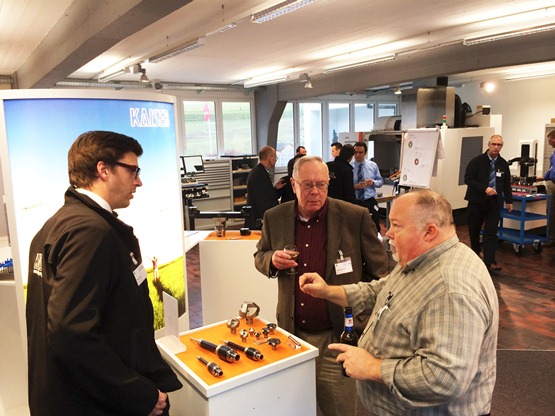
Tooling manufacturer BIG Kaiser Precision Tooling Inc., Hoffman Estates, Ill., hosted a group of U.S. manufacturers on a visit to the Kaiser Precision Tooling Ltd. headquarters in Rümlang, Switzerland, in February.
The third annual event paired educational presentations, tours of the assembly and machining areas and traditional Swiss hospitality.
"The challenges of manufacturing are universal," Dennis Rosene, owner, Rosene Machine, Firth, Neb., said. "Visiting factories outside the U.S. can help us find new ways to solve the same challenges we face at home."
Operations from product and fixture design to rough-and-finish machining and assembly are done on two levels of the original Kaiser factory. A flexible production process supports lot sizes from one to 1,000, but typical lots are 10 to 150 pieces.
A universal take-away for the American visitors was the Swiss model of efficiency. "In this part of our country, close to Zurich, the operating costs, cost of land, and demand for talent are all very high," Peter Elmer, CEO of Kaiser, explained. "We must always drive efficiency, quality and process optimization to be successful here."
"We were really impressed with how much production could be done in a relatively small space," Ronda Peterson, CEO, Peterson Machining, Boulder, Colo., said. "That gave us some ideas for our own shop."
The visitors were given a brief overview of the global organization. Many were surprised to learn that 25 percent of the BIG Kaiser products they use are actually licensed for manufacturing in Tennessee.
"Many of our tools are designed to the CAT specification common only in the U.S. With a portfolio of over 30,000 items, it's important we have domestic production and inventory for our customers," Jack Burley, vice president of BIG Kaiser explained. Meanwhile, products like digital boring heads, microtools, tool presetters and HSK shanks are produced at the facilities in Europe. In 2003, Kaiser entered into a global sales and marketing partnership with BIG Daishowa of Japan, thus changing the name of the U.S. operations to BIG Kaiser, and expanding the product line globally.
One highlight of the tour was new boring head technology. Released in 2012, this line of high-precision digital boring heads was designed and manufactured at the Swiss facility. A small sensor and digital display are built into each tool body, allowing quick and precise adjustment of the tool carrier. The patented design saves time and enables critical boring adjustments down to 0.00005", according to the company.
Related Glossary Terms
- boring
boring
Enlarging a hole that already has been drilled or cored. Generally, it is an operation of truing the previously drilled hole with a single-point, lathe-type tool. Boring is essentially internal turning, in that usually a single-point cutting tool forms the internal shape. Some tools are available with two cutting edges to balance cutting forces.
- boring head
boring head
Single- or multiple-point precision tool used to bring an existing hole within dimensional tolerance. The head attaches to a standard toolholder and a mechanism permits fine adjustments to be made to the head within a diameter range.
- fixture
fixture
Device, often made in-house, that holds a specific workpiece. See jig; modular fixturing.
- land
land
Part of the tool body that remains after the flutes are cut.