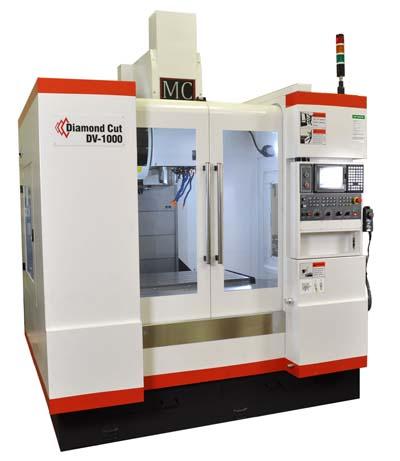
MC Machinery Systems Inc. expands its product supply chain with the new MC Milling line. The Diamond Cut general milling line is comprised of five series of vertical machining centers and drilling and tapping machines. This addition supports the company's focus on improving its products, services, and product portfolio to support U.S. manufacturers.
The MCV Series is a general purpose machining center featuring two spindle/tooling system types. The CAT-40 tooling system uses an 8,000 RPM motor and the CAT-50 tooling uses a 6,000 RPM motor. It performs well in a wide variety of applications including fixtures, mold base, and secondary operations. The series comes with coolant-thru-spindle preparation and an M70 Mitsubishi controller. The machine can be equipped with a ZF gearbox to achieve four times the torque of a standard motor.
The DV Series is a general purpose machine, featuring a 15,000 RPM direct drive spindle and CAT-40 tooling. It can accommodate smaller cutting tools for more intricate milling work, and is a popular choice among job shops because of its wide range of applications. The series comes with coolant-thru-spindle preparation and an M70 Mitsubishi controller.
The DM Series features a 20,000 RPM HSK-A63 spindle, which features a more rigid and accurate tooling system. This series excels in close-tolerance work and is ideal for applications in mold and die. The 32-position automatic tool changer provides better tool life management and boosts machine productivity. An M720 Mitsubishi controller, linear scales, and roller guideways are standard features of the DM Series.
The SV Series is built with a heavy-duty box way construction in the X, Y, and Z axes, ideal for rigidity and stability in large parts. The machine excels in maximum material removal with its ability to handle bigger tools. The machine features a 10,000 RPM spindle, CAT-50 tooling, and hand-scraped box way guides, for years of accuracy and durability. The series comes with coolant-thru-spindle preparation, an M70 Mitsubishi controller, and optional ZF gearbox for higher torque.
The TV Series of drill/tap machines feature 24,000 RPM high-speed spindle driven by a 5HP motor. BBT-30 dual contact tooling delivers extra rigidity and better Z depth control during operation. The fast and simple, two-second tool changes provide multi-axis machining all in one setup. A bi-directional tool magazine is driven through advanced PLC software which is achieved through the M70 Mitsubishi controller. A CAM-driven tool magazine allows rotation and accuracy and smooth motion even while large tools are loading.
Contact Details
Related Glossary Terms
- centers
centers
Cone-shaped pins that support a workpiece by one or two ends during machining. The centers fit into holes drilled in the workpiece ends. Centers that turn with the workpiece are called “live” centers; those that do not are called “dead” centers.
- gang cutting ( milling)
gang cutting ( milling)
Machining with several cutters mounted on a single arbor, generally for simultaneous cutting.
- machining center
machining center
CNC machine tool capable of drilling, reaming, tapping, milling and boring. Normally comes with an automatic toolchanger. See automatic toolchanger.
- milling
milling
Machining operation in which metal or other material is removed by applying power to a rotating cutter. In vertical milling, the cutting tool is mounted vertically on the spindle. In horizontal milling, the cutting tool is mounted horizontally, either directly on the spindle or on an arbor. Horizontal milling is further broken down into conventional milling, where the cutter rotates opposite the direction of feed, or “up” into the workpiece; and climb milling, where the cutter rotates in the direction of feed, or “down” into the workpiece. Milling operations include plane or surface milling, endmilling, facemilling, angle milling, form milling and profiling.
- tapping
tapping
Machining operation in which a tap, with teeth on its periphery, cuts internal threads in a predrilled hole having a smaller diameter than the tap diameter. Threads are formed by a combined rotary and axial-relative motion between tap and workpiece. See tap.