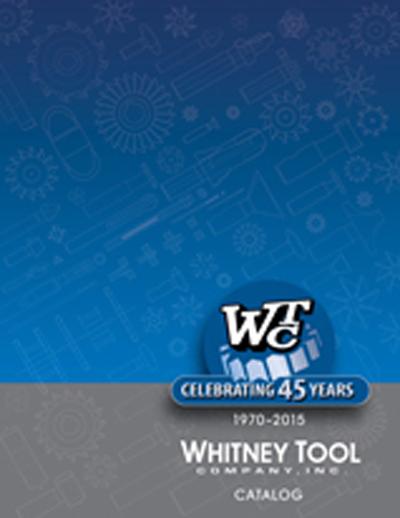
The new 2015 general catalog from Whitney Tool Co. has been expanded to 96 pages and features more than 8,000 items.
Featured products include:
• Decimal Width Slotting Cutters in M42, Carbide Tipped and Solid Carbide
• Carbide O-Ring Dovetail Cutters
• High-Performance, 3-Flute Countersinks
• Drill Extensions from #80 to 9/16"
• Tap Extensions from #0 to 1" NPT
• Tapered Endmills in HSS and Carbide
• Carbide-Tipped, Stagger-Tooth Side Mills and Slitting Saws
• A full range of specialty PVD coatings
• Screw Extractors and Extractor Extensions
• Left-Hand Drills and Drill Extensions
Additionally, Whitney Tool manufactures custom cutting tools, specializing in shank and arbor-type milling cutters in high-speed steel, cobalt, carbide tipped and solid carbide. All of this and more are detailed in the new general catalog from Whitney Tool.
Contact Details
Related Glossary Terms
- gang cutting ( milling)
gang cutting ( milling)
Machining with several cutters mounted on a single arbor, generally for simultaneous cutting.
- gang cutting ( milling)2
gang cutting ( milling)
Machining with several cutters mounted on a single arbor, generally for simultaneous cutting.
- high-speed steels ( HSS)
high-speed steels ( HSS)
Available in two major types: tungsten high-speed steels (designated by letter T having tungsten as the principal alloying element) and molybdenum high-speed steels (designated by letter M having molybdenum as the principal alloying element). The type T high-speed steels containing cobalt have higher wear resistance and greater red (hot) hardness, withstanding cutting temperature up to 1,100º F (590º C). The type T steels are used to fabricate metalcutting tools (milling cutters, drills, reamers and taps), woodworking tools, various types of punches and dies, ball and roller bearings. The type M steels are used for cutting tools and various types of dies.
- milling
milling
Machining operation in which metal or other material is removed by applying power to a rotating cutter. In vertical milling, the cutting tool is mounted vertically on the spindle. In horizontal milling, the cutting tool is mounted horizontally, either directly on the spindle or on an arbor. Horizontal milling is further broken down into conventional milling, where the cutter rotates opposite the direction of feed, or “up” into the workpiece; and climb milling, where the cutter rotates in the direction of feed, or “down” into the workpiece. Milling operations include plane or surface milling, endmilling, facemilling, angle milling, form milling and profiling.
- physical vapor deposition ( PVD)
physical vapor deposition ( PVD)
Tool-coating process performed at low temperature (500° C), compared to chemical vapor deposition (1,000° C). Employs electric field to generate necessary heat for depositing coating on a tool’s surface. See CVD, chemical vapor deposition.
- shank
shank
Main body of a tool; the portion of a drill or similar end-held tool that fits into a collet, chuck or similar mounting device.
- slotting
slotting
Machining, normally milling, that creates slots, grooves and similar recesses in workpieces, including T-slots and dovetails.
- tap
tap
Cylindrical tool that cuts internal threads and has flutes to remove chips and carry tapping fluid to the point of cut. Normally used on a drill press or tapping machine but also may be operated manually. See tapping.