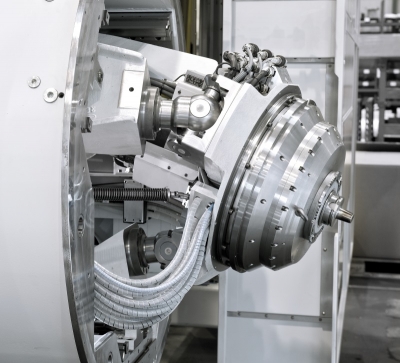
Amazing, but true: Over one and a half decades ago, many engineering companies were dreaming of parallel kinematic drives that would be able to replace conventional fork heads in machine tools after a brief period of euphoria, involving a few conferences, plenty of journal articles and several tentative attempts with prototypes and machines, things settled down again. Only one machine tool manufacturer reportedly had any success, working in close conjunction with an innovative aircraft producer to come up with a great three-legged idea.
This was the Ecospeed machining center, with its patented parallel kinematics. Starrag´s Ecospeed product range developed the new solution from scratch in less than a year, for the former DaimlerChrysler Aerospace AG. Managing Director Dr. Norbert Hennes recalls the first machine to be installed in April 2000 in Augsburg and its totally innovative drive concept. "Lots of people thought we were mad back then." But the idea developed by the engineering company and aircraft producer has been a success. Now the company has built more than 100 machines in the 18 years since, and these are in use worldwide. Every year, 15 machines from the Ecospeed series are produced, tailored to the specific application thanks to the modular overall concept. With these exclusive parallel kinematic machines, users in the aerospace industry throughout the world are now milling very large and challenging aluminum components from solid metal. The Ecospeed range is far and away the world's most productive solution for high-performance machining of aluminum structural components.
Sprint Z3 and its parallel kinematic concept: Three parallel linear axis drives are mounted radially equispaced in a barrel-shaped headstock. The spindle platform is connected to each drive by means of rigid levers with a simple pivot at one end, and a ball joint at the other end. A high performance motor spindle is mounted to the spindle platform. The headstock is mounted horizontally and moves vertically inside the column. This arrangement offers minimum movable mass resulting in unprecedented dynamic characteristics.
When all three axes are moved equally and simultaneously, the spindle is moved in a straight line in Z-direction. If the three axes move differentially, the spindle platform will be tilted in the A/B kinematic. Synchronized motion of the three Z-axes allows the spindle to describe any path within a spherical cone of ± 45 degrees.
All machines are now available with the latest modules of Starrag´s IPS (Integrated production System). True to the Starrag claim "Engineering precisely what you value", the IPS platform is based on the customer's individual task definition to provide the desired added value with a variety of features, systems and services.
Starrag has already used these IPS components to develop very interesting and wide-ranging Industry 4.0 solutions in combination with Ecospeed flexible manufacturing systems.
All machines in the Ecospeed range feature 161-hp, 30,000-rpm, 61-lbf-ft motor spindles, and have the option of a C-axis, allowing the use of automatic interchangeable angular milling heads.
Contact Details
Related Glossary Terms
- gang cutting ( milling)
gang cutting ( milling)
Machining with several cutters mounted on a single arbor, generally for simultaneous cutting.
- machining center
machining center
CNC machine tool capable of drilling, reaming, tapping, milling and boring. Normally comes with an automatic toolchanger. See automatic toolchanger.
- milling
milling
Machining operation in which metal or other material is removed by applying power to a rotating cutter. In vertical milling, the cutting tool is mounted vertically on the spindle. In horizontal milling, the cutting tool is mounted horizontally, either directly on the spindle or on an arbor. Horizontal milling is further broken down into conventional milling, where the cutter rotates opposite the direction of feed, or “up” into the workpiece; and climb milling, where the cutter rotates in the direction of feed, or “down” into the workpiece. Milling operations include plane or surface milling, endmilling, facemilling, angle milling, form milling and profiling.
- parallel
parallel
Strip or block of precision-ground stock used to elevate a workpiece, while keeping it parallel to the worktable, to prevent cutter/table contact.