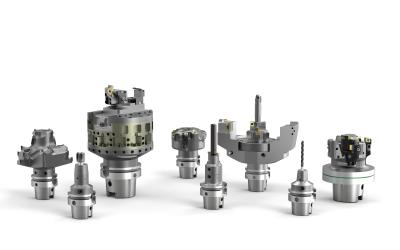
The turbocharger has been state-of-the-art in diesel vehicles for some time. And almost all automotive manufacturers offer a turbocharged petrol engine. Why? The turbocharger makes comparable performance with a smaller engine capacity possible and that contributes to the advance in downsizing. Turbochargers also help to achieve lower fuel consumption and are therefore fundamental in meeting strict emission limits. MAPAL offers the complete process for machining these parts, including tools.
Challenge for machining tools
Most turbochargers are exhaust gas turbochargers. These look different at almost every automotive manufacturer and have a special geometry. Common to all: there are very high temperatures when they are used in vehicles with petrol engines. For this reason the turbine housing, the so-called “hot side” is manufactured from very abrasive, heat-resistant materials. These materials represent a particular challenge for every machining tool.
MAPAL has taken up these challenges and developed new cutting materials and tools. The company offers the complete process for machining turbochargers, including all tools, for example, drills, milling cutters, reamers and mechatronic actuating tools – matched to the related geometry of the turbocharger. The company also assists its customers during the continuous further development of processes, to reduce cycle times and to increase tool lives. As such, combination tools that undertake multiple machining operations in one machining step form part of the portfolio.
A large part of turbocharger machining can be implemented using tools with ISO indexable inserts. Including many machining processes on the challenging hot side. MAPAL has developed a cutting material specially matched to the machining of heat-resistant cast steel and that offers long tool lives and therefore high cost-effectiveness, despite the abrasiveness of the material.
1. Complex boring tool with ISO indexable inserts
It is necessary to machine the V band on every turbocharger. Along with the material properties, an interrupted cut is often a challenge here during pre-machining. MAPAL relies on a complex boring tool with ISO indexable inserts to pre-machine the V band as well as to pre-machine the internal contour of the turbine. The tool therefore machines internally and externally simultaneously. Multiple steps are machined. The tool operates counterclockwise to transport the chips out of the component and to prevent damage to the internal contour of the turbine.
Machining example:
Material: 1.4837| Cooling: MQL | Diameter: 49; 70.5; 73; 90 mm; chamfer 10° | Cutting speed: 70 m/min | Feed: 0.4 mm | Tool life: 75 parts
2. Turning on the machining center using TOOLTRONIC
A particular challenge during the machining of the turbine housing for exhaust gas turbochargers is the main turbine bore. Its manufacture is subject to close tolerances in relation to shape, position and surface finish. The bore is bell-mouthed shaped to generate the best possible flow characteristics. MAPAL undertakes this machining operation using TOOLTRONIC with the LAT attachment (linear actuating tool). TOOLTRONIC, a mechatronic tool system, is a full NC axis integrated into the existing machine controller. The mounting tool is fitted with three inserts, one for roughing and two for finishing.
Machining example:
Material: 1.4837 | Cooling: MQL | Diameter: 40.5-57.295 mm | Cutting speed: 140 m/min (roughing), 120 m/min (finishing) | Feed: 0.15-0.4 mm | Tool life: 50 parts
3. New facemilling cutters for roughing
MAPAL recently announced a milling range with pressed, radial ISO indexable inserts. The milling cutter for roughing the face surface on the turbocharger housing comes from this range. The ISO indexable inserts with 16 usable cutting edges are the highlight of this facemilling cutter. As such the usage of the tool is particularly economical.
Machining example:
Material: 1.4849 | Cooling: Dry machining | Diameter: 125 mm, 14 inserts | Cutting speed: 80 m/min | Feed: 0.12 mm | Tool life: 125 parts
4. Diameter turning tool with tangential technology
The new tool from MAPAL for pre-machining the catalytic converter flange is also particularly cost-effective. Tangential technology is used on this diameter turning tool. Due to the upright and horizontal installation of the LTHU inserts, in effect eight cutting edges can be used per indexable insert.
Machining example:
Material: 1.4837 | Cooling: MQL | Diameter: 119 mm | Cutting speed: 80 m/min | Feed: 0.3 mm | Tool life: 100 parts
The four tools mentioned demonstrate, on the one hand, the different machining tasks on a turbocharger and, on the other hand, symbolise the variety of tools and know-how available from MAPAL. From standard milling cutters, through mechatronic actuating tools, to complex boring tools, the programme includes all the tools necessary for machining turbochargers, including the tool clamping systems. MAPAL designs the complete machining process such that the most reliable and cost-effective strategy for the customer is used. There is always a close eye on accuracy down to the μm so that the turbochargers achieve the highest possible efficiency in operation.
Contact Details
Related Glossary Terms
- abrasive
abrasive
Substance used for grinding, honing, lapping, superfinishing and polishing. Examples include garnet, emery, corundum, silicon carbide, cubic boron nitride and diamond in various grit sizes.
- bandsaw blade ( band)
bandsaw blade ( band)
Endless band, normally with serrated teeth, that serves as the cutting tool for cutoff or contour band machines.
- boring
boring
Enlarging a hole that already has been drilled or cored. Generally, it is an operation of truing the previously drilled hole with a single-point, lathe-type tool. Boring is essentially internal turning, in that usually a single-point cutting tool forms the internal shape. Some tools are available with two cutting edges to balance cutting forces.
- facemilling
facemilling
Form of milling that produces a flat surface generally at right angles to the rotating axis of a cutter having teeth or inserts both on its periphery and on its end face.
- gang cutting ( milling)
gang cutting ( milling)
Machining with several cutters mounted on a single arbor, generally for simultaneous cutting.
- indexable insert
indexable insert
Replaceable tool that clamps into a tool body, drill, mill or other cutter body designed to accommodate inserts. Most inserts are made of cemented carbide. Often they are coated with a hard material. Other insert materials are ceramic, cermet, polycrystalline cubic boron nitride and polycrystalline diamond. The insert is used until dull, then indexed, or turned, to expose a fresh cutting edge. When the entire insert is dull, it is usually discarded. Some inserts can be resharpened.
- interrupted cut
interrupted cut
Cutting tool repeatedly enters and exits the work. Subjects tool to shock loading, making tool toughness, impact strength and flexibility vital. Closely associated with milling operations. See shock loading.
- machining center
machining center
CNC machine tool capable of drilling, reaming, tapping, milling and boring. Normally comes with an automatic toolchanger. See automatic toolchanger.
- milling
milling
Machining operation in which metal or other material is removed by applying power to a rotating cutter. In vertical milling, the cutting tool is mounted vertically on the spindle. In horizontal milling, the cutting tool is mounted horizontally, either directly on the spindle or on an arbor. Horizontal milling is further broken down into conventional milling, where the cutter rotates opposite the direction of feed, or “up” into the workpiece; and climb milling, where the cutter rotates in the direction of feed, or “down” into the workpiece. Milling operations include plane or surface milling, endmilling, facemilling, angle milling, form milling and profiling.
- milling cutter
milling cutter
Loosely, any milling tool. Horizontal cutters take the form of plain milling cutters, plain spiral-tooth cutters, helical cutters, side-milling cutters, staggered-tooth side-milling cutters, facemilling cutters, angular cutters, double-angle cutters, convex and concave form-milling cutters, straddle-sprocket cutters, spur-gear cutters, corner-rounding cutters and slitting saws. Vertical cutters use shank-mounted cutting tools, including endmills, T-slot cutters, Woodruff keyseat cutters and dovetail cutters; these may also be used on horizontal mills. See milling.
- numerical control ( NC)
numerical control ( NC)
Any controlled equipment that allows an operator to program its movement by entering a series of coded numbers and symbols. See CNC, computer numerical control; DNC, direct numerical control.
- turning
turning
Workpiece is held in a chuck, mounted on a face plate or secured between centers and rotated while a cutting tool, normally a single-point tool, is fed into it along its periphery or across its end or face. Takes the form of straight turning (cutting along the periphery of the workpiece); taper turning (creating a taper); step turning (turning different-size diameters on the same work); chamfering (beveling an edge or shoulder); facing (cutting on an end); turning threads (usually external but can be internal); roughing (high-volume metal removal); and finishing (final light cuts). Performed on lathes, turning centers, chucking machines, automatic screw machines and similar machines.