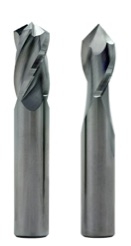
Scientific Cutting Tools welcomed the new year with the launch of brand new drill mills. The versatile, multi-operational specialty tool is designed for milling, chamfering, and light spotting applications. Despite the word 'drill' in the name, it is not recommended for drilling. The name is conceived from the common industry standard for the tool. Cutting diameter sizes range from 1/8" to 1/2". Included angle options are 90° or 120°. The two-flute design is optimal when chip evacuation and increased chip per tooth are the priority. For harder materials, the fortified strength of the four-flute design performs best and allows for increased feed rates in hard materials. Items are stocked uncoated or AlTiN coated. AlTiN coating is highly recommended for longevity and high-speed applications.
The drill mills are the newest addition to the specialty tool group. Helical chamfer mills were introduced in late 2018 followed by spotting drills in 2020. Both tools are significantly superior at their singular tasks, however, the drill mills have the advantage of performing both operations as well as general milling. The utility and diversity of the drill mill functions provide flexibility and enhanced productivity in one outstanding tool.
Contact Details
Related Glossary Terms
- chamfering
chamfering
Machining a bevel on a workpiece or tool; improves a tool’s entrance into the cut.
- feed
feed
Rate of change of position of the tool as a whole, relative to the workpiece while cutting.
- gang cutting ( milling)
gang cutting ( milling)
Machining with several cutters mounted on a single arbor, generally for simultaneous cutting.
- included angle
included angle
Measurement of the total angle within the interior of a workpiece or the angle between any two intersecting lines or surfaces.
- milling
milling
Machining operation in which metal or other material is removed by applying power to a rotating cutter. In vertical milling, the cutting tool is mounted vertically on the spindle. In horizontal milling, the cutting tool is mounted horizontally, either directly on the spindle or on an arbor. Horizontal milling is further broken down into conventional milling, where the cutter rotates opposite the direction of feed, or “up” into the workpiece; and climb milling, where the cutter rotates in the direction of feed, or “down” into the workpiece. Milling operations include plane or surface milling, endmilling, facemilling, angle milling, form milling and profiling.
- milling machine ( mill)
milling machine ( mill)
Runs endmills and arbor-mounted milling cutters. Features include a head with a spindle that drives the cutters; a column, knee and table that provide motion in the three Cartesian axes; and a base that supports the components and houses the cutting-fluid pump and reservoir. The work is mounted on the table and fed into the rotating cutter or endmill to accomplish the milling steps; vertical milling machines also feed endmills into the work by means of a spindle-mounted quill. Models range from small manual machines to big bed-type and duplex mills. All take one of three basic forms: vertical, horizontal or convertible horizontal/vertical. Vertical machines may be knee-type (the table is mounted on a knee that can be elevated) or bed-type (the table is securely supported and only moves horizontally). In general, horizontal machines are bigger and more powerful, while vertical machines are lighter but more versatile and easier to set up and operate.