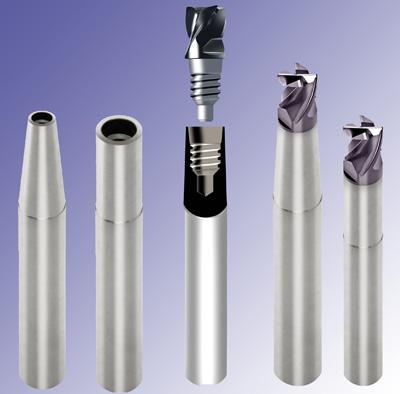
With the INOSCREW modular milling system, the tool manufacturer InovaTools says it supports tool and mold construction with a technically sophisticated and cost-effective solution. Thanks to a large number of shank shapes and different geometries, the tool system covers a wide range of applications. Flexibility, precision and reduced set-up times are arguments designed to encourage the cutter to use the new InovaTools tool family.
In the INOSCREW modular tool system, the user can choose between cylindrical tool holders (short, long, extra long) as well as conical ones (short, long) with diameters ranging from 8mm to 20mm. A special trapezoidal inner thread ensures a secure hold in the replaceable head holder. The replaceable heads are fitted with a guide pin and a ground cone in addition to the trapezoidal outer thread. In combination with the contact surface, the milling replaceable head is seated very securely in the holder with no leeway after being screwed"
Sixteen head types ensure the necessary flexibility for a range of uses. Examples include the replaceable head STARMAX for HPC milling, the roughing end mill QUICKMAX, the finishing end mill MULTICUT, different copying, full radius and ball head end mills right up to deburring devices and quarter-circle end mills. All replaceable heads are made of quality hard metal and, whether coated or uncoated, thus feature good wear resistance and toughness. This means that high cutting speeds can be achieved with INOSCREW tools.
Thanks to its many unique design features, INOSCREW scores points with the outstanding stability of the tool system, and this successfully suppresses vibrations and oscillations. In practice, INOSCREW therefore wins people over thanks to its extremely high change and concentricity accuracy, which is below 20µm. Thanks to the precision inner thread and the guide pin, the replaceable heads can be changed quickly and easily directly on the machine. The replaceable head holder does not have to be removed for this purpose. This keeps set-up times extremely low.
Ditmar Ertel, Manager of InovaTools: "Thanks to this, it takes less than 1 minute to replace a head. This is Formula 1 speed compared to replacing a complete shank end mill, which involves removing the tool holder and making fine adjustments."
Contact Details
Related Glossary Terms
- gang cutting ( milling)
gang cutting ( milling)
Machining with several cutters mounted on a single arbor, generally for simultaneous cutting.
- milling
milling
Machining operation in which metal or other material is removed by applying power to a rotating cutter. In vertical milling, the cutting tool is mounted vertically on the spindle. In horizontal milling, the cutting tool is mounted horizontally, either directly on the spindle or on an arbor. Horizontal milling is further broken down into conventional milling, where the cutter rotates opposite the direction of feed, or “up” into the workpiece; and climb milling, where the cutter rotates in the direction of feed, or “down” into the workpiece. Milling operations include plane or surface milling, endmilling, facemilling, angle milling, form milling and profiling.
- milling machine ( mill)
milling machine ( mill)
Runs endmills and arbor-mounted milling cutters. Features include a head with a spindle that drives the cutters; a column, knee and table that provide motion in the three Cartesian axes; and a base that supports the components and houses the cutting-fluid pump and reservoir. The work is mounted on the table and fed into the rotating cutter or endmill to accomplish the milling steps; vertical milling machines also feed endmills into the work by means of a spindle-mounted quill. Models range from small manual machines to big bed-type and duplex mills. All take one of three basic forms: vertical, horizontal or convertible horizontal/vertical. Vertical machines may be knee-type (the table is mounted on a knee that can be elevated) or bed-type (the table is securely supported and only moves horizontally). In general, horizontal machines are bigger and more powerful, while vertical machines are lighter but more versatile and easier to set up and operate.
- shank
shank
Main body of a tool; the portion of a drill or similar end-held tool that fits into a collet, chuck or similar mounting device.
- wear resistance
wear resistance
Ability of the tool to withstand stresses that cause it to wear during cutting; an attribute linked to alloy composition, base material, thermal conditions, type of tooling and operation and other variables.