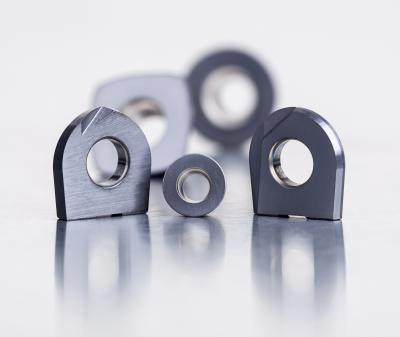
Dormer Pramet's latest milling grades - M4303 and M4310 - provide durability and reliability in semifinishing and finishing applications.
Each is designed for high-speed milling in the die and mold segment, offering consistent wear and longer tool life. An ultrathin PVD coating increases cutting edge toughness, while its substrate provides high hardness and cutting-edge strength, preventing fracture by chipping.
The M4303 replaces the previous 7205 grade and provides superior wear resistance. It has been developed for hardened steel above 55 HRC and cast iron, but can also be used for machining steels and nonferrous metals.
The M4310 takes over from the existing 7215 grade and offers an optimal balance of toughness and wear resistance in hardened steel and cast iron. It can also be used for machining stainless steel, steels and nonferrous metals.
Contact Details
Related Glossary Terms
- gang cutting ( milling)
gang cutting ( milling)
Machining with several cutters mounted on a single arbor, generally for simultaneous cutting.
- hardness
hardness
Hardness is a measure of the resistance of a material to surface indentation or abrasion. There is no absolute scale for hardness. In order to express hardness quantitatively, each type of test has its own scale, which defines hardness. Indentation hardness obtained through static methods is measured by Brinell, Rockwell, Vickers and Knoop tests. Hardness without indentation is measured by a dynamic method, known as the Scleroscope test.
- milling
milling
Machining operation in which metal or other material is removed by applying power to a rotating cutter. In vertical milling, the cutting tool is mounted vertically on the spindle. In horizontal milling, the cutting tool is mounted horizontally, either directly on the spindle or on an arbor. Horizontal milling is further broken down into conventional milling, where the cutter rotates opposite the direction of feed, or “up” into the workpiece; and climb milling, where the cutter rotates in the direction of feed, or “down” into the workpiece. Milling operations include plane or surface milling, endmilling, facemilling, angle milling, form milling and profiling.
- physical vapor deposition ( PVD)
physical vapor deposition ( PVD)
Tool-coating process performed at low temperature (500° C), compared to chemical vapor deposition (1,000° C). Employs electric field to generate necessary heat for depositing coating on a tool’s surface. See CVD, chemical vapor deposition.
- wear resistance
wear resistance
Ability of the tool to withstand stresses that cause it to wear during cutting; an attribute linked to alloy composition, base material, thermal conditions, type of tooling and operation and other variables.