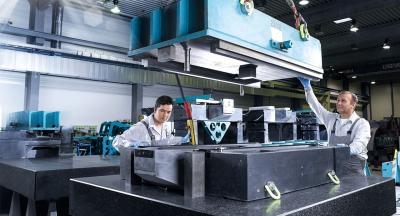
When it comes to replicating mineral casting beds, RAMPF says it is setting new standards. With new materials and optimized production and processing methods, an evenness of 0.02 millimeters and a straightness of 0.02 millimeters over a replication length of four meters is achieved.
“The new replication technology centers around the production process for the casting gauge and the reduction of dead weight while ensuring consistent or increased rigidity. Moreover, we are using new materials that have been tested in wide-ranging FEM calculations to ensure their suitability,” says Marc Dizdarevic, director of technics/development at RAMPF Machine Systems.
The basic accuracy of the casting gauge is 0.005 millimeters over the entire length. This is achieved on a reliable basis due to the optimized manufacturing process.
Dizdarevic says, "With this groundbreaking development, the many advantages of replication technology can now also be utilized for larger surfaces. Previously, replication accuracy in the hundredths of a millimeter range could only be reliably achieved with lengths up to 2.5 meters."
Thanks to this new replication technology, RAMPF Machine Systems can produce precision surfaces on machine beds in-house, in climate-controlled production shops without the need for machining work. The contour of high-precision gauges is transferred to the mineral casting blank by means of special lining systems (filled resins).
The key benefits:
- Excellent cost-efficiency, especially for medium to large quantities, as there is no costly use of machining equipment.
- The entire process is completed by RAMPF in-house – replicating in a climate-controlled workshop at 20° C; no external processors or transport required.
- High reliability because of lack of influence from machines or tools.
- There reportedly is only a small number of milling and grinding contractors that can reliably provide such high-precision results. The new replication technology eliminates any dependency on these service providers (e.g. fluctuating capacities).
“We have consistently built upon the replication technology developed by RAMPF over 20 years ago,” says Thomas Altmann, managing director of RAMPF Machine Systems. “Until recently, the biggest challenge was producing machine bed replications in lengths over 2.5 meters that still exhibited the precision that is needed for mechanical engineering applications. This is now possible with this new replication technology.”
Contact Details
Related Glossary Terms
- centers
centers
Cone-shaped pins that support a workpiece by one or two ends during machining. The centers fit into holes drilled in the workpiece ends. Centers that turn with the workpiece are called “live” centers; those that do not are called “dead” centers.
- gang cutting ( milling)
gang cutting ( milling)
Machining with several cutters mounted on a single arbor, generally for simultaneous cutting.
- grinding
grinding
Machining operation in which material is removed from the workpiece by a powered abrasive wheel, stone, belt, paste, sheet, compound, slurry, etc. Takes various forms: surface grinding (creates flat and/or squared surfaces); cylindrical grinding (for external cylindrical and tapered shapes, fillets, undercuts, etc.); centerless grinding; chamfering; thread and form grinding; tool and cutter grinding; offhand grinding; lapping and polishing (grinding with extremely fine grits to create ultrasmooth surfaces); honing; and disc grinding.
- milling
milling
Machining operation in which metal or other material is removed by applying power to a rotating cutter. In vertical milling, the cutting tool is mounted vertically on the spindle. In horizontal milling, the cutting tool is mounted horizontally, either directly on the spindle or on an arbor. Horizontal milling is further broken down into conventional milling, where the cutter rotates opposite the direction of feed, or “up” into the workpiece; and climb milling, where the cutter rotates in the direction of feed, or “down” into the workpiece. Milling operations include plane or surface milling, endmilling, facemilling, angle milling, form milling and profiling.