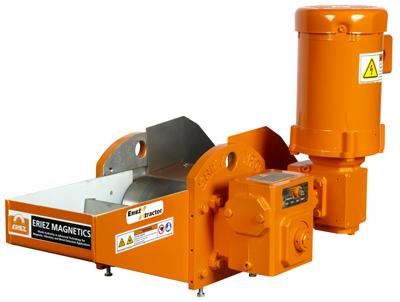
Eriez HydroFlow permanent magnetic and rare earth coolant cleaners are for use with surface grinders, gear grinders, honing and lapping machines, broaches, milling and drilling machines, face grinders, oil reclaiming machines and essentially anywhere else clean coolant is needed. They effectively maximize life of cutting tools, grinding wheels, pumps and coolant fluids.
"The demand for higher production rates and closer tolerances at lower costs has never been greater," says Dan Zimmerman, Eriez Director of Business Development. "We designed our line of Coolant Cleaners to meet the industry's precise requirements and expectations."
Coolant cleaners from Eriez HydroFlow keep machine tools running longer and more accurately with lower costs per unit produced. Radial-design magnetic circuits extract ferrous particles to help meet tolerances and improve surface finish in grinding and metalcutting operations.
Eriez offers both Permanent Magnetic and Rare Earth Coolant Cleaners in various models and capacities to meet practically any application need. Eriez says its knowledgeable and professional sales team is always available to guide customers through the equipment selection process. Eriez HydroFlow Coolant Cleaners are easy to install in restricted spaces and can be used on new or existing machines.
Contact Details
Related Glossary Terms
- coolant
coolant
Fluid that reduces temperature buildup at the tool/workpiece interface during machining. Normally takes the form of a liquid such as soluble or chemical mixtures (semisynthetic, synthetic) but can be pressurized air or other gas. Because of water’s ability to absorb great quantities of heat, it is widely used as a coolant and vehicle for various cutting compounds, with the water-to-compound ratio varying with the machining task. See cutting fluid; semisynthetic cutting fluid; soluble-oil cutting fluid; synthetic cutting fluid.
- gang cutting ( milling)
gang cutting ( milling)
Machining with several cutters mounted on a single arbor, generally for simultaneous cutting.
- grinding
grinding
Machining operation in which material is removed from the workpiece by a powered abrasive wheel, stone, belt, paste, sheet, compound, slurry, etc. Takes various forms: surface grinding (creates flat and/or squared surfaces); cylindrical grinding (for external cylindrical and tapered shapes, fillets, undercuts, etc.); centerless grinding; chamfering; thread and form grinding; tool and cutter grinding; offhand grinding; lapping and polishing (grinding with extremely fine grits to create ultrasmooth surfaces); honing; and disc grinding.
- lapping
lapping
Finishing operation in which a loose, fine-grain abrasive in a liquid medium abrades material. Extremely accurate process that corrects minor shape imperfections, refines surface finishes and produces a close fit between mating surfaces.
- metalcutting ( material cutting)
metalcutting ( material cutting)
Any machining process used to part metal or other material or give a workpiece a new configuration. Conventionally applies to machining operations in which a cutting tool mechanically removes material in the form of chips; applies to any process in which metal or material is removed to create new shapes. See metalforming.
- milling
milling
Machining operation in which metal or other material is removed by applying power to a rotating cutter. In vertical milling, the cutting tool is mounted vertically on the spindle. In horizontal milling, the cutting tool is mounted horizontally, either directly on the spindle or on an arbor. Horizontal milling is further broken down into conventional milling, where the cutter rotates opposite the direction of feed, or “up” into the workpiece; and climb milling, where the cutter rotates in the direction of feed, or “down” into the workpiece. Milling operations include plane or surface milling, endmilling, facemilling, angle milling, form milling and profiling.