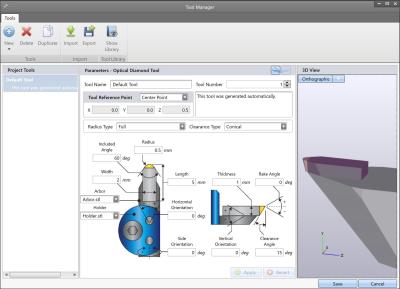
Moore Nanotechnology Systems (“Nanotech”) has released its next generation NanoCAM4 software package with enhanced capabilities. Nanotech’s latest product release has been years in the making. Comprehensive, yet easy to use, NanoCAM4 (N4) brings a significantly high level of accuracy and programming functionality to the ultraprecision optical market.
Mark Boomgarden, Nanotech’s president and CEO, said: “We are excited to announce this very important milestone in our product offerings. With the release of NanoCAM4, our customers are able to design and directly transfer their complex optical surfaces seamlessly to Nanotech’s machine tools. Our engineering teams have worked for almost 3-years, and have invested over 20,000 man-hours, in the design, development and testing of this NanoCAM4 package.”
Nanotech partnered with lead customers, technology institutions and software providers during the development cycle, providing opportunities to make incremental changes prior to the release. All previous CAM packages are viewed as “acceptable” for various programming needs, but they all have inherent weaknesses, often requiring intervention by third-party software to complete the task. In other cases, they simply do not have the capability or functionality to program many of the complicated and diverse optical-machining configurations required in today’s market.
Chris Morgan, chief development engineer for Nanotech, said: “NanoCAM4 is a completely new and superior CAM software package, developed with the goal of being the only ultra-precision programming software package customers will ever want or need. N4 enables improved form accuracies and direct importing/exporting of STEP, IGES or point clouds through the actual nonuniform rational B-splines (NURBS) raw data, thus eliminating the need for cumbersome and less-accurate point-cloud conversion.”
The output provides a smooth form and surface definition. Capable of generating a complete array of programs for diamond turning, micro-milling, ruling, rastering, diffractive/Fresnel, optical grinding and form correction, N4 is available in four different base modules.
Bob Cassin, Nanotech’s vice president of sales and marketing, commented, “Finally, there is a full-featured, 5-axis CAM package for ultraprecision machine tools that was designed to handle the complexity of today’s optical surfaces. Markets like mobile, AR/VR/MR, imaging and automotive lighting are innovating quickly, and we are seeing more requirements for free-form optical elements. NanoCAM4 demonstrates our dedication to keep pace in these markets and support our customers.”
The list of value-added advancements contained within the N4 CAM package is extensive, which includes:
Color-coded representations of exact acceleration and velocity values at every point on the surface enable up front program adjustments that result in reduced machine setup time and the most precise form accuracies.
Toolpath and machine simulations feature realistic 3D solid models, including any imported fixturing, to visually test and analyze tool geometries, programs and overall setup prior to taking a chip.
An integrated Oscillating X Dseg advanced programming capability for cellphone camera mold-pin manufacturers.
30 embedded optical equations and surface precision of 1nm.
NanoCAM4 is a CAM software package that enables next-generation design and processing capabilities for all diamond-turning customers.
Contact Details
Related Glossary Terms
- computer-aided manufacturing ( CAM)
computer-aided manufacturing ( CAM)
Use of computers to control machining and manufacturing processes.
- grinding
grinding
Machining operation in which material is removed from the workpiece by a powered abrasive wheel, stone, belt, paste, sheet, compound, slurry, etc. Takes various forms: surface grinding (creates flat and/or squared surfaces); cylindrical grinding (for external cylindrical and tapered shapes, fillets, undercuts, etc.); centerless grinding; chamfering; thread and form grinding; tool and cutter grinding; offhand grinding; lapping and polishing (grinding with extremely fine grits to create ultrasmooth surfaces); honing; and disc grinding.
- nonuniform rational B-splines ( NURBS)
nonuniform rational B-splines ( NURBS)
Type of curve or surface for which the difference between successive knots (parameter values) need not be expressed in uniform increments of 1. See B-spline.
- toolpath( cutter path)
toolpath( cutter path)
2-D or 3-D path generated by program code or a CAM system and followed by tool when machining a part.
- turning
turning
Workpiece is held in a chuck, mounted on a face plate or secured between centers and rotated while a cutting tool, normally a single-point tool, is fed into it along its periphery or across its end or face. Takes the form of straight turning (cutting along the periphery of the workpiece); taper turning (creating a taper); step turning (turning different-size diameters on the same work); chamfering (beveling an edge or shoulder); facing (cutting on an end); turning threads (usually external but can be internal); roughing (high-volume metal removal); and finishing (final light cuts). Performed on lathes, turning centers, chucking machines, automatic screw machines and similar machines.