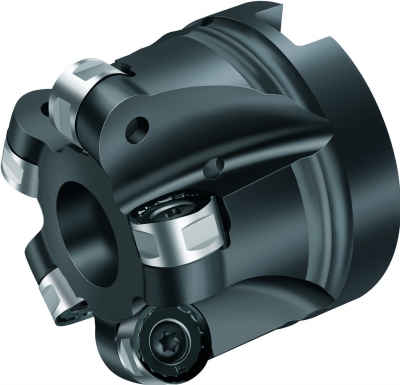
Walter has introduced the M2471, a copy milling cutter with excellent cost efficiency thanks to its high metal-removal rate -- even on low performance machines, coupled with lower cutting material costs resulting from its eight cutting edges (four per side) per insert. These 12 mm positive cutting geometry, round inserts with negative basic shape feature Walter's Tiger·tec Silver coating, ensuring maximum tool life.
In addition, the M2471 displays a high level of process reliability because of the stability of its indexable inserts, bolstered by Torx Plus screws. This new copy milling cutter is particularly well suited for the machining of turbine blades, but also has applications in face milling of steel, stainless steel and difficult-to-cut materials.
The inserts for the M2471 are available in grade WSP45S, and two geometries: D57 and F67. The D57 "universal" geometry is for medium machining conditions, while F67 "the light cutting one," is for good machining conditions with low cutting forces and medium feedrates. Diameter range for these sintered design inserts is 2-2.5 in. (32-63 mm).
Recommended DOC for the M2471 is 0.16 in. (4 mm). It is available with modular ScrewFit interface or shell mill mount.
Contact Details
Related Glossary Terms
- gang cutting ( milling)
gang cutting ( milling)
Machining with several cutters mounted on a single arbor, generally for simultaneous cutting.
- metal-removal rate
metal-removal rate
Rate at which metal is removed from an unfinished part, measured in cubic inches or cubic centimeters per minute.
- milling
milling
Machining operation in which metal or other material is removed by applying power to a rotating cutter. In vertical milling, the cutting tool is mounted vertically on the spindle. In horizontal milling, the cutting tool is mounted horizontally, either directly on the spindle or on an arbor. Horizontal milling is further broken down into conventional milling, where the cutter rotates opposite the direction of feed, or “up” into the workpiece; and climb milling, where the cutter rotates in the direction of feed, or “down” into the workpiece. Milling operations include plane or surface milling, endmilling, facemilling, angle milling, form milling and profiling.
- milling cutter
milling cutter
Loosely, any milling tool. Horizontal cutters take the form of plain milling cutters, plain spiral-tooth cutters, helical cutters, side-milling cutters, staggered-tooth side-milling cutters, facemilling cutters, angular cutters, double-angle cutters, convex and concave form-milling cutters, straddle-sprocket cutters, spur-gear cutters, corner-rounding cutters and slitting saws. Vertical cutters use shank-mounted cutting tools, including endmills, T-slot cutters, Woodruff keyseat cutters and dovetail cutters; these may also be used on horizontal mills. See milling.
- milling machine ( mill)
milling machine ( mill)
Runs endmills and arbor-mounted milling cutters. Features include a head with a spindle that drives the cutters; a column, knee and table that provide motion in the three Cartesian axes; and a base that supports the components and houses the cutting-fluid pump and reservoir. The work is mounted on the table and fed into the rotating cutter or endmill to accomplish the milling steps; vertical milling machines also feed endmills into the work by means of a spindle-mounted quill. Models range from small manual machines to big bed-type and duplex mills. All take one of three basic forms: vertical, horizontal or convertible horizontal/vertical. Vertical machines may be knee-type (the table is mounted on a knee that can be elevated) or bed-type (the table is securely supported and only moves horizontally). In general, horizontal machines are bigger and more powerful, while vertical machines are lighter but more versatile and easier to set up and operate.