takes the form of straight turning (cutting along the periphery of the workpiece); taper turning (creating a taper); step turning (turning different-size diameters on the same work); chamfering (beveling an edge or shoulder); facing (cutting on an end); turning threads (usually external but can be internal); roughing (high-volume metal removal); and finishing (final light cuts). Performed on lathes, turning centers, chucking machines, automatic screw machines and similar machines.