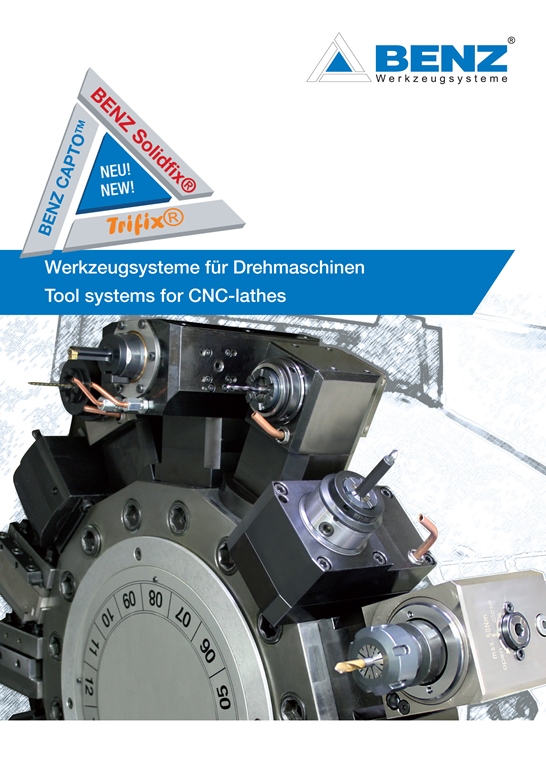
BENZ Inc., Charlotte, N.C., has released new catalogs for its Solidfix, CAPTO and Trifix modular quick-change tooling systems. BENZ specializes in tooling systems for turning and milling machines such as live and static tools, angle heads, multi-spindle heads, spindle speeders, large scale drill heads, 5-axis heads, and its lines of modular tooling systems. BENZ tooling systems are engineered in Germany and sold and serviced in the U.S. and Canada by Benz Inc.
BENZ has published a 60-page catalog for its latest proprietary modular tooling system, the Solidfix line. The new system reduces setup times for tools by up to 90 percent with 15 second tool changes, according to the company.
Another new catalog details BENZ's CAPTO modular quick-change system, which features a compact design that can be used for milling, drilling and turning with up to 100 bar coolant pressure.
BENZ also released a catalog featuring LinTec push-type broaching tools, which the company says provide a range of additional machining processes, such as torx, internal and external splines, involute gears/shafts, hexagon sockets and grooves.
Each full-color catalog provides product descriptions, technical specifications and parts breakdown, complete with product ordering information, inquiry forms, and available options and tooling accessories data. To download electronic versions of each catalog, visit www.benz-inc.com, or request a hard copy by calling (704) 529-5300.
Related Glossary Terms
- broaching
broaching
Operation in which a cutter progressively enlarges a slot or hole or shapes a workpiece exterior. Low teeth start the cut, intermediate teeth remove the majority of the material and high teeth finish the task. Broaching can be a one-step operation, as opposed to milling and slotting, which require repeated passes. Typically, however, broaching also involves multiple passes.
- coolant
coolant
Fluid that reduces temperature buildup at the tool/workpiece interface during machining. Normally takes the form of a liquid such as soluble or chemical mixtures (semisynthetic, synthetic) but can be pressurized air or other gas. Because of water’s ability to absorb great quantities of heat, it is widely used as a coolant and vehicle for various cutting compounds, with the water-to-compound ratio varying with the machining task. See cutting fluid; semisynthetic cutting fluid; soluble-oil cutting fluid; synthetic cutting fluid.
- gang cutting ( milling)
gang cutting ( milling)
Machining with several cutters mounted on a single arbor, generally for simultaneous cutting.
- milling
milling
Machining operation in which metal or other material is removed by applying power to a rotating cutter. In vertical milling, the cutting tool is mounted vertically on the spindle. In horizontal milling, the cutting tool is mounted horizontally, either directly on the spindle or on an arbor. Horizontal milling is further broken down into conventional milling, where the cutter rotates opposite the direction of feed, or “up” into the workpiece; and climb milling, where the cutter rotates in the direction of feed, or “down” into the workpiece. Milling operations include plane or surface milling, endmilling, facemilling, angle milling, form milling and profiling.
- modular tooling
modular tooling
1. Tooling system comprised of standardized tools and toolholders. 2. Devices that allow rapid mounting and replacement of tools. Commonly used with carousel toolchangers and other computerized machining operations. See toolchanger; toolholder.
- turning
turning
Workpiece is held in a chuck, mounted on a face plate or secured between centers and rotated while a cutting tool, normally a single-point tool, is fed into it along its periphery or across its end or face. Takes the form of straight turning (cutting along the periphery of the workpiece); taper turning (creating a taper); step turning (turning different-size diameters on the same work); chamfering (beveling an edge or shoulder); facing (cutting on an end); turning threads (usually external but can be internal); roughing (high-volume metal removal); and finishing (final light cuts). Performed on lathes, turning centers, chucking machines, automatic screw machines and similar machines.