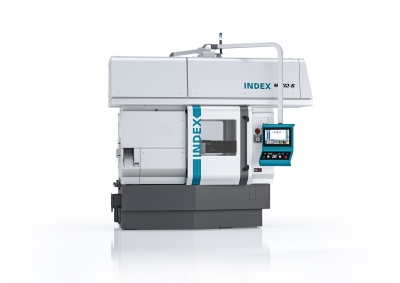
INDEX has announced the launch of its next generation MS32-6 multiple-spindle automatic lathe. This newest version of the six-spindle machine brings the benefits of multispindle technology to a broader range of applications thanks to a flexible tool slide platform that greatly reduces changeover times.
Accommodating up to 32 mm bar stock, the MS32-6 easily handles a wide variety of complex parts, as the machine is equipped with 12 cross slides, with two V-shaped cross slides equipped with X and Z axes located at each spindle position. C and Y axes, together with live tools, can also be implemented to allow for a broad range of machining processes, including off-center drilling, threading, contouring, hobbing and polygonal turning. All of the machines’ slides can also be alternatively configured for grooving or drilling.
Each cross slide in the MS32-6 now incorporates INDEX’s patented W-serration locating system that provides µm-accurate alignment of the toolholder. Coupled with the company’s newly developed quick clamping device, tools can be set up off of the machine and then quickly installed, reducing tool change times by 50%. Additionally, the machine incorporates the same W-serration system on its live units for drilling, milling and polygonal turning. By presetting tooling for these operations off of the machine, setup times can be reduced by up to 92%.
With the updated MS32-6, users can also now apply twin turrets with rigid tools in up to five spindle positions. These hydraulically controlled units can alternate between tools in less than half a second. This enables the efficient use of separate tools for roughing and finishing in the same position. The twin turrets can also be used to reduce tool changes by incorporating duplicate tools, an option that is especially attractive when working with difficult-to-machine materials.
The machine’s fluid-cooled spindle drum features six spindles with speeds that are independently controlled to a maximum of 8,000 rpm. This allows optimal cutting data to be applied to each individual cutting process, resulting in superior metal-removal rates, surface quality and tool life. Additionally, the machine can be equipped with one or two synchronous spindles, each of which can apply up to six tools for machining the rear end of parts.
Contact Details
Related Glossary Terms
- gang cutting ( milling)
gang cutting ( milling)
Machining with several cutters mounted on a single arbor, generally for simultaneous cutting.
- grooving
grooving
Machining grooves and shallow channels. Example: grooving ball-bearing raceways. Typically performed by tools that are capable of light cuts at high feed rates. Imparts high-quality finish.
- lathe
lathe
Turning machine capable of sawing, milling, grinding, gear-cutting, drilling, reaming, boring, threading, facing, chamfering, grooving, knurling, spinning, parting, necking, taper-cutting, and cam- and eccentric-cutting, as well as step- and straight-turning. Comes in a variety of forms, ranging from manual to semiautomatic to fully automatic, with major types being engine lathes, turning and contouring lathes, turret lathes and numerical-control lathes. The engine lathe consists of a headstock and spindle, tailstock, bed, carriage (complete with apron) and cross slides. Features include gear- (speed) and feed-selector levers, toolpost, compound rest, lead screw and reversing lead screw, threading dial and rapid-traverse lever. Special lathe types include through-the-spindle, camshaft and crankshaft, brake drum and rotor, spinning and gun-barrel machines. Toolroom and bench lathes are used for precision work; the former for tool-and-die work and similar tasks, the latter for small workpieces (instruments, watches), normally without a power feed. Models are typically designated according to their “swing,” or the largest-diameter workpiece that can be rotated; bed length, or the distance between centers; and horsepower generated. See turning machine.
- milling
milling
Machining operation in which metal or other material is removed by applying power to a rotating cutter. In vertical milling, the cutting tool is mounted vertically on the spindle. In horizontal milling, the cutting tool is mounted horizontally, either directly on the spindle or on an arbor. Horizontal milling is further broken down into conventional milling, where the cutter rotates opposite the direction of feed, or “up” into the workpiece; and climb milling, where the cutter rotates in the direction of feed, or “down” into the workpiece. Milling operations include plane or surface milling, endmilling, facemilling, angle milling, form milling and profiling.
- threading
threading
Process of both external (e.g., thread milling) and internal (e.g., tapping, thread milling) cutting, turning and rolling of threads into particular material. Standardized specifications are available to determine the desired results of the threading process. Numerous thread-series designations are written for specific applications. Threading often is performed on a lathe. Specifications such as thread height are critical in determining the strength of the threads. The material used is taken into consideration in determining the expected results of any particular application for that threaded piece. In external threading, a calculated depth is required as well as a particular angle to the cut. To perform internal threading, the exact diameter to bore the hole is critical before threading. The threads are distinguished from one another by the amount of tolerance and/or allowance that is specified. See turning.
- toolholder
toolholder
Secures a cutting tool during a machining operation. Basic types include block, cartridge, chuck, collet, fixed, modular, quick-change and rotating.
- turning
turning
Workpiece is held in a chuck, mounted on a face plate or secured between centers and rotated while a cutting tool, normally a single-point tool, is fed into it along its periphery or across its end or face. Takes the form of straight turning (cutting along the periphery of the workpiece); taper turning (creating a taper); step turning (turning different-size diameters on the same work); chamfering (beveling an edge or shoulder); facing (cutting on an end); turning threads (usually external but can be internal); roughing (high-volume metal removal); and finishing (final light cuts). Performed on lathes, turning centers, chucking machines, automatic screw machines and similar machines.