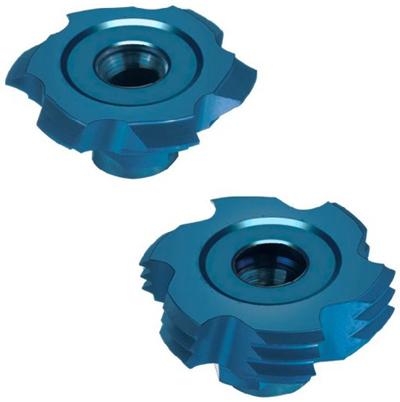
Now available in configurations for threading, grooving and chamfering, Carmex says its expanded CMT line of vertical milling inserts delivers longer tool life, higher material removal, excellent surface finish, reduced cycle times, and lower cutting forces in materials up to 62 HRC steel.
Featuring a specially ground profile incorporating four to eight cutting edges and spiral flute design and constructed of MT8 submicron carbide grade with advanced PVD triple coating, Carmex's CMT tools offer high heat resistance and smooth operation in all general-purpose applications.
Jeff Dei, President of Carmex USA, comments, "The new CMT line reflects Carmex's commitment to continuous product improvement. Our new cutters can be used with existing CMT C18 type tool holders and offer significantly improved performance thanks to the carbide grade, the PVD triple coating, and the spiral flute design for smoother cutting. Available in a wide range of profiles, including 60° and 55° partial profile for internal and external threading, and ISO and UN full profile for internal threading, we also offer multiple sizes for chamfering, grooving and boring, as well as regular and full radius groove milling."
Contact Details
Related Glossary Terms
- boring
boring
Enlarging a hole that already has been drilled or cored. Generally, it is an operation of truing the previously drilled hole with a single-point, lathe-type tool. Boring is essentially internal turning, in that usually a single-point cutting tool forms the internal shape. Some tools are available with two cutting edges to balance cutting forces.
- chamfering
chamfering
Machining a bevel on a workpiece or tool; improves a tool’s entrance into the cut.
- gang cutting ( milling)
gang cutting ( milling)
Machining with several cutters mounted on a single arbor, generally for simultaneous cutting.
- grooving
grooving
Machining grooves and shallow channels. Example: grooving ball-bearing raceways. Typically performed by tools that are capable of light cuts at high feed rates. Imparts high-quality finish.
- milling
milling
Machining operation in which metal or other material is removed by applying power to a rotating cutter. In vertical milling, the cutting tool is mounted vertically on the spindle. In horizontal milling, the cutting tool is mounted horizontally, either directly on the spindle or on an arbor. Horizontal milling is further broken down into conventional milling, where the cutter rotates opposite the direction of feed, or “up” into the workpiece; and climb milling, where the cutter rotates in the direction of feed, or “down” into the workpiece. Milling operations include plane or surface milling, endmilling, facemilling, angle milling, form milling and profiling.
- physical vapor deposition ( PVD)
physical vapor deposition ( PVD)
Tool-coating process performed at low temperature (500° C), compared to chemical vapor deposition (1,000° C). Employs electric field to generate necessary heat for depositing coating on a tool’s surface. See CVD, chemical vapor deposition.
- threading
threading
Process of both external (e.g., thread milling) and internal (e.g., tapping, thread milling) cutting, turning and rolling of threads into particular material. Standardized specifications are available to determine the desired results of the threading process. Numerous thread-series designations are written for specific applications. Threading often is performed on a lathe. Specifications such as thread height are critical in determining the strength of the threads. The material used is taken into consideration in determining the expected results of any particular application for that threaded piece. In external threading, a calculated depth is required as well as a particular angle to the cut. To perform internal threading, the exact diameter to bore the hole is critical before threading. The threads are distinguished from one another by the amount of tolerance and/or allowance that is specified. See turning.