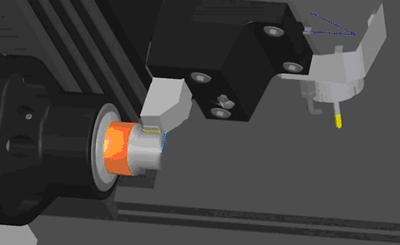
Methods Machine Tools Inc. is introducing Version 6.0 of CAMplete TurnMill software for Nakamura-Tome multitasking turning centers, which includes several upgrades for greater macro language support, improved error handling and increased post processing capabilities. CAMplete TurnMill software is an integrated suite of G-Code editing, optimization, analysis and verification tools, enabling a full range of turn/mill functions, and comes standard on the full line of Nakamura multitasking turning centers.
CAMplete TurnMill Version 6.0 offers added support for FANUC Macro B language including G# and M# calls; G65 macro calls; local, common, system and shared variables; variable math; IF/GOTO statements and sub program calls. Users now have the ability to create custom macros that can be easily inserted into any G-Code or formatted program.
Upgrades also include improved error handling, reporting and navigation, and an enhanced simulation progress display that now shows nested program calls. Newly designed regeneration controls have been added to show the active program and current location, including line number, within the program. Post processing support has been broadened in CAMplete TurnMill Version 6.0 to be compatible with Delcam's PowerMILL CAM software for milling from CUT files for 3+2 milling, 5-Axis milling and canned cycles; Mastercam CAD/CAM software support from NCI files; as well as OPEN MIND's hyperMILL post processing from POF files. Mastercam and HyperMill post processing works with ATC and WT-Series machines, turning, milling and 5-Axis milling.
"CAMplete TurnMill Version 6.0 features upgrades that will further enhance our Nakamura multitasking solution. Users now have a number of new functions which will result in greater productivity," said Richard Parenteau, Director of Applications Development at Methods Machine Tools.
Additional upgrades include stock creation for the main/sub-spindle and new material removal simulation. CAMplete TurnMill Version 6.0 offers full 64-bit support to accommodate larger programs and provide increased performance. The tool library has been redesigned and enhanced for greater ease-of-use and faster processing. CAMplete TurnMill software was originally developed to create a program that could combine G-Code from CAM systems and hand-coded G-Code into a set of programs that could be simulated, fine-tuned and optimized using detailed 3-D Nakamura machine models.
Contact Details
Related Glossary Terms
- 3-D
3-D
Way of displaying real-world objects in a natural way by showing depth, height and width. This system uses the X, Y and Z axes.
- centers
centers
Cone-shaped pins that support a workpiece by one or two ends during machining. The centers fit into holes drilled in the workpiece ends. Centers that turn with the workpiece are called “live” centers; those that do not are called “dead” centers.
- computer-aided manufacturing ( CAM)
computer-aided manufacturing ( CAM)
Use of computers to control machining and manufacturing processes.
- gang cutting ( milling)
gang cutting ( milling)
Machining with several cutters mounted on a single arbor, generally for simultaneous cutting.
- milling
milling
Machining operation in which metal or other material is removed by applying power to a rotating cutter. In vertical milling, the cutting tool is mounted vertically on the spindle. In horizontal milling, the cutting tool is mounted horizontally, either directly on the spindle or on an arbor. Horizontal milling is further broken down into conventional milling, where the cutter rotates opposite the direction of feed, or “up” into the workpiece; and climb milling, where the cutter rotates in the direction of feed, or “down” into the workpiece. Milling operations include plane or surface milling, endmilling, facemilling, angle milling, form milling and profiling.
- turning
turning
Workpiece is held in a chuck, mounted on a face plate or secured between centers and rotated while a cutting tool, normally a single-point tool, is fed into it along its periphery or across its end or face. Takes the form of straight turning (cutting along the periphery of the workpiece); taper turning (creating a taper); step turning (turning different-size diameters on the same work); chamfering (beveling an edge or shoulder); facing (cutting on an end); turning threads (usually external but can be internal); roughing (high-volume metal removal); and finishing (final light cuts). Performed on lathes, turning centers, chucking machines, automatic screw machines and similar machines.