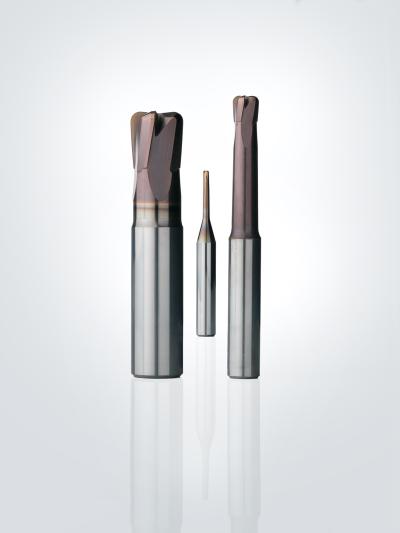
Seco Tools released two new solid-carbide endmills that significantly boost metal-removal rates and offer exceptionally long tool life for a variety of today’s challenging workpiece materials. The Jabro-HFM JHF181 is suitable for high-feed milling strategies in hardened steels and nickel-based alloys, while the Jabro-Solid2 JS564 and JS565 represent Seco’s continued focus on developing tools for optimized roughing strategies for materials such as steels, stainless steels and titanium alloys.
As the latest member in the Seco high-feed family, the new Jabro-HFM JHF181 offers the same performance as other Seco high-feed tooling solutions as well as increases metal removal rates by up to 30 percent over traditional methods. The JHF181 is especially effective at machining complex parts that require long tool overhangs and a mix of multiple axial and radial machining operations. It also provides up to 30 percent more tool life than other comparable solid-carbide endmills when processing ISO H materials, the company reports. With Seco’s new HXT coating, the JHF181 gains a hard layer that delivers advanced thermal protection and high wear resistance.
The JHF181 is available in 2-, 4- or 5-flute options with cutting diameters from 0.0787" (2 mm) to 0.6299" (16 mm) and length options ranging from 2xD to 7xD. This end mill also has through-tool coolant capability for diameters from 0.2362" (6 mm) to 0.4724" (12mm.)
Designed for optimized roughing strategies, the new Jabro-Solid2 JS564 and JS565 offer 20 percent longer tool life than their predecessors due to stable tapered cores, polished NXT coatings and other high-performance features. The JS564 and JS565 provide a relatively high radial engagement while maintaining high feeds and speeds for optimized roughing passes. Furthermore, the positive frontal teeth geometries on these two endmills make them successful in axial and helical interpolation operations.
New, optimized chip splitter options on the endmills create small chips when using long cutting lengths, ensuring the best possible chip evacuation. This proves especially beneficial when machining deep pockets and reduces operational risks, such as tool breakage and workpiece scrap.
The JS564 and JS565 are available in 4- and 5-flute designs in a broad range of cutting diameters and lengths. The JS565 is also available without chip splitters. For both the JS564 and JS565, cylindrical shank diameters are available from 0.1181" (3 mm) to 0.7874" (20 mm), and Weldon shank diameters are available from 0.2362" (6 mm) to 0.7874" (20 mm.) All of these options are stocked products.
Contact Details
Related Glossary Terms
- alloys
alloys
Substances having metallic properties and being composed of two or more chemical elements of which at least one is a metal.
- coolant
coolant
Fluid that reduces temperature buildup at the tool/workpiece interface during machining. Normally takes the form of a liquid such as soluble or chemical mixtures (semisynthetic, synthetic) but can be pressurized air or other gas. Because of water’s ability to absorb great quantities of heat, it is widely used as a coolant and vehicle for various cutting compounds, with the water-to-compound ratio varying with the machining task. See cutting fluid; semisynthetic cutting fluid; soluble-oil cutting fluid; synthetic cutting fluid.
- gang cutting ( milling)
gang cutting ( milling)
Machining with several cutters mounted on a single arbor, generally for simultaneous cutting.
- interpolation
interpolation
Process of generating a sufficient number of positioning commands for the servomotors driving the machine tool so the path of the tool closely approximates the ideal path. See CNC, computer numerical control; NC, numerical control.
- milling
milling
Machining operation in which metal or other material is removed by applying power to a rotating cutter. In vertical milling, the cutting tool is mounted vertically on the spindle. In horizontal milling, the cutting tool is mounted horizontally, either directly on the spindle or on an arbor. Horizontal milling is further broken down into conventional milling, where the cutter rotates opposite the direction of feed, or “up” into the workpiece; and climb milling, where the cutter rotates in the direction of feed, or “down” into the workpiece. Milling operations include plane or surface milling, endmilling, facemilling, angle milling, form milling and profiling.
- milling machine ( mill)
milling machine ( mill)
Runs endmills and arbor-mounted milling cutters. Features include a head with a spindle that drives the cutters; a column, knee and table that provide motion in the three Cartesian axes; and a base that supports the components and houses the cutting-fluid pump and reservoir. The work is mounted on the table and fed into the rotating cutter or endmill to accomplish the milling steps; vertical milling machines also feed endmills into the work by means of a spindle-mounted quill. Models range from small manual machines to big bed-type and duplex mills. All take one of three basic forms: vertical, horizontal or convertible horizontal/vertical. Vertical machines may be knee-type (the table is mounted on a knee that can be elevated) or bed-type (the table is securely supported and only moves horizontally). In general, horizontal machines are bigger and more powerful, while vertical machines are lighter but more versatile and easier to set up and operate.
- shank
shank
Main body of a tool; the portion of a drill or similar end-held tool that fits into a collet, chuck or similar mounting device.
- stainless steels
stainless steels
Stainless steels possess high strength, heat resistance, excellent workability and erosion resistance. Four general classes have been developed to cover a range of mechanical and physical properties for particular applications. The four classes are: the austenitic types of the chromium-nickel-manganese 200 series and the chromium-nickel 300 series; the martensitic types of the chromium, hardenable 400 series; the chromium, nonhardenable 400-series ferritic types; and the precipitation-hardening type of chromium-nickel alloys with additional elements that are hardenable by solution treating and aging.
- wear resistance
wear resistance
Ability of the tool to withstand stresses that cause it to wear during cutting; an attribute linked to alloy composition, base material, thermal conditions, type of tooling and operation and other variables.