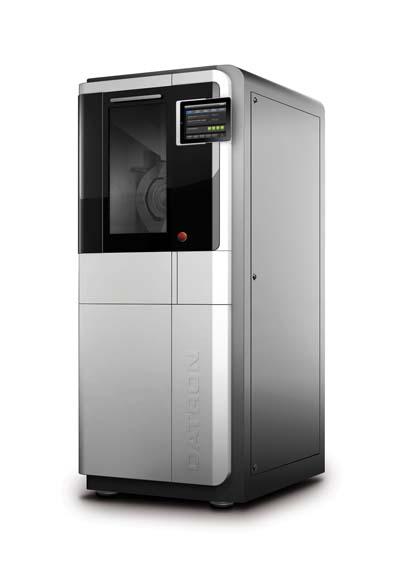
Datron Dynamics Inc. has announced the release of the DATRON D5 Dental Mill. This 5-axis, high-speed machining center was designed specifically and exclusively for dental milling applications including crowns, bridges, abutments, inlays, onlays, telescopes, implants, bar work and even models. A rigid cast iron construction houses a fully-integrated 5-axis automation system built to hold up to 8 material blanks or "pucks" frequently used by dental labs. This integrated 8-piece handling system loads and unloads blanks for un-attended operation. Finished blanks can be unloaded from the machine while the machine is running.
The DATRON D5 is optimized for the efficient machining of common dental materials such as NEM, titanium, chrome-cobalt, zirconium, PMMA, wax, ceramics and dental gypsum. This machine has 7 dynamic servo drives, cast construction, horizontally-mounted industrial spindle, all of which produce superior and ultra precise parts.
The D5 features a user-friendly touch-screen Apple iPad to control all machine functions. The control software is an open architecture capable of interfacing with all standard scanning systems and CAD/CAM packages. Even the size of the machine was dictated by the needs of dental laboratories and the D5 can fit through a standard 36" x 80" commercial door. The D5 has an integrated lubrication system and dust collection to handle any material being processed. Made in Germany, this machine was launched last month to critical acclaim – winning the prestigious Red Dot Design Award for Best Industrial Design. The D5's touch operator interface (Apple iPad) enables very simple programming of the DATRON Dental software. Since the Apple iPad is removable and can be taken off of the machining center, machine operations and job status can be monitored remotely even from a distance. For example, by activating the Live View button, the iPad screen shows the machining area.
A camera mounted inside the machine transmits the image to the removable iPad screen. This feature allows the operator to check the production status of the machine from another location, such as an office, or perhaps a ceramic station. Within the D5 machining software, the milling data generated by the CAM module is constantly synchronized with the job manager and activated when necessary. Simple Touch functions can link jobs together according to priority and deadline, or they can be run independently if preferred. Integrated blank management stores a library of data about the type and strength of the various materials comprising each individual blank (puck) housed within the automation unit. A plausibility examination is completed before any milling procedure begins. Tool data defining each tool type allows for the simple selection of tools by the CAM module.
Based on the function and machining time for which the tool will be employed, a pre-defined tool exchange (replacement) is scheduled – thereby ensuring ongoing quality control even during unattended operations. An integrated 13-station tool changer features tool-length and tool-break sensors. The milling tools and lubricant provided with the D5 which have been tested and optimized for superior tool life. The turning center of the rotary axis lies directly in the center of the material blank being milled which leads to tremendous rigidity – and contributes considerably to extremely high manufacturing accuracies.
Contact Details
Related Glossary Terms
- ceramics
ceramics
Cutting tool materials based on aluminum oxide and silicon nitride. Ceramic tools can withstand higher cutting speeds than cemented carbide tools when machining hardened steels, cast irons and high-temperature alloys.
- computer-aided manufacturing ( CAM)
computer-aided manufacturing ( CAM)
Use of computers to control machining and manufacturing processes.
- gang cutting ( milling)
gang cutting ( milling)
Machining with several cutters mounted on a single arbor, generally for simultaneous cutting.
- machining center
machining center
CNC machine tool capable of drilling, reaming, tapping, milling and boring. Normally comes with an automatic toolchanger. See automatic toolchanger.
- milling
milling
Machining operation in which metal or other material is removed by applying power to a rotating cutter. In vertical milling, the cutting tool is mounted vertically on the spindle. In horizontal milling, the cutting tool is mounted horizontally, either directly on the spindle or on an arbor. Horizontal milling is further broken down into conventional milling, where the cutter rotates opposite the direction of feed, or “up” into the workpiece; and climb milling, where the cutter rotates in the direction of feed, or “down” into the workpiece. Milling operations include plane or surface milling, endmilling, facemilling, angle milling, form milling and profiling.
- milling machine ( mill)
milling machine ( mill)
Runs endmills and arbor-mounted milling cutters. Features include a head with a spindle that drives the cutters; a column, knee and table that provide motion in the three Cartesian axes; and a base that supports the components and houses the cutting-fluid pump and reservoir. The work is mounted on the table and fed into the rotating cutter or endmill to accomplish the milling steps; vertical milling machines also feed endmills into the work by means of a spindle-mounted quill. Models range from small manual machines to big bed-type and duplex mills. All take one of three basic forms: vertical, horizontal or convertible horizontal/vertical. Vertical machines may be knee-type (the table is mounted on a knee that can be elevated) or bed-type (the table is securely supported and only moves horizontally). In general, horizontal machines are bigger and more powerful, while vertical machines are lighter but more versatile and easier to set up and operate.
- quality assurance ( quality control)
quality assurance ( quality control)
Terms denoting a formal program for monitoring product quality. The denotations are the same, but QC typically connotes a more traditional postmachining inspection system, while QA implies a more comprehensive approach, with emphasis on “total quality,” broad quality principles, statistical process control and other statistical methods.
- turning
turning
Workpiece is held in a chuck, mounted on a face plate or secured between centers and rotated while a cutting tool, normally a single-point tool, is fed into it along its periphery or across its end or face. Takes the form of straight turning (cutting along the periphery of the workpiece); taper turning (creating a taper); step turning (turning different-size diameters on the same work); chamfering (beveling an edge or shoulder); facing (cutting on an end); turning threads (usually external but can be internal); roughing (high-volume metal removal); and finishing (final light cuts). Performed on lathes, turning centers, chucking machines, automatic screw machines and similar machines.