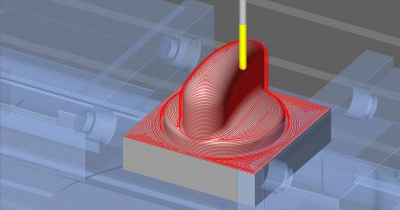
CAM software developer DP Technology Corp. announced the release of ESPRIT 2017, the latest version of its flagship product. ESPRIT 2017 delivers a smarter, simpler, faster machining process with expert toolpath, streamlined user control, and accelerated processing power, the company reports.
ESPRIT 2017 features a new 3-axis Global Finishing cycle that provides a comprehensive solution for steep/shallow milling of complex part geometries. Global Finishing optimizes machining by applying the most-appropriate toolpath to complex parts based on an analysis of the model and a single threshold angle. Z-level cutting passes are applied to steep areas and boundary offset passes to shallow areas using a sophisticated logic that gives priority to continuity of toolpath between steep and shallow areas for smoother finishing. A timesaving option constructs toolpath to machine over openings and holes in the CAD model without stopping or retracting the tool.
A redesign of ESPRIT facing dramatically reduces the number of steps needed to face a part. Up-to-the-minute intelligence about the shape of in-process stock is now built into facing, pocketing, and contour milling for faster, more reliable programming. The stock automation engine inside ESPRIT 2017 underwent a refactoring to reduce calculation times from minutes to seconds for facing, pocketing and contouring operations. The same refactoring was applied to ESPRIT’s 3-axis roughing to compute in-process stock in dramatically less time, even on complex parts.
Awkward profiles in wire EDM parts are now cut more efficiently with new support for open profiles in EDM pocketing. When a profile is interspersed with small or oddly shaped openings, the wire can be programmed in ESPRIT 2017 to ignore those openings for a simple slug drop, then followed up with precise no-core pocketing that burns away only the small pockets of material that remain.
Advancements in ESPRIT’s ProfitMilling technology improve performance inside closed cavities for better chip evacuation and coolant access, and faster attainment of the programmed feed rate. Lathe contouring has even more options for accurately positioning the tool edge along walls, at the start or end of cutting passes, and between walls. Lathe programming enhancements are particularly advantageous when contouring with round or grooving inserts.
A bevy of enhancements to 5-axis swarf milling has improved its responsiveness to a wider range of unusual part shapes for smoother, more reliable machining. Automatic machining over gaps in surfaces, reliable pass extensions along ribs, and smoother positioning of the tool along walls with irregular borders eliminate the time-consuming process of creating extra geometry on complex 5-axis parts.
Contact Details
Related Glossary Terms
- computer-aided design ( CAD)
computer-aided design ( CAD)
Product-design functions performed with the help of computers and special software.
- computer-aided manufacturing ( CAM)
computer-aided manufacturing ( CAM)
Use of computers to control machining and manufacturing processes.
- coolant
coolant
Fluid that reduces temperature buildup at the tool/workpiece interface during machining. Normally takes the form of a liquid such as soluble or chemical mixtures (semisynthetic, synthetic) but can be pressurized air or other gas. Because of water’s ability to absorb great quantities of heat, it is widely used as a coolant and vehicle for various cutting compounds, with the water-to-compound ratio varying with the machining task. See cutting fluid; semisynthetic cutting fluid; soluble-oil cutting fluid; synthetic cutting fluid.
- electrical-discharge machining ( EDM)
electrical-discharge machining ( EDM)
Process that vaporizes conductive materials by controlled application of pulsed electrical current that flows between a workpiece and electrode (tool) in a dielectric fluid. Permits machining shapes to tight accuracies without the internal stresses conventional machining often generates. Useful in diemaking.
- feed
feed
Rate of change of position of the tool as a whole, relative to the workpiece while cutting.
- gang cutting ( milling)
gang cutting ( milling)
Machining with several cutters mounted on a single arbor, generally for simultaneous cutting.
- grooving
grooving
Machining grooves and shallow channels. Example: grooving ball-bearing raceways. Typically performed by tools that are capable of light cuts at high feed rates. Imparts high-quality finish.
- lathe
lathe
Turning machine capable of sawing, milling, grinding, gear-cutting, drilling, reaming, boring, threading, facing, chamfering, grooving, knurling, spinning, parting, necking, taper-cutting, and cam- and eccentric-cutting, as well as step- and straight-turning. Comes in a variety of forms, ranging from manual to semiautomatic to fully automatic, with major types being engine lathes, turning and contouring lathes, turret lathes and numerical-control lathes. The engine lathe consists of a headstock and spindle, tailstock, bed, carriage (complete with apron) and cross slides. Features include gear- (speed) and feed-selector levers, toolpost, compound rest, lead screw and reversing lead screw, threading dial and rapid-traverse lever. Special lathe types include through-the-spindle, camshaft and crankshaft, brake drum and rotor, spinning and gun-barrel machines. Toolroom and bench lathes are used for precision work; the former for tool-and-die work and similar tasks, the latter for small workpieces (instruments, watches), normally without a power feed. Models are typically designated according to their “swing,” or the largest-diameter workpiece that can be rotated; bed length, or the distance between centers; and horsepower generated. See turning machine.
- milling
milling
Machining operation in which metal or other material is removed by applying power to a rotating cutter. In vertical milling, the cutting tool is mounted vertically on the spindle. In horizontal milling, the cutting tool is mounted horizontally, either directly on the spindle or on an arbor. Horizontal milling is further broken down into conventional milling, where the cutter rotates opposite the direction of feed, or “up” into the workpiece; and climb milling, where the cutter rotates in the direction of feed, or “down” into the workpiece. Milling operations include plane or surface milling, endmilling, facemilling, angle milling, form milling and profiling.
- swarf
swarf
Metal fines and grinding wheel particles generated during grinding.
- toolpath( cutter path)
toolpath( cutter path)
2-D or 3-D path generated by program code or a CAM system and followed by tool when machining a part.
- wire EDM
wire EDM
Process similar to ram electrical-discharge machining except a small-diameter copper or brass wire is used as a traveling electrode. Usually used in conjunction with a CNC and only works when a part is to be cut completely through. A common analogy is wire electrical-discharge machining is like an ultraprecise, electrical, contour-sawing operation.