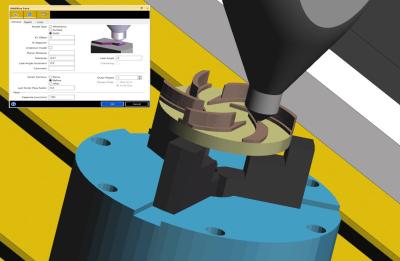
Responding to the increase in hybrid manufacturing, the latest release of Edgecam introduced a new Additive Machining module. Supporting the direct energy deposition method, Edgecam now offers a dedicated manufacturing cycle which accurately guides a laser as it deposits material to form a shape. After that, the shape is machined using Edgecam’s milling cycles to create the final component.
As Edgecam 2019 R1 now offers full ToolStore support for additive manufacturing, shapes can be built using almost any milling cycle, including advanced functions such as rotary and 5-axis simultaneous machining.
Edgecam Brand Manager John Buehler says the new Additive Lace cycle is designed to construct geometry on a layer-by-layer basis, depositing a continuous molten bead of material which adheres to the parent material. “Using the same intuitive dialog interface as all other Edgecam cycles, Additive Lace not only offers the ability to work with various CAD entities, but also empowers the user to determine numerous control types, such as lace angle, amount of finish passes, and undercut mode.”
In total, Edgecam 2019 R1 includes around 30 individual enhancements.
Performance Improvements
Mindful of the need to generate quick toolpaths to reduce production costs, Edgecam 2019 R1 introduces three performance-boosting enhancements to its machining engine, benefiting both turning and milling operations.
Regeneration time has been reduced by around 20 percent when editing the Move Angular/Index commands.
“Responding to customer feedback, the Waveform machining algorithm has been enhanced to reduce processing time. Previously, performance bottlenecks were detected when small stepovers were used, or on components with narrow channels and heavily curved regions. Manufacturers will now notice average time savings ranging between 15 and 60 percent, depending on the complexity of the component and its cycle parameters,” Buehler says.
And, because of improvements in the way Edgecam’s machining engine generates data, machining large complex components is now considerably quicker. This has been achieved by the way the software calculates prismatic geometry within the toolpath.
New Parting Off Cycle
A new Parting Off cycle is available for turning customers, satisfying a high demand for a single cycle to not only perform the parting off toolpath, but also to deburr the back edge during the operation. “Like all other turning cycles, Parting Off offers extended help through dialog pictures, and is sensitive to the current stock position.”
Finish Turning Cycle Support for CoroTurn Prime Inserts
Again, for turning customers, a new Up-Cutting function has been added to the Finish turning cycle. This enables high productivity finishing to be achieved in conjunction with Sandvik Coromant’s CoroTurn Prime tools and inserts.
Located alongside the Down-Cut modifier, Up-Cutting reverses the direction of the toolpath to utilize the Prime insert geometry. Also, the cycle feed rate can be expressed using the "Chip Thickness" modifier, as well as in the traditional format of feed per revolution.
Multiple User Experience Turning Enhancements
Found in the Rough Turn cycle, the Stock Runout function has been enhanced to give greater toolpath control when exiting the cut. The inclusion of Runout Angle and Runout Length means toolpaths can be trimmed to user-specific demands.
“Both the Thread Turning and Finish Groove cycles now benefit from functionality found in other turning commands. Safe Distance modifier has been added to the Thread Turning cycles, giving more accurate control at the start position of a threading toolpath,” says Buehler. “Finish Groove toolpaths can be more tightly controlled with new Start and End Extension modifiers.”
The Spindle Set-up function for multiple-spindle lathes now includes main- and sub-spindle C angle positions, further guaranteeing no collisions during the parts transfer command.
Numerous Edgecam Inspect Enhancements
Buehler says that although Edgecam Inspect is less than two years old, it continues to grow fast, and Edgecam 2019 R1 introduces 13 new enhancements to it. “Firstly, the mathematical brain behind the product is being switched to use the PCDMIS fit libraries supplied by our parent company, Hexagon. All Geometry Fit calculations, such as measurement deviations and GD&T values, now use a higher level of certified and approved algorithms.
“And we’ve introduced more customization. In the past, users had to accept the standard Measurement Report, but now they can develop their own software plugins to personalize it, along with developing their own probing Canned Cycles, usually in Renishaw or M&H format.”
Probing features can be managed more easily, as all commands are automatically created on separate layers. “Also, where either the solid model geometry is incorrect, or the model isn’t available, the new manual feature means it’s still possible to inspect a region,” Buehler says.
Through user feedback, specific Probing features now work with rotary solid faces, and the feedback can also include evaluation of Axis Deflection.
“The final enhancement to this area provides two new output variations in the Work Offset function: Type, and Axes. These give greater control and a more detailed inspection routine, while communicating to the machine tool via the NC Gateway,” he adds.
Hole Cycle Extra Collision Detection
The Hole Cycle now has additional collision checking. While stringent detection has been in place for a number of releases – such as a toolpath being re-directed to avoid a clamp – Edgecam 2019 R1 now checks if a hole is obstructed by any part of a fixture. Where such a collision exists, the system removes the drill position and alerts the user.
Chamfering Cycle Gouge Checking
Gouge Check Gap has been added to the Chamfering Cycle to give even stricter control over the toolpath. Specifically, neighbouring features which could potentially come into contact with the flute of the taper tool can now be excluded.
Extended CAD Format
Edgecam 2019 R1 supports the latest version of all CAD files. “Focusing on a few formats, users will notice, for instance, support for SpaceClaim 19 (ACIS V28), Parasolid version 30.1.247, Inventor 2019, and Creo 5.0. All other CAD formats will be catered for when a newer version becomes available," Buehler says.
“It’s particularly exciting that, regardless of which licence a user has, they’ll be able to load all Designer files – *.v_t and *.vdf extensions. Designer is Vero Software’s latest CAD package, featuring direct modelling technology. This will be a major boost for manufacturers who haven’t yet sampled the power of Edgecam’s Solid Machinist capabilities.”
Concluding, Buehler says: “Overall, there are more than 30 individual enhancements in Edgecam 2019 R1, geared towards improving efficiency, productivity, and ease of use, to keep manufacturers ahead of the game with the best technology available.”
Related Glossary Terms
- chamfering
chamfering
Machining a bevel on a workpiece or tool; improves a tool’s entrance into the cut.
- computer-aided design ( CAD)
computer-aided design ( CAD)
Product-design functions performed with the help of computers and special software.
- feed
feed
Rate of change of position of the tool as a whole, relative to the workpiece while cutting.
- fixture
fixture
Device, often made in-house, that holds a specific workpiece. See jig; modular fixturing.
- gang cutting ( milling)
gang cutting ( milling)
Machining with several cutters mounted on a single arbor, generally for simultaneous cutting.
- milling
milling
Machining operation in which metal or other material is removed by applying power to a rotating cutter. In vertical milling, the cutting tool is mounted vertically on the spindle. In horizontal milling, the cutting tool is mounted horizontally, either directly on the spindle or on an arbor. Horizontal milling is further broken down into conventional milling, where the cutter rotates opposite the direction of feed, or “up” into the workpiece; and climb milling, where the cutter rotates in the direction of feed, or “down” into the workpiece. Milling operations include plane or surface milling, endmilling, facemilling, angle milling, form milling and profiling.
- numerical control ( NC)
numerical control ( NC)
Any controlled equipment that allows an operator to program its movement by entering a series of coded numbers and symbols. See CNC, computer numerical control; DNC, direct numerical control.
- parting
parting
When used in lathe or screw-machine operations, this process separates a completed part from chuck-held or collet-fed stock by means of a very narrow, flat-end cutting, or parting, tool.
- solid model
solid model
3-D model created using “building blocks.” This is the most accurate way of representing real-world objects in CAD.
- threading
threading
Process of both external (e.g., thread milling) and internal (e.g., tapping, thread milling) cutting, turning and rolling of threads into particular material. Standardized specifications are available to determine the desired results of the threading process. Numerous thread-series designations are written for specific applications. Threading often is performed on a lathe. Specifications such as thread height are critical in determining the strength of the threads. The material used is taken into consideration in determining the expected results of any particular application for that threaded piece. In external threading, a calculated depth is required as well as a particular angle to the cut. To perform internal threading, the exact diameter to bore the hole is critical before threading. The threads are distinguished from one another by the amount of tolerance and/or allowance that is specified. See turning.
- toolpath( cutter path)
toolpath( cutter path)
2-D or 3-D path generated by program code or a CAM system and followed by tool when machining a part.
- turning
turning
Workpiece is held in a chuck, mounted on a face plate or secured between centers and rotated while a cutting tool, normally a single-point tool, is fed into it along its periphery or across its end or face. Takes the form of straight turning (cutting along the periphery of the workpiece); taper turning (creating a taper); step turning (turning different-size diameters on the same work); chamfering (beveling an edge or shoulder); facing (cutting on an end); turning threads (usually external but can be internal); roughing (high-volume metal removal); and finishing (final light cuts). Performed on lathes, turning centers, chucking machines, automatic screw machines and similar machines.
- undercut
undercut
In numerical-control applications, a cut shorter than the programmed cut resulting after a command change in direction. Also a condition in generated gear teeth when any part of the fillet curve lies inside of a line drawn tangent to the working profile at its point of juncture with the fillet. Undercut may be deliberately introduced to facilitate finishing operations, as in preshaving.