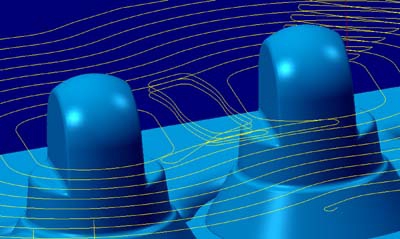
OPEN MIND Technologies AG has released its new optimization strategy for stock roughing titled hyperMAXX. The high-performance roughing module is powered by the Volumill toolpath layout engine from Celeritive Technologies (and is fully integrated in hyperMILL 2010. It combines optimal milling paths and maximum material removal with minimized machining times. With features like constant radial depth of cut and fully automated dynamic feedrate and infeed adjustment, the results are significantly improved productivity and cutting conditions.
The optional hyperMAXX module generates ideally distributed 3D milling paths for stock roughing, reducing wear and tear on both milling machine and cutting tools. This is achieved by establishing and maintaining ideal cutting conditions throughout, regardless of part shape. Milling parameters are set based on best-case scenarios, rather than the usual worst-case situations like cornering, entry moves, and connection paths. Feed rates are also adjusted dynamically in special machining conditions to ensure constant volume removal.
Roughing time savings of 50 percent or more are typical. As the new strategy is fully integrated in hyperMILL, there is no need to open any additional software tools, change the program, or adjust the post-processor, further boosting productivity while optimally complementing the other roughing strategies in hyperMILL. The Celeritive Volumill toolpath kernel has been successfully used in the market for years within standalone versions and other integrations. This is matched with proven hyperMILL analysis for slicing, stock management, collision detection, and more. Increasing service life and reducing milling times.
As hyperMAXX performs all machining jobs in a predictable, consistent manner, tools and machines are subjected to an even load, resulting in increased service life. Tool paths are completely free of abrupt changes of direction and other extreme tool movements, thus providing the basis for a high surface quality. hyperMAXX ensures maximum material removal and the fastest possible safe positioning of the tool, resulting in reduced machining times and more efficient production.
The high performance of hyperMAXX is made possible by intelligent automated functions, such as a feature that accounts for the material and dynamically optimizes both feedrate and infeed during 3D arbitrary stock roughing to control the volume of cut. This option is seamlessly integrated with hyperMILL's roughing procedure to simplify learning and implementation. There are also two selectable functions. The "first opening cut" is suited for full-cut machining of areas that are difficult to reach, and is highly effective in softer materials, such as aluminum. The "side cutting only" option enables opening via lateral infeed movements without full cutting, and is designed for machining harder materials.
The plunge macro always creates a complete helix or ramp movement and automatically determines the helix radius. Up to 100 per cent of the tool diameter can be processed by infeed without any rest material remaining between adjacent paths. For axial infeeds, the process is absolutely reliable up to the maximum cutting length. hyperMAXX is suited for machining soft as well as harder materials that are hard to chip, such as titanium, nickel-based alloys, or stainless steel. Both machining large parts and performing micro jobs can be handled quickly and efficiently using hyperMAXX. The function range also includes a collision check that accounts for tool lengths as well as plane detection in automatic mode. In addition, the residual geometry can be defined as a stock for subsequent job steps.
Related Glossary Terms
- alloys
alloys
Substances having metallic properties and being composed of two or more chemical elements of which at least one is a metal.
- depth of cut
depth of cut
Distance between the bottom of the cut and the uncut surface of the workpiece, measured in a direction at right angles to the machined surface of the workpiece.
- feed
feed
Rate of change of position of the tool as a whole, relative to the workpiece while cutting.
- gang cutting ( milling)
gang cutting ( milling)
Machining with several cutters mounted on a single arbor, generally for simultaneous cutting.
- milling
milling
Machining operation in which metal or other material is removed by applying power to a rotating cutter. In vertical milling, the cutting tool is mounted vertically on the spindle. In horizontal milling, the cutting tool is mounted horizontally, either directly on the spindle or on an arbor. Horizontal milling is further broken down into conventional milling, where the cutter rotates opposite the direction of feed, or “up” into the workpiece; and climb milling, where the cutter rotates in the direction of feed, or “down” into the workpiece. Milling operations include plane or surface milling, endmilling, facemilling, angle milling, form milling and profiling.
- milling machine ( mill)
milling machine ( mill)
Runs endmills and arbor-mounted milling cutters. Features include a head with a spindle that drives the cutters; a column, knee and table that provide motion in the three Cartesian axes; and a base that supports the components and houses the cutting-fluid pump and reservoir. The work is mounted on the table and fed into the rotating cutter or endmill to accomplish the milling steps; vertical milling machines also feed endmills into the work by means of a spindle-mounted quill. Models range from small manual machines to big bed-type and duplex mills. All take one of three basic forms: vertical, horizontal or convertible horizontal/vertical. Vertical machines may be knee-type (the table is mounted on a knee that can be elevated) or bed-type (the table is securely supported and only moves horizontally). In general, horizontal machines are bigger and more powerful, while vertical machines are lighter but more versatile and easier to set up and operate.
- toolpath( cutter path)
toolpath( cutter path)
2-D or 3-D path generated by program code or a CAM system and followed by tool when machining a part.