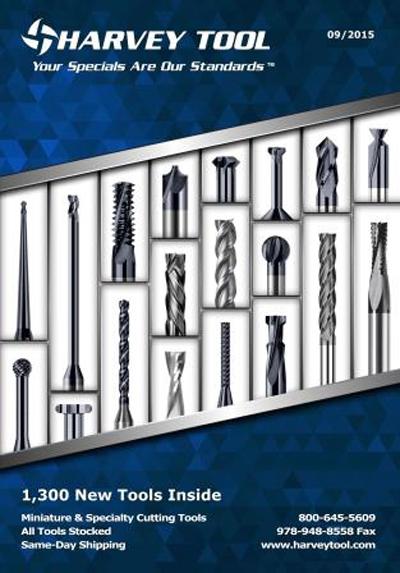
Harvey Tool has released its fall 2015 catalog. More than 1,300 new tools were added, with nine new product innovations, including Reamers, Diamond Cut End Mills, Variable Helix End Mills, Engravers, Double Angle Shank Cutters, Dovetail Cutters, and Hard Milling End Mills. Harvey Tool's Product Development Team has engineered these nine new Miniature and Specialty End Mill lines to grow our product offering to over 13,500 standard tools in stock.
The company now offers Mill Style and Drill Style Diamond Cut Composite Cutting End Mills. These end mills are ideally suited for composites with high fiber content such as carbon and glass fiber composites. The diamond cut style and high flute count allow for effective roughing and semi-roughing in abrasive composites. Both the End Mill Style and the Drill Style have downcut geometry on the OD, with the Drill Style having a 140° point for efficient plunging through composite sheet material. Both styles are offered in fractional sizes between 1⁄16" and ¼".
Harvey Tool's line of Hard Milling End Mills for Steels has been expanded to include end mills designed for milling from stock. In addition to having an h6 shank for shrink fit tool holders, these end mills are offered in a 5-flute variable helix design for improved slotting and roughing. Offered in both square and corner radius profiles, these highly useful end mills are designed to mill hardened tool, die and mold steels up to 55Rc and have our latest generation AlTiN Nano coating for superior hardness and heat resistance.
Harvey Tool announces the expansion of our Tip Radius Double Angle Shank Cutter line. Offered in our most popular angles and sizes, these cutters have a radius on the tip for improved strength and wear resistance. These versatile cutters are ideal for back chamfering, chamfering, deburring and milling a "V-groove." They also have a reduced neck for long reach machining and are offered uncoated or AlTiN coated for improved tool life and lubricity in ferrous materials.
Harvey Tool now offers our Pointed Engraver tool in a double ended version giving you two tools on one shank. These tools feature 180° opposing split lengths for improved balance at high RPMs. They are stocked in common angles and diameters that offer a great option to help decrease tooling costs without compromising quality or performance.
Harvey Tool now offers square Variable Helix Long Reach Stub Flute End Mills optimized for machining medium alloy steels. It's now possible to machine sharp corners in deep cavities with a rigid tool that combats deflection and also features the added benefits of variable geometry to enable higher feed rates, improve part finish, and increase tool life. These tools are offered with various reach options up to 10x the cutter diameter, and are AlTiN coated for improved lubricity and heat resistance when cutting medium alloy steels.
Long Reach Dovetail Cutters are here! Including all the benefits of our standard Dovetail Cutters, these tools feature a reduced neck for long reach machining and a corner radius for improved strength. These cutters are available in three included angles, 30°, 60°, and 90°, and cutter diameters ranging from 1⁄8" to ½". This product is offered uncoated for nonferrous applications and AlTiN coated for improved tool life and lubricity in ferrous materials.
With Harvey Tool's new line of Miniature Reamers machine shops can now finish tight tolerance through and blind holes to high precision. We offer 248 diameter options from .0080" up to .1890" with all tools ground to a tight diameter tolerance of +.0002"/-.0000" so you can be confident all holes are sized accurately to print specifications. These tools are AlTiN coated for improved lubricity and heat resistance in ferrous materials and are reached to 12x diameter for use in a wider range of hole depths.
"This catalog is a testament to Harvey Tool's commitment to thinking of our customers first by offering broader and deeper selection of stocked specialty tools," said Jeff Davis, Vice President of Product Development.
Contact Details
Related Glossary Terms
- abrasive
abrasive
Substance used for grinding, honing, lapping, superfinishing and polishing. Examples include garnet, emery, corundum, silicon carbide, cubic boron nitride and diamond in various grit sizes.
- alloy steels
alloy steels
Steel containing specified quantities of alloying elements (other than carbon and the commonly accepted amounts of manganese, sulfur and phosphorus) added to cause changes in the metal’s mechanical and/or physical properties. Principal alloying elements are nickel, chromium, molybdenum and silicon. Some grades of alloy steels contain one or more of these elements: vanadium, boron, lead and copper.
- chamfering
chamfering
Machining a bevel on a workpiece or tool; improves a tool’s entrance into the cut.
- composites
composites
Materials composed of different elements, with one element normally embedded in another, held together by a compatible binder.
- feed
feed
Rate of change of position of the tool as a whole, relative to the workpiece while cutting.
- gang cutting ( milling)
gang cutting ( milling)
Machining with several cutters mounted on a single arbor, generally for simultaneous cutting.
- hardness
hardness
Hardness is a measure of the resistance of a material to surface indentation or abrasion. There is no absolute scale for hardness. In order to express hardness quantitatively, each type of test has its own scale, which defines hardness. Indentation hardness obtained through static methods is measured by Brinell, Rockwell, Vickers and Knoop tests. Hardness without indentation is measured by a dynamic method, known as the Scleroscope test.
- lubricity
lubricity
Measure of the relative efficiency with which a cutting fluid or lubricant reduces friction between surfaces.
- milling
milling
Machining operation in which metal or other material is removed by applying power to a rotating cutter. In vertical milling, the cutting tool is mounted vertically on the spindle. In horizontal milling, the cutting tool is mounted horizontally, either directly on the spindle or on an arbor. Horizontal milling is further broken down into conventional milling, where the cutter rotates opposite the direction of feed, or “up” into the workpiece; and climb milling, where the cutter rotates in the direction of feed, or “down” into the workpiece. Milling operations include plane or surface milling, endmilling, facemilling, angle milling, form milling and profiling.
- milling machine ( mill)
milling machine ( mill)
Runs endmills and arbor-mounted milling cutters. Features include a head with a spindle that drives the cutters; a column, knee and table that provide motion in the three Cartesian axes; and a base that supports the components and houses the cutting-fluid pump and reservoir. The work is mounted on the table and fed into the rotating cutter or endmill to accomplish the milling steps; vertical milling machines also feed endmills into the work by means of a spindle-mounted quill. Models range from small manual machines to big bed-type and duplex mills. All take one of three basic forms: vertical, horizontal or convertible horizontal/vertical. Vertical machines may be knee-type (the table is mounted on a knee that can be elevated) or bed-type (the table is securely supported and only moves horizontally). In general, horizontal machines are bigger and more powerful, while vertical machines are lighter but more versatile and easier to set up and operate.
- outer diameter ( OD)
outer diameter ( OD)
Dimension that defines the exterior diameter of a cylindrical or round part. See ID, inner diameter.
- shank
shank
Main body of a tool; the portion of a drill or similar end-held tool that fits into a collet, chuck or similar mounting device.
- slotting
slotting
Machining, normally milling, that creates slots, grooves and similar recesses in workpieces, including T-slots and dovetails.
- tolerance
tolerance
Minimum and maximum amount a workpiece dimension is allowed to vary from a set standard and still be acceptable.
- wear resistance
wear resistance
Ability of the tool to withstand stresses that cause it to wear during cutting; an attribute linked to alloy composition, base material, thermal conditions, type of tooling and operation and other variables.