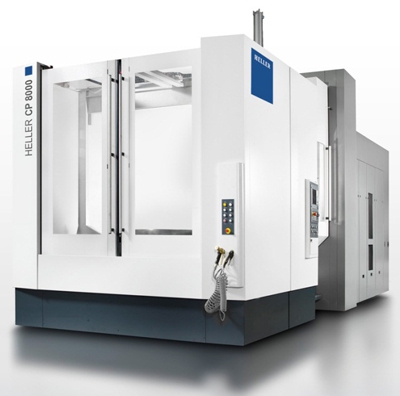
Shrinking batch sizes with larger varieties of parts and rising competitive pressure are increasingly leading to the demand for complete 5-axis machining, milling as well as turning, in a single set-up. To meet these demands HELLER Machine Tools introduced the CP 8000 5-axis milling and turning center.
The CP 8000 handles larger workpieces, offering a work area of 1,250mm x 1,200mm x 1,400mm (X, Y, Z), for pallet sizes of 800mm x 800mm. This enables milling of workpieces with a maximum loading capacity of 2,000 kg, a diameter of up to 1,250mm and a maximum height of 1,400mm in one set-up.
According to a HELLER spokesman, The CP 8000 is particularly productive and economical in machining predominantly cubic parts, with a particularly strong emphasis on process reliability or when the rotationally symmetric length/diameter ratio of the components is less than 1".
The fifth axis integrated into the tool indicates the significance HELLER engineers attached to accomplishing turning operations. Whether horizontal or vertical, external and internal turning contours can be produced extremely efficiently with the C or A and B axis.
The direct torque drive system in the rotary table delivers the power needed when the workpiece rotates against the tool.
A highlight of the CP 8000 is its ability to identify imbalances in the workpiece or the rotary table. Using drive-internal signals without the need for additional sensors, it identifies the smallest imbalance in the workpiece and corrects it. This is important for central clamping with repeat accuracy, but is also relevant for safety and productivity reasons.
Contact Details
Related Glossary Terms
- gang cutting ( milling)
gang cutting ( milling)
Machining with several cutters mounted on a single arbor, generally for simultaneous cutting.
- milling
milling
Machining operation in which metal or other material is removed by applying power to a rotating cutter. In vertical milling, the cutting tool is mounted vertically on the spindle. In horizontal milling, the cutting tool is mounted horizontally, either directly on the spindle or on an arbor. Horizontal milling is further broken down into conventional milling, where the cutter rotates opposite the direction of feed, or “up” into the workpiece; and climb milling, where the cutter rotates in the direction of feed, or “down” into the workpiece. Milling operations include plane or surface milling, endmilling, facemilling, angle milling, form milling and profiling.
- turning
turning
Workpiece is held in a chuck, mounted on a face plate or secured between centers and rotated while a cutting tool, normally a single-point tool, is fed into it along its periphery or across its end or face. Takes the form of straight turning (cutting along the periphery of the workpiece); taper turning (creating a taper); step turning (turning different-size diameters on the same work); chamfering (beveling an edge or shoulder); facing (cutting on an end); turning threads (usually external but can be internal); roughing (high-volume metal removal); and finishing (final light cuts). Performed on lathes, turning centers, chucking machines, automatic screw machines and similar machines.