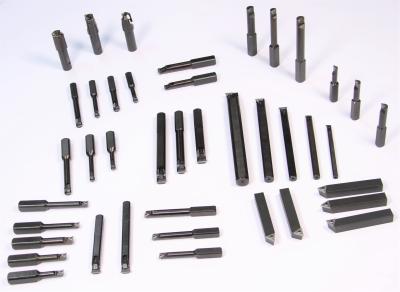
ARNO Werkzeuge USA announced it has reintroduced the H.B. Rouse brand of American-made, carbide cutting tools and inserts. Formerly sold and marketed under the Arno-Rouse name, the company has reintroduced Rouse as a stand-alone product offering under its original brand name: H.B. Rouse.
The company offers a broad range of carbide boring bars, tools and inserts for manual turning and milling operations.
• H.B. Rouse Little Hogger Mills have standard ¾” Weldon shanks and use standard carbide inserts and are useful on all milling machines like Bridgeport types to large boring mills.
• H.B. Rouse carbide insert turning tools triple-sided inserts for quick-change turning/lathe operations.
• H.B. Rouse triple-tip boring bars offer an improved triangular insert located within a precision machined pocket to eliminate shifting under heavy cuts. The cutting-edge only requires removing a single screw and indexing the insert.
• H.B. Rouse carbide insert boring bars feature carbide inserts that provide three cutting edges instead of only one (as is common with brazed tip tooling).
Martin Gardner, president of ARNO USA, added, “While ARNO Werkzeuge high-precision cutting tools and inserts is our focus in North America, the H.B. Rouse product has always been complimentary to our German-made, high-precision offering. H.B. Rouse cutting tools are still very popular in manual lathes and milling applications, such as automotive, education/training, hobbyist and other general machining markets."
Contact Details
Related Glossary Terms
- boring
boring
Enlarging a hole that already has been drilled or cored. Generally, it is an operation of truing the previously drilled hole with a single-point, lathe-type tool. Boring is essentially internal turning, in that usually a single-point cutting tool forms the internal shape. Some tools are available with two cutting edges to balance cutting forces.
- gang cutting ( milling)
gang cutting ( milling)
Machining with several cutters mounted on a single arbor, generally for simultaneous cutting.
- milling
milling
Machining operation in which metal or other material is removed by applying power to a rotating cutter. In vertical milling, the cutting tool is mounted vertically on the spindle. In horizontal milling, the cutting tool is mounted horizontally, either directly on the spindle or on an arbor. Horizontal milling is further broken down into conventional milling, where the cutter rotates opposite the direction of feed, or “up” into the workpiece; and climb milling, where the cutter rotates in the direction of feed, or “down” into the workpiece. Milling operations include plane or surface milling, endmilling, facemilling, angle milling, form milling and profiling.
- turning
turning
Workpiece is held in a chuck, mounted on a face plate or secured between centers and rotated while a cutting tool, normally a single-point tool, is fed into it along its periphery or across its end or face. Takes the form of straight turning (cutting along the periphery of the workpiece); taper turning (creating a taper); step turning (turning different-size diameters on the same work); chamfering (beveling an edge or shoulder); facing (cutting on an end); turning threads (usually external but can be internal); roughing (high-volume metal removal); and finishing (final light cuts). Performed on lathes, turning centers, chucking machines, automatic screw machines and similar machines.