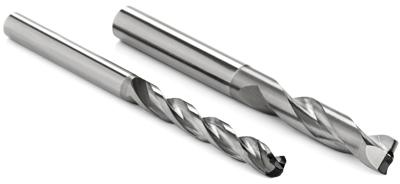
Seco Tools introduced the company's new CX1 and CX2 polycrystalline diamond (PCD) drills for composite holemaking. The new diamond-tip technology reportedly eliminates issues with uncut fibers or delamination in composite machining, and has allowed the company to successfully develop the industry's first PCD three-flute geometry (CX1) for composite drilling. Designed to offer the sharpest and strongest cutting edges currently available, the CX1 and CX2 PCD drills use solid PCD tips. These tips can be much sharper than PCD coated drills as the coating, when applied, wraps around the cutting edge and creates a dulling effect. Additional benefits of the new solid PCD tipped drills include high cutting speeds, long tool life, low friction, superior thermal conductivity, multiple resharpening capacity and high process reliability.
"In composite machining, acute edge sharpness is everything as the very thin fibers that comprise composite material are extremely difficult to cut," said Scott Turner, Marketing Manager-Holemaking at Seco. "If left uncut, these fibers eventually lead to material fray and premature part replacement. Furthermore, a sharper cutting tool requires less stress on the material and with less stress comes a lower chance of toughness compromising delamination."
For effectively drilling through "plain" composite materials, the third flute on the CX1 provides high levels of stability in the hole as well as decreases vibrations and improves roundness. Also, the dome-shaped tip of the CX1 applies a double-angle geometry that reduces uncut fibers and delamination in composite-only applications. Grinding these highly complex types of geometries was previously impossible using conventional brazed or similar PCD techniques.
Seco developed the CX2's flat geometry drill point for the machining of stacked composite materials that incorporate layers of aluminum, titanium or stainless steel. With a PCD cap and drill point angle of 180-degrees, the CX2 provides efficient chip breaking and evacuation. This reduces the chance of metal chips damaging the hole when transitioning between layers of metal and composites and, as a result, keeps the surface finish of the composite intact.
"While solid PCD-tipped drills are more expensive than PCD-coated drills," continued Turner, "the investing makes sense when hole quality is of the utmost importance, as with aircraft components. Also, the overall return on investment for these solid-tip designs can be substantial in certain applications such as the drilling of a large number of holes. In fact, the PCD drills with the CX1 and CX2 geometries have the ability to effectively drill two to three times more holes than a PCD-coated drill."
Both the CX1 and CX2 series include a mix of dimensions for holes that range in size from 0.125" to 0.375". Chamfers can also be incorporated into the drill designs to further increase application flexibility.
Contact Details
Related Glossary Terms
- composites
composites
Materials composed of different elements, with one element normally embedded in another, held together by a compatible binder.
- flat ( screw flat)
flat ( screw flat)
Flat surface machined into the shank of a cutting tool for enhanced holding of the tool.
- grinding
grinding
Machining operation in which material is removed from the workpiece by a powered abrasive wheel, stone, belt, paste, sheet, compound, slurry, etc. Takes various forms: surface grinding (creates flat and/or squared surfaces); cylindrical grinding (for external cylindrical and tapered shapes, fillets, undercuts, etc.); centerless grinding; chamfering; thread and form grinding; tool and cutter grinding; offhand grinding; lapping and polishing (grinding with extremely fine grits to create ultrasmooth surfaces); honing; and disc grinding.
- point angle
point angle
Included angle at the point of a twist drill or similar tool; for general-purpose tools, the point angle is typically 118°.
- polycrystalline diamond ( PCD)
polycrystalline diamond ( PCD)
Cutting tool material consisting of natural or synthetic diamond crystals bonded together under high pressure at elevated temperatures. PCD is available as a tip brazed to a carbide insert carrier. Used for machining nonferrous alloys and nonmetallic materials at high cutting speeds.
- polycrystalline diamond ( PCD)2
polycrystalline diamond ( PCD)
Cutting tool material consisting of natural or synthetic diamond crystals bonded together under high pressure at elevated temperatures. PCD is available as a tip brazed to a carbide insert carrier. Used for machining nonferrous alloys and nonmetallic materials at high cutting speeds.