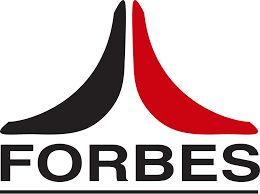
Forbes & Co. Ltd., Mumbai, India, and MachiningCloud Inc., Camarillo, Calif., are partnering to provide Forbes & Co. product data in the cloud. Forbes manufactures precision engineering tools under the brand Totem for threading, milling, drilling and deburring for industrial applications. MachiningCloud is a product data provider for cutting tools, CNC machines and workholding. The Forbes-MachiningCloud partnership will utilize the convenience of cloud-based technology. This will enable customers to optimize the way they gather information for their manufacturing operations by reducing their need to research multiple catalogs or websites seeking the proper cutting tool that best fits their cutting conditions. Furthermore, Forbes' customers will be able to increase their productivity and to achieve greater accuracy by easily downloading descriptive, usage and geometric information directly into their shop-floor software, such as CAM, simulation and tool management systems.
Ravinder Prem, COO of the engineering solution group for Forbes & Co., stated, "MachiningCloud will facilitate Totem to reach out to (our) varied customer base with our technology solution(s) for different applications. This step is in line with our vision of empowering customer(s) with innovative technological solutions. We are happy to partner with MachiningCloud."
"We are excited to help customers save time and increase efficiency by offering Forbes product data on the cloud. Customers will be able to quickly find the right tools for their jobs without spending too much time searching through various resources. All they need will be in one place", said Christophe Rogazy, director of product management for MachiningCloud.
Contact Details
Related Glossary Terms
- computer numerical control ( CNC)
computer numerical control ( CNC)
Microprocessor-based controller dedicated to a machine tool that permits the creation or modification of parts. Programmed numerical control activates the machine’s servos and spindle drives and controls the various machining operations. See DNC, direct numerical control; NC, numerical control.
- computer-aided manufacturing ( CAM)
computer-aided manufacturing ( CAM)
Use of computers to control machining and manufacturing processes.
- gang cutting ( milling)
gang cutting ( milling)
Machining with several cutters mounted on a single arbor, generally for simultaneous cutting.
- milling
milling
Machining operation in which metal or other material is removed by applying power to a rotating cutter. In vertical milling, the cutting tool is mounted vertically on the spindle. In horizontal milling, the cutting tool is mounted horizontally, either directly on the spindle or on an arbor. Horizontal milling is further broken down into conventional milling, where the cutter rotates opposite the direction of feed, or “up” into the workpiece; and climb milling, where the cutter rotates in the direction of feed, or “down” into the workpiece. Milling operations include plane or surface milling, endmilling, facemilling, angle milling, form milling and profiling.
- threading
threading
Process of both external (e.g., thread milling) and internal (e.g., tapping, thread milling) cutting, turning and rolling of threads into particular material. Standardized specifications are available to determine the desired results of the threading process. Numerous thread-series designations are written for specific applications. Threading often is performed on a lathe. Specifications such as thread height are critical in determining the strength of the threads. The material used is taken into consideration in determining the expected results of any particular application for that threaded piece. In external threading, a calculated depth is required as well as a particular angle to the cut. To perform internal threading, the exact diameter to bore the hole is critical before threading. The threads are distinguished from one another by the amount of tolerance and/or allowance that is specified. See turning.