END USER: Matherne Instrumentation Specialists Inc., (985) 876-9808, www.matherneinstrumentation.com.
CHALLENGE: Extend tool life and boost productivity when milling Inconel 718.
SOLUTION: A 6-flute endmill programmed to follow a trochoidal milling toolpath.
SOLUTION PROVIDERS: IMCO Carbide Tool Inc., (800) 765-4626, www.imcousa.com; Tooling and Accessories Group Inc., (985) 507-9207
Gilbert Boquet always keeps his eyes open for new opportunities to shave machining time and reduce tool costs, especially when producing parts made of difficult-to-machine Inconel 718. Boquet is mill foreman at Matherne Instrumentation Specialists Inc., Houma, La., in the heart of the Gulf Coast oil industry. The company makes precision-calibrated instruments used in oil fields, which are demanding work environments. The instruments have to be tough—Inconel tough—to get the job done. Therefore, the cutting tools used to produce the instrument components have to be up to the task.
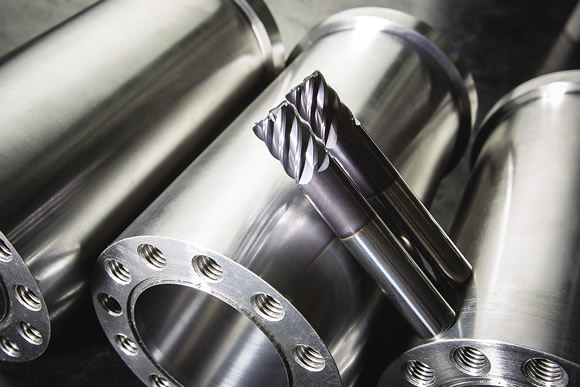
Courtesy of IMCO Carbide Tool
Matherne Instrumentation went from six tools per part to one and cut cycle time in half when milling Inconel 718 parts for precision-calibrated instruments used in oil fields after switching to Omega-6 M7 series 6-flute endmills from IMCO. Tools are shown resting on top of completed parts.
Matherne was experiencing problems when applying standard 4-flute endmills. Each part required six tools to rough at a cutting speed of 70 sfm and a feed of 1 ipm, according to Neal Wilson, a manufacturer’s representative at Tooling and Accessories Group Inc., Ponchatoula, La., which represents Perrysburg, Ohio-based IMCO Carbide Tool Inc. in Louisiana, Mississippi and Arkansas.
Wilson recommended IMCO’s Omega-6 M7 series 6-flute endmills. According to IMCO, the tool’s corner radius protects the corner from chipping and breakage and its high helix angle creates a high shear plane in the cutting zone for enhanced efficiency and chip control.
Wilson also recommended a trochoidal milling toolpath. When trochoidal milling, the toolpath maintains a constant tool engagement and feed. A constant tool engagement means less loading and unloading of a tool as it enters and exits the cut, which prolongs tool life. It also means the tool spends less time cutting air and more time removing metal.
CAM software is available to automatically generate those toolpaths, but Matherne didn’t have a CAM package at the time (but now does), Wilson noted. “After I explained the toolpath, Gilbert Boquet took the concept and long-handed his own program,” he said. “That was very impressive.”
With the program completed, Matherne tested the IMCO tools against three other brands. “No other brand was close,” Wilson said, noting Matherne was able to increase the cutting speed to 110 sfm, the feed to 4.2 ipm and up the metal-removal rate because of the two additional cutting edges on the IMCO endmills, which means less work per flute and longer tool life. As a result, only one tool was needed to rough a part.
Wilson added that by adjusting for radial chip thinning, which resulted from the more efficient toolpath, Matherne made additional productivity gains. “We were able to cut the cycle time probably in half,” he said about all the machining gains combined.
Chip thinning occurs when the WOC is less than the cutter radius. When this happens, the length of the cutting edge engagement becomes larger than the radial DOC, and the chip becomes thinner because it is distributed over a greater length of cutting edge. A thinner chip carries less heat from the cutting edge, escalating tool wear. With chip thinning adjustment, the chip returns to the desired thickness, allowing it to carry more heat from the cutting edge and extending tool life.
Matherne uses the Omega-6 M7 series endmills for other Inconel projects as well, including a complex 8½ "-dia. part with multiple windows and ¼ " lugs.
“We get better tool life,” Boquet said. “And we don’t have to replace tools as often, so we save time.”
Related Glossary Terms
- computer-aided manufacturing ( CAM)
computer-aided manufacturing ( CAM)
Use of computers to control machining and manufacturing processes.
- cutting speed
cutting speed
Tangential velocity on the surface of the tool or workpiece at the cutting interface. The formula for cutting speed (sfm) is tool diameter 5 0.26 5 spindle speed (rpm). The formula for feed per tooth (fpt) is table feed (ipm)/number of flutes/spindle speed (rpm). The formula for spindle speed (rpm) is cutting speed (sfm) 5 3.82/tool diameter. The formula for table feed (ipm) is feed per tooth (ftp) 5 number of tool flutes 5 spindle speed (rpm).
- endmill
endmill
Milling cutter held by its shank that cuts on its periphery and, if so configured, on its free end. Takes a variety of shapes (single- and double-end, roughing, ballnose and cup-end) and sizes (stub, medium, long and extra-long). Also comes with differing numbers of flutes.
- feed
feed
Rate of change of position of the tool as a whole, relative to the workpiece while cutting.
- gang cutting ( milling)
gang cutting ( milling)
Machining with several cutters mounted on a single arbor, generally for simultaneous cutting.
- helix angle
helix angle
Angle that the tool’s leading edge makes with the plane of its centerline.
- inches per minute ( ipm)
inches per minute ( ipm)
Value that refers to how far the workpiece or cutter advances linearly in 1 minute, defined as: ipm = ipt 5 number of effective teeth 5 rpm. Also known as the table feed or machine feed.
- metal-removal rate
metal-removal rate
Rate at which metal is removed from an unfinished part, measured in cubic inches or cubic centimeters per minute.
- milling
milling
Machining operation in which metal or other material is removed by applying power to a rotating cutter. In vertical milling, the cutting tool is mounted vertically on the spindle. In horizontal milling, the cutting tool is mounted horizontally, either directly on the spindle or on an arbor. Horizontal milling is further broken down into conventional milling, where the cutter rotates opposite the direction of feed, or “up” into the workpiece; and climb milling, where the cutter rotates in the direction of feed, or “down” into the workpiece. Milling operations include plane or surface milling, endmilling, facemilling, angle milling, form milling and profiling.
- milling machine ( mill)
milling machine ( mill)
Runs endmills and arbor-mounted milling cutters. Features include a head with a spindle that drives the cutters; a column, knee and table that provide motion in the three Cartesian axes; and a base that supports the components and houses the cutting-fluid pump and reservoir. The work is mounted on the table and fed into the rotating cutter or endmill to accomplish the milling steps; vertical milling machines also feed endmills into the work by means of a spindle-mounted quill. Models range from small manual machines to big bed-type and duplex mills. All take one of three basic forms: vertical, horizontal or convertible horizontal/vertical. Vertical machines may be knee-type (the table is mounted on a knee that can be elevated) or bed-type (the table is securely supported and only moves horizontally). In general, horizontal machines are bigger and more powerful, while vertical machines are lighter but more versatile and easier to set up and operate.
- shear plane
shear plane
Plane along which the chip parts from the workpiece. In orthogonal cutting, most of the energy is used to create the shear plane.
- toolpath( cutter path)
toolpath( cutter path)
2-D or 3-D path generated by program code or a CAM system and followed by tool when machining a part.