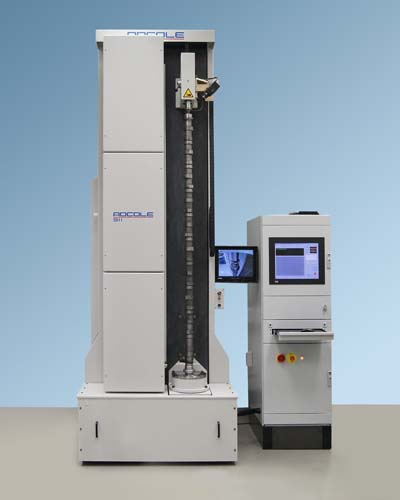
An upgraded camshaft measuring machine that is designed with a wide diameter offset follower to accommodate larger diameter cams with built-in gears is being introduced by ADCOLE Corp.
The ADCOLE Model 911 Camshaft Gage is ideal for measuring camshafts up to 90" long and has an offset follower with 6.1" travel to accommodate larger diameters with built-in gears. Featuring an air-actuated open-close of the tailstock, with a video monitor to assure the center hole is lined up and engaged, this camshaft measuring machine has a ball bearing spindle with run-out under 0.2µm and a footswitch operated tailstock restraint.
Automatically measuring 360 degrees around the part, including all cam lobes, reference journals, timing features, and keyways, the ADCOLE Model 911 Camshaft Gage is capable of the submicron detection of material buildup or other form irregularities. This cam tester has become the world standard for milling and grinding machine tool users to make certain there is product conformance among suppliers and OEMs, claims the firm.
The ADCOLE Model 911 Camshaft Gage is priced from $150,000.00 up. Price quotations and literature are available upon request.
Contact Details
Related Glossary Terms
- computer-aided manufacturing ( CAM)
computer-aided manufacturing ( CAM)
Use of computers to control machining and manufacturing processes.
- gang cutting ( milling)
gang cutting ( milling)
Machining with several cutters mounted on a single arbor, generally for simultaneous cutting.
- grinding
grinding
Machining operation in which material is removed from the workpiece by a powered abrasive wheel, stone, belt, paste, sheet, compound, slurry, etc. Takes various forms: surface grinding (creates flat and/or squared surfaces); cylindrical grinding (for external cylindrical and tapered shapes, fillets, undercuts, etc.); centerless grinding; chamfering; thread and form grinding; tool and cutter grinding; offhand grinding; lapping and polishing (grinding with extremely fine grits to create ultrasmooth surfaces); honing; and disc grinding.
- grinding machine
grinding machine
Powers a grinding wheel or other abrasive tool for the purpose of removing metal and finishing workpieces to close tolerances. Provides smooth, square, parallel and accurate workpiece surfaces. When ultrasmooth surfaces and finishes on the order of microns are required, lapping and honing machines (precision grinders that run abrasives with extremely fine, uniform grits) are used. In its “finishing” role, the grinder is perhaps the most widely used machine tool. Various styles are available: bench and pedestal grinders for sharpening lathe bits and drills; surface grinders for producing square, parallel, smooth and accurate parts; cylindrical and centerless grinders; center-hole grinders; form grinders; facemill and endmill grinders; gear-cutting grinders; jig grinders; abrasive belt (backstand, swing-frame, belt-roll) grinders; tool and cutter grinders for sharpening and resharpening cutting tools; carbide grinders; hand-held die grinders; and abrasive cutoff saws.
- milling
milling
Machining operation in which metal or other material is removed by applying power to a rotating cutter. In vertical milling, the cutting tool is mounted vertically on the spindle. In horizontal milling, the cutting tool is mounted horizontally, either directly on the spindle or on an arbor. Horizontal milling is further broken down into conventional milling, where the cutter rotates opposite the direction of feed, or “up” into the workpiece; and climb milling, where the cutter rotates in the direction of feed, or “down” into the workpiece. Milling operations include plane or surface milling, endmilling, facemilling, angle milling, form milling and profiling.