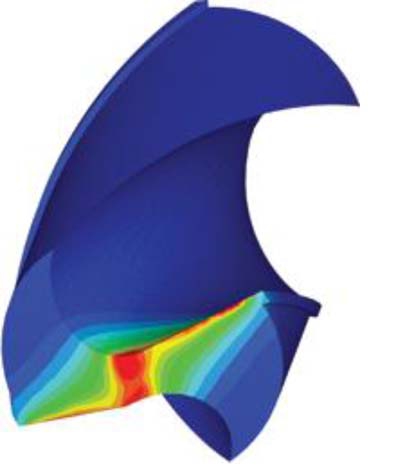
Machining modeling solutions provider Third Wave Systems offers version 6.0 of its finite element analysis product, Third Wave AdvantEdge. Third Wave AdvantEdge is physics-based material modeling technology used by companies that machine metal to optimize their cutting processes and machining strategies, providing detailed information about chip formation, temperatures, stresses, forces, and other material behavior not accessible during trial-and-error tests. The technology has become an invaluable tool for analyzing cutting tool design and performance.
Recognizing the increasing presence of high performance computing hardware, Third Wave focused significant efforts for this release on improving AdvantEdge parallel computing capabilities. AdvantEdge version 6.0 will contain enhanced algorithms that enable the software to more effectively utilize computing cores for significant computing speedups compared to version 5.9. With the release of Third Wave AdvantEdge 6.0, users will also have the opportunity to employ massively parallel computing, designating up to 40 computing cores for any given project. Benchmark testing at Third Wave has demonstrated speedups of between 10 and 20x for milling and drilling, respectively, when comparing serial mode to 40-core computing.
In addition to massively parallel computing capabilities, Third Wave AdvantEdge 6.0 will also contain enhanced material model options for 2D modeling. This new mechanism will enable more accurate characterization of flow stress behavior by allowing users to capture not only isotropic hardening components (currently available within the user-defined yield stress model), but also kinematic hardening components of reverse loading. The user-defined material model enhancement will be especially useful for companies interested in capturing detailed characteristics of workpiece surfaces, and allow users to model more complex deformation modes that could be influential when predicting residual stress. The introduction of kinematic hardening into custom material models is one more step toward giving users the opportunity to create their own comprehensive material models for more accurate results.
Contact Details
Related Glossary Terms
- flow stress
flow stress
Uniaxial true stress at the onset of plastic deformation in a metal.
- gang cutting ( milling)
gang cutting ( milling)
Machining with several cutters mounted on a single arbor, generally for simultaneous cutting.
- hardening
hardening
Process of increasing the surface hardness of a part. It is accomplished by heating a piece of steel to a temperature within or above its critical range and then cooling (or quenching) it rapidly. In any heat-treatment operation, the rate of heating is important. Heat flows from the exterior to the interior of steel at a definite rate. If the steel is heated too quickly, the outside becomes hotter than the inside and the desired uniform structure cannot be obtained. If a piece is irregular in shape, a slow heating rate is essential to prevent warping and cracking. The heavier the section, the longer the heating time must be to achieve uniform results. Even after the correct temperature has been reached, the piece should be held at the temperature for a sufficient period of time to permit its thickest section to attain a uniform temperature. See workhardening.
- milling
milling
Machining operation in which metal or other material is removed by applying power to a rotating cutter. In vertical milling, the cutting tool is mounted vertically on the spindle. In horizontal milling, the cutting tool is mounted horizontally, either directly on the spindle or on an arbor. Horizontal milling is further broken down into conventional milling, where the cutter rotates opposite the direction of feed, or “up” into the workpiece; and climb milling, where the cutter rotates in the direction of feed, or “down” into the workpiece. Milling operations include plane or surface milling, endmilling, facemilling, angle milling, form milling and profiling.
- parallel
parallel
Strip or block of precision-ground stock used to elevate a workpiece, while keeping it parallel to the worktable, to prevent cutter/table contact.
- residual stress
residual stress
Stress present in a body that is free of external forces or thermal gradients.