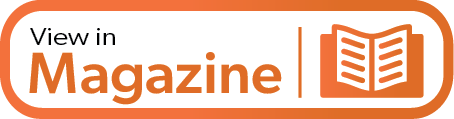
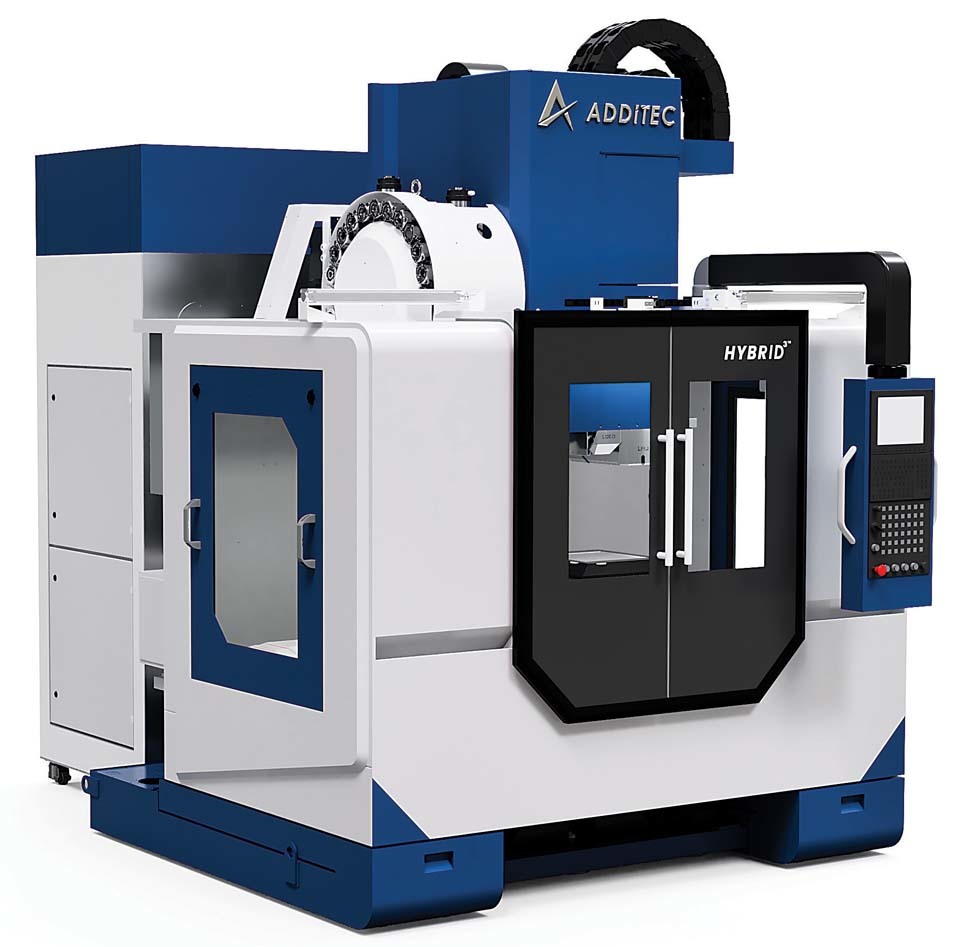
The technology is not intended to produce most parts, but a hybrid machine, which combines additive manufacturing and subtractive machining, can save a significant amount of time and money — when the application is appropriate.
DMG Mori USA reduced processing time by 80% when it switched from making ma chine drawbars with the traditional method to a hybrid approach, said Lennart Tasche, engineering manager for the Hoffman Estates, Illinois-based machine tool builder. “The core of the drawbar is still manufactured like it always has been, but instead of a complicated process of adding a hard facing material to the drawbar, we now do that in the same ma chine by switching to our laser head and de positing that second material that’s required for the necessary wear resistance.”
DMG Mori offers four hybrid 5-axis CNC machines with laser-based directed energy deposition (DED) through a powder nozzle: Lasertec 65, Lasertec 125, Lasertec 3000 and Lasertec 6600 DED hybrids. The first two are milling machines, with the number for each indicating the table diameter in centimeters, Tasche said. The other two machines are turning centers.
The Lasertec 3000 DED hybrid is for producing parts up to 670 mm × 932 mm (26.38" × 36.69") in diameter at B-axis 180° or up to 400 mm × 1,321 mm (15.75" × 52.01") at B-axis 90°. It can be ordered with an extended bed to double the length for even larger parts, he added. The Lasertec 6600 DED hybrid handles workpieces up to 1,010 mm × 3,702 mm (39.76" × 145.75") in diameter.
The turning machines have an A and B spindle and an upper and lower turret with live tooling, and the laser head is loaded into the upper turret, Tasche noted. “The two spindles can run independently from each other.”
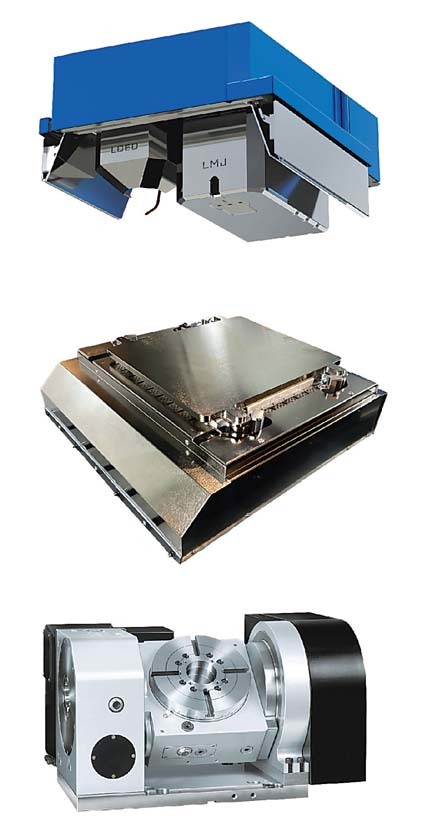
Repairing parts is a major application for the hybrid machines, he said, with other significant ones being the creation of internal cooling channels, cladding and depositing coatings. For example, a die with a worn wear surface is repaired by machining off a thin layer of the worn material, then cladded via 3D printing with either the same material or an advanced material and finish machined to bring the die back to its original shape. “All of that,” Tasche said, “in one machine without having to bring the part from one ma chine to another and reposition it and fixture it.”
Typically, he added, the thickness of a deposited layer is about 1 mm (0.039") that is adjustable with parameter settings, but an additive technology is available to re duce the thickness to about 0.1 mm (0.004") when coating rotary items.
More than One Metal
A standard DED hybrid machine comes with two hoppers for storing powder, enabling users to load two materials into the machine, Tasche said. That arrangement enables mold and die makers, for instance, to produce a part with a copper core that’s finished with steel. “We can really get the best of both worlds of having a long-lasting mold with good heat transfer.”
Not only can one metal be placed on top of another, he added, but a gradual transition between the two metals can occur. An application might require starting with 100% deposition of one powder, and then slowly reducing it to 75%, and depositing a second material for the remaining 25% before transitioning to a 50/50 composition. That’s followed by depositing 25% of the first material and 75% of the second, then finishing with 100% deposition of the second powder.
If more than two metals must be printed, a special hybrid machine can be ordered with more than two hoppers, Tasche said. Another option is to print with two hoppers, and, when the machine is printing the second metal, exchange the hopper for the first metal with a hopper containing a third metal powder. “You pretty much have un limited material combinations in that machine.”
DMG Mori does not produce the powders but uses a supplier network to provide them to its hybrid machine customers, he noted. Nonetheless, a customer can purchase powder from any supplier. Because powder quality is critical to effective 3D printing, the machine builder offers powder testing at a laboratory that quantifies various qualities of a powder, such as particle size distribution, flowability and humidity. “In general, powder quality is nothing that will ever harm the machine. It’s just something that you want to keep an eye on for successful printing.”
Down to the Wire
ADDiTEC is another machine tool builder that provides equipment to 3D print with laser deposited energy deposition and 5-axis CNC machining with 3+2 motion axes, but also combines that AM technology with the liquid metal jetting (LMJ) additive process in its Hybrid3 machine. The Palm City, Florida-based company also offers the Hybrid2 machine, which com bines LMJ and 5-axis CNC machining.
ADDiTEC introduced the equipment last year after acquiring the LMJ technology to complement its existing laser DED technology, said Sriram Manoharan, R&D program manager. LMJ provides a high level of resolution to print complex features while laser DED enables a high deposition rate.
However, instead of using powder, the machines use off-the-shelf welding wire to print iron, nickel, aluminum and copper alloys, he said. Using wire avoids having to don the personal protective equipment, including a respirator mask, clothing and gloves, required to handle powder. “The powder is toxic,” noted Manoharan.
The standard wire sizes are from 0.8 mm to 1.6 mm (0.031" to 0.063"), with the larger wire enabling a higher deposition rate, he explained. “With a smaller wire diameter, you can attack complicated thin-wall features.”
A suitable application for the Hybrid2 machine is part repair, he continued. For example, a turbine blade with a broken tip can be machined to prepare that surface for 3D printing and then finish machined to meet the specifications. “You always require a post-process finishing operation to get that additive part into functional shape.
Producing intricate features within a part is another application, such as a curved cooling pipe, Manoharan explained. Creating that feature may require printing a few layers followed by internal machining, then more printing and more machining until completed.
The Hybrid3, on the other hand, has two additive technologies to offer multiple-material capability, he added. This ability, for example, enables printing a lightweight aluminum structure in a part’s interior and a high-strength exterior structure.
Manoharan said machine installation and training takes one week, in part because most CNC machine programmers and operators are familiar with Mastercam CAD/CAM software. “Our additive technologies are just add-ons or plug-ins to Mastercam. Inputting parameters to 3D print and machine is straight forward because we’re using the same Mastercam platform to do the additive modules as well.”
In the U.S., ADDiTEC is primarily focusing on machine shops serving the defense, aerospace, automotive and energy sectors for its hybrid machines, he said, with annual production volumes for suitable applications ranging from 10 to 10,000 parts.
Moving forward, the company plans to achieve higher deposition rates and higher power rates than its current technology, according to Manoharan. “What we want to do with our laser wire DED system is to try to match the depositions rates of wire arc additive manufacturing.”
Improved Part Repair
To enhance the performance of a hybrid machine, especially when repairing parts, Tasche said DMG Mori introduced a scanning unit feature this year that resides in the toolchanger and can be pulled from the changer to scan a part and generate a digital point cloud. The point cloud is then compared to the original CAD file of the part being machined. That comparison determines if there are any deviations in the part or if any areas are worn or bent.
“By getting that differential between the part that’s currently in your machine and the original CAD file of the part, you can then easily jump to the repair,” Tasche said.
By comparing the data that’s received automatically from the scanning unit, a worn area on a mold, for example, can be quickly uncovered and targeted for repair, Tasche said. “With the scanning, you have an automated repair solution that detects where my worn areas are and what’s the best strategy to re pair them.”
For optimal and verifiable work piece quality, it is crucial to continuously monitor and control the important AM process variables, according to DMG Mori. To achieve that, it offers the AM Assistant option, which is a combination of hardware and software for Lasertec DED hybrid machines, as well as for the Lasertec 65 DED machine. AM Assistant monitors variables such as laser power, powder mass flow, shielding gas, as well as melt pool temperature and size.
In addition, the option measures and monitors the distance between the nozzle and melt pool. “We have a certain distance, depending on the application, of 13 to 25 mm between the tip of the laser head and the part,” Tasche said. “We can detect any changes to the distance that we didn’t plan for.”
That would occur if too much or too little material is deposited, he added, increasing or shrinking the distance. “As soon as some of the metrics are not perfectly what you want them to be, it alerts you and enables you to make changes to it.”
As more metal part manufacturers develop applications for hybrid machines, including the ability to produce products that would be impossible to machine conventionally, Tasche said DMG Mori sees a constantly rising demand. “In the U.S., it’s a really strong market that seems to appreciate the capabilities of this technology.”
Related Glossary Terms
- alloys
alloys
Substances having metallic properties and being composed of two or more chemical elements of which at least one is a metal.
- centers
centers
Cone-shaped pins that support a workpiece by one or two ends during machining. The centers fit into holes drilled in the workpiece ends. Centers that turn with the workpiece are called “live” centers; those that do not are called “dead” centers.
- computer numerical control ( CNC)
computer numerical control ( CNC)
Microprocessor-based controller dedicated to a machine tool that permits the creation or modification of parts. Programmed numerical control activates the machine’s servos and spindle drives and controls the various machining operations. See DNC, direct numerical control; NC, numerical control.
- computer-aided design ( CAD)
computer-aided design ( CAD)
Product-design functions performed with the help of computers and special software.
- copper alloys
copper alloys
Copper containing specified quantities of alloying elements added to obtain the necessary mechanical and physical properties. The most common copper alloys are divided into six groups, and each group contains one of the following major alloying elements: brasses—major alloying element is zinc; phosphor bronzes—major alloying element is tin; aluminum bronzes—major alloying element is aluminum; silicon bronzes—major alloying element is silicon; copper-nickels and nickel-silvers—major alloying element is nickel; and dilute-copper or high-copper alloys, which contain small amounts of various elements such as beryllium, cadmium, chromium or iron.
- fixture
fixture
Device, often made in-house, that holds a specific workpiece. See jig; modular fixturing.
- gang cutting ( milling)
gang cutting ( milling)
Machining with several cutters mounted on a single arbor, generally for simultaneous cutting.
- lapping compound( powder)
lapping compound( powder)
Light, abrasive material used for finishing a surface.
- milling
milling
Machining operation in which metal or other material is removed by applying power to a rotating cutter. In vertical milling, the cutting tool is mounted vertically on the spindle. In horizontal milling, the cutting tool is mounted horizontally, either directly on the spindle or on an arbor. Horizontal milling is further broken down into conventional milling, where the cutter rotates opposite the direction of feed, or “up” into the workpiece; and climb milling, where the cutter rotates in the direction of feed, or “down” into the workpiece. Milling operations include plane or surface milling, endmilling, facemilling, angle milling, form milling and profiling.
- toolchanger
toolchanger
Carriage or drum attached to a machining center that holds tools until needed; when a tool is needed, the toolchanger inserts the tool into the machine spindle. See automatic toolchanger.
- turning
turning
Workpiece is held in a chuck, mounted on a face plate or secured between centers and rotated while a cutting tool, normally a single-point tool, is fed into it along its periphery or across its end or face. Takes the form of straight turning (cutting along the periphery of the workpiece); taper turning (creating a taper); step turning (turning different-size diameters on the same work); chamfering (beveling an edge or shoulder); facing (cutting on an end); turning threads (usually external but can be internal); roughing (high-volume metal removal); and finishing (final light cuts). Performed on lathes, turning centers, chucking machines, automatic screw machines and similar machines.
- wear resistance
wear resistance
Ability of the tool to withstand stresses that cause it to wear during cutting; an attribute linked to alloy composition, base material, thermal conditions, type of tooling and operation and other variables.