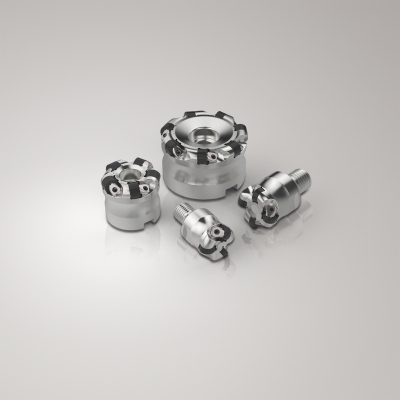
Seco Tools offers Secomax CS300 ceramic inserts and cutter bodies to boost productivity in milling and turning operations with heavy interrupted cuts on nickel-based heat-resistant superalloys (HRSA). The new cutters increase productivity by up to eight times over standard carbide milling and are ideal for machining a range of components for aerospace and power generation turbine segments, according to the company.
CS300 inserts are SiAlON-type ceramics that offer high notch wear resistance, toughness and thermal shock resistance. The inserts provide optimum flank wear resistance at higher cutting speeds ranging from 1,970 to 3,940 feet (600 to 1,200 meters) per minute and enable feeds from 0.002 to 0.006 inches (0.05 to 0.15 mm) per tooth. Combined, these attributes reduce machining cost per workpiece, increase output and lower energy consumption.
The new R220.26 and R217.26 cutter bodies are hardened and nickel-coated for high reliability, reduced chip friction and better resistance to high temperatures. Wedge clamps provide more secure insert locking and feature internal air coolant channels that ensure optimum chip evacuation and heat control. The metric range includes cutter bodies with RP 1204 inserts for facing and pocketing in diameters from 32 to 50 mm. Cutters with RN 1207 and RN 1204 inserts for facing are available in diameters from 32 to 125 mm. The imperial range includes diameters 2.0", 2.5" and 3.0".
Contact Details
Related Glossary Terms
- ceramics
ceramics
Cutting tool materials based on aluminum oxide and silicon nitride. Ceramic tools can withstand higher cutting speeds than cemented carbide tools when machining hardened steels, cast irons and high-temperature alloys.
- coolant
coolant
Fluid that reduces temperature buildup at the tool/workpiece interface during machining. Normally takes the form of a liquid such as soluble or chemical mixtures (semisynthetic, synthetic) but can be pressurized air or other gas. Because of water’s ability to absorb great quantities of heat, it is widely used as a coolant and vehicle for various cutting compounds, with the water-to-compound ratio varying with the machining task. See cutting fluid; semisynthetic cutting fluid; soluble-oil cutting fluid; synthetic cutting fluid.
- flank wear
flank wear
Reduction in clearance on the tool’s flank caused by contact with the workpiece. Ultimately causes tool failure.
- gang cutting ( milling)
gang cutting ( milling)
Machining with several cutters mounted on a single arbor, generally for simultaneous cutting.
- milling
milling
Machining operation in which metal or other material is removed by applying power to a rotating cutter. In vertical milling, the cutting tool is mounted vertically on the spindle. In horizontal milling, the cutting tool is mounted horizontally, either directly on the spindle or on an arbor. Horizontal milling is further broken down into conventional milling, where the cutter rotates opposite the direction of feed, or “up” into the workpiece; and climb milling, where the cutter rotates in the direction of feed, or “down” into the workpiece. Milling operations include plane or surface milling, endmilling, facemilling, angle milling, form milling and profiling.
- superalloys
superalloys
Tough, difficult-to-machine alloys; includes Hastelloy, Inconel and Monel. Many are nickel-base metals.
- turning
turning
Workpiece is held in a chuck, mounted on a face plate or secured between centers and rotated while a cutting tool, normally a single-point tool, is fed into it along its periphery or across its end or face. Takes the form of straight turning (cutting along the periphery of the workpiece); taper turning (creating a taper); step turning (turning different-size diameters on the same work); chamfering (beveling an edge or shoulder); facing (cutting on an end); turning threads (usually external but can be internal); roughing (high-volume metal removal); and finishing (final light cuts). Performed on lathes, turning centers, chucking machines, automatic screw machines and similar machines.
- wear resistance
wear resistance
Ability of the tool to withstand stresses that cause it to wear during cutting; an attribute linked to alloy composition, base material, thermal conditions, type of tooling and operation and other variables.