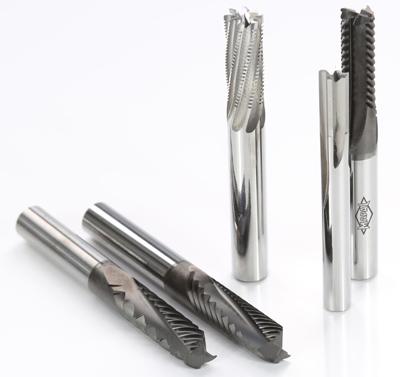
The trend towards lightweight construction is resulting in the constant development of new materials with a very wide range of properties which create new demands also on the machining. Tool manufacturers have to react here, as reliable machining is no longer assured with the normal geometries. MAPAL has now expanded its extensive milling cutter product range that has been well-established on the market for many years to include four new high-performance milling cutters.
Thermoplastics are widely used in the automotive sector, for example in the production of instrument panels. Due to its low melting temperature, the material requires special tool geometries to avoid melting. MAPAL has therefore developed the solid-carbide OptiMill-Thermoplastic with very sharp cutting edges for the reliable machining of thermoplastics. Its special geometry not only ensures the optimal discharge of the chips, but also minimizes the build-up of heat during milling. MAPAL also offers the OptiMill-Thermoplastic-FR for the machining of special fiber-reinforced thermoplastics, predominantly carbon fibers. As carbon fibers are very abrasive, the solid-carbide milling cutter is diamond coated. Thanks to the arrangement of the cutting edges around the circumference, the fibers are cut off cleanly without burr formation.
The solid-carbide end milling cutter, OptiMill-Composite-UD, was added to the milling cutter range for the milling of parts made from fiber composite materials such as CFRP that are either very thin or are difficult to machine. Thanks to its cutting edge geometry, it achieves a simultaneous pulling and pushing cut with compression effect in the part, thus preventing delaminations and fibre projections. The milling cutter is diamond coated for a long tool life.
Due to their low weight and flexural strength, honeycomb structures are used for support and reinforcement between the inner and outer skin of aircraft or in the vanes of wind energy converters. The difficulty when machining this very light material is its comb structure. MAPAL has developed the OptiMill-Honeycomb to meet the special demands of machining honeycombs. The eight-bladed solid-carbide end milling cutter has extremely sharp cutting edges, a helix angle of 15 degrees and very fine serration. The new OptiMill-Honeycomb reliably machines even honeycombs with a wide variety of outer layers or with fillings.
The new milling cutters, OptiMill-Thermoplastic, OptiMill-Thermoplastic-FR, OptiMill-Composite-UD and OptiMill-Honeycomb are immediately available in a range of dimensions.
Contact Details
Related Glossary Terms
- abrasive
abrasive
Substance used for grinding, honing, lapping, superfinishing and polishing. Examples include garnet, emery, corundum, silicon carbide, cubic boron nitride and diamond in various grit sizes.
- burr
burr
Stringy portions of material formed on workpiece edges during machining. Often sharp. Can be removed with hand files, abrasive wheels or belts, wire wheels, abrasive-fiber brushes, waterjet equipment or other methods.
- gang cutting ( milling)
gang cutting ( milling)
Machining with several cutters mounted on a single arbor, generally for simultaneous cutting.
- helix angle
helix angle
Angle that the tool’s leading edge makes with the plane of its centerline.
- milling
milling
Machining operation in which metal or other material is removed by applying power to a rotating cutter. In vertical milling, the cutting tool is mounted vertically on the spindle. In horizontal milling, the cutting tool is mounted horizontally, either directly on the spindle or on an arbor. Horizontal milling is further broken down into conventional milling, where the cutter rotates opposite the direction of feed, or “up” into the workpiece; and climb milling, where the cutter rotates in the direction of feed, or “down” into the workpiece. Milling operations include plane or surface milling, endmilling, facemilling, angle milling, form milling and profiling.
- milling cutter
milling cutter
Loosely, any milling tool. Horizontal cutters take the form of plain milling cutters, plain spiral-tooth cutters, helical cutters, side-milling cutters, staggered-tooth side-milling cutters, facemilling cutters, angular cutters, double-angle cutters, convex and concave form-milling cutters, straddle-sprocket cutters, spur-gear cutters, corner-rounding cutters and slitting saws. Vertical cutters use shank-mounted cutting tools, including endmills, T-slot cutters, Woodruff keyseat cutters and dovetail cutters; these may also be used on horizontal mills. See milling.