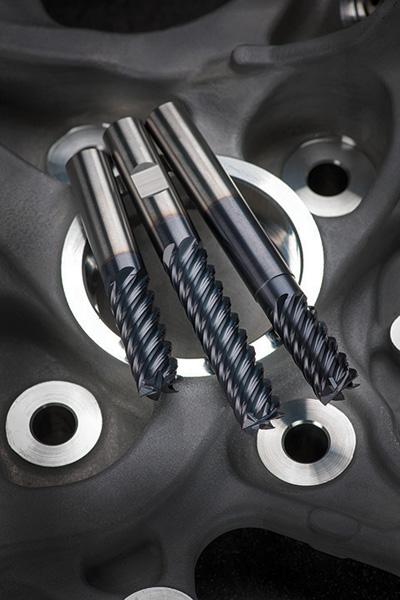
IMCO Carbide Tool offers the new wave of Omega M7 end mills.
"Omega M726 and M725 end mills are specially designed to overcome the unique challenges of machining in hardened steels, even up to 58-62 HRC, running wet or dry," said IMCO President Perry Osburn. "We've produced significant increases in tool life and corresponding savings in tool costs by applying our advanced understanding of cutting technology to make sure our end mills are the best they can possibly be."
That process resulted in changes to corner geometries, a 50 degree helix angle, improved cutting edges and a more advanced AlTiNX coating to protect those cutting edges from heat generated in the cutting zone, even under extreme cutting conditions.
Six flutes provide more cutting edge engagement per rotation for more inches per minutes in hardened steels, and extra strength for remarkably longer tool life. Running dry requires use of modern high-speed, high-efficiency machining techniques and continuous toolpaths.
Tested in IMCO's machining lab A2 steel at HRC 60 using ¼" dia. end mill at 0.25" axial DOC and 0.015" radial DOC, the Omega M726 end mill lasted more than 3 times longer than comparable competitors' tools and even the original M706. In addition, the M726 end mill provides reliably superior finishes in a wide range of non-hardened materials.
The new Omega M7 line is available in sizes from 1⁄8" to ¾" and in a variety of lengths with neck relief and corner radii as standard options. Sizes 1⁄8" to 3/16" have five flutes for maximum chip evacuation and are designated the M725 series. All other geometries on M725 end mills are the same as those on M726 end mills.
Contact Details
Related Glossary Terms
- flutes
flutes
Grooves and spaces in the body of a tool that permit chip removal from, and cutting-fluid application to, the point of cut.
- helix angle
helix angle
Angle that the tool’s leading edge makes with the plane of its centerline.
- milling machine ( mill)
milling machine ( mill)
Runs endmills and arbor-mounted milling cutters. Features include a head with a spindle that drives the cutters; a column, knee and table that provide motion in the three Cartesian axes; and a base that supports the components and houses the cutting-fluid pump and reservoir. The work is mounted on the table and fed into the rotating cutter or endmill to accomplish the milling steps; vertical milling machines also feed endmills into the work by means of a spindle-mounted quill. Models range from small manual machines to big bed-type and duplex mills. All take one of three basic forms: vertical, horizontal or convertible horizontal/vertical. Vertical machines may be knee-type (the table is mounted on a knee that can be elevated) or bed-type (the table is securely supported and only moves horizontally). In general, horizontal machines are bigger and more powerful, while vertical machines are lighter but more versatile and easier to set up and operate.
- relief
relief
Space provided behind the cutting edges to prevent rubbing. Sometimes called primary relief. Secondary relief provides additional space behind primary relief. Relief on end teeth is axial relief; relief on side teeth is peripheral relief.