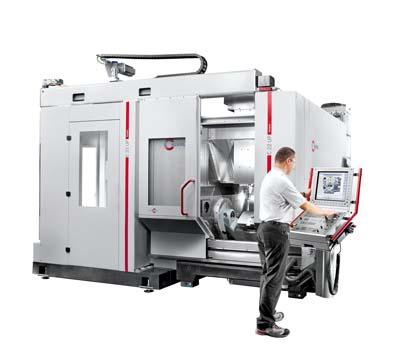
The CNC C 22 U dynamic high-speed machining center, first introduced by Hermle in 2010, can now also be fully automated. The pallet changer PW 150 was specially designed for workpiece dimensions of the C 22 and can transport weights up to 250 kg including pallet.
The automated system consists of an NC controlled drive unit and a turning unit with double gripper. Both units are positioned compactly on the left next to the machine and allow completely free access to the working area. The pallet changer does not have to be dismantled for transportation, it does not require a floor mounting, and it is adapted quickly and easily to the machine at the customer's facility.
The key feature of the pallet changer is the double gripper that can be used to simultaneously move two pallets with 150 kg transport weight each in or out or, for a one-sided application, one pallet with up to 250 kg transport weight. The maximum workpiece cube has a diameter of 400mm with a maximum workpiece height of 370mm.
The standard design can handle up to 6 pallets, with additional storage of up to 11 pallets. The side setup station (optional rotation) offers ideal conditions for setup concurrent with production time.
The spindle moves to the park position into the tool magazine. The top and the expansion bellows of the left side wall are opened together and provide access to the drive unit/turning unit with adapted double gripper. The double gripper docks with a pallet and moves it through the side access of the machining center and into the working area. The free side of the double gripper docks with and lifts the finished part pallet on the NC swivelling rotary table. Rotating through 180 degrees, both pallets are positioned and the blank pallet is placed on the table. The drive unit/turning unit conveys the finished part pallet into the storage or setup station.
In another optional version, several machining centers can also be interlinked and combined into an automated manufacturing center with an extended pallet changer.
Hermle Machine Company president, Robert Komljenovic commented, "The new pallet changer/double gripper design, which was engineered to match the size envelope of the C 22 U, offers our customers an automation solution applicable to one machine or to a multi-machine manufacturing center. The increasing demand from industries including aerospace, medical appliances and tools, and the energy sector for complex parts that fit the C 22 U's work area can now be met through an automated system built to Hermle's exacting standards. The C 22 U has become an extremely popular configuration in the North American market, and an easily accessible automated system can only make it more so."
Contact Details
Related Glossary Terms
- centers
centers
Cone-shaped pins that support a workpiece by one or two ends during machining. The centers fit into holes drilled in the workpiece ends. Centers that turn with the workpiece are called “live” centers; those that do not are called “dead” centers.
- computer numerical control ( CNC)
computer numerical control ( CNC)
Microprocessor-based controller dedicated to a machine tool that permits the creation or modification of parts. Programmed numerical control activates the machine’s servos and spindle drives and controls the various machining operations. See DNC, direct numerical control; NC, numerical control.
- machining center
machining center
CNC machine tool capable of drilling, reaming, tapping, milling and boring. Normally comes with an automatic toolchanger. See automatic toolchanger.
- numerical control ( NC)
numerical control ( NC)
Any controlled equipment that allows an operator to program its movement by entering a series of coded numbers and symbols. See CNC, computer numerical control; DNC, direct numerical control.
- turning
turning
Workpiece is held in a chuck, mounted on a face plate or secured between centers and rotated while a cutting tool, normally a single-point tool, is fed into it along its periphery or across its end or face. Takes the form of straight turning (cutting along the periphery of the workpiece); taper turning (creating a taper); step turning (turning different-size diameters on the same work); chamfering (beveling an edge or shoulder); facing (cutting on an end); turning threads (usually external but can be internal); roughing (high-volume metal removal); and finishing (final light cuts). Performed on lathes, turning centers, chucking machines, automatic screw machines and similar machines.