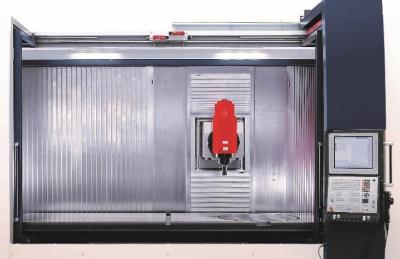
With the MMV 4200 / 5200 / 6200 models, EMCO introduces an extension to its MMV series, featuring enlarged travel paths (X= 4200 / 5200 / 6200) in response to increased demand in the travelling column machine segment. The machines with 3, 4 and 5 axes can be used for complete machining of very large and heavy parts in one clamping. The proven technology MMV 3200 has been kept in the new models: a high-performance motor spindle with 0 - 15,000 rpm speed range, 46 kW spindle power and up to 170 Nm torque. 40 tool pockets available as standard, optionally expandable up to 120 pockets. Thanks to the new modular system, customers do not have to choose between a smaller machine or one that is too large; variable sizes are possible up to 6,200 mm. The main difference between the MMV 4200 / 5200 and 6200 and the previous model is the X-axis drive, which uses a rack-and-pinion system instead of ball screws. This ensures dynamic, fast and precise feed during machining. The demand for these high-performance machines comes mainly from the petroleum industry, railroad industry and intralogistics.
Highlights
The extremely compact machine bed of the travelling column machining centres is a heat-treated, welded steel structure that provides a torsion-resistant and stable base for all components and machining operations. The production of large and heavy workpieces up to 8,000 kg is enabled by a powerful motor spindle with 46 kW spindle power, a torque of up to 170 Nm and a spindle speed of up to 15,000 rpm (18,000 rpm HSK-A63). Both spindle versions are grease-lubricated. The new versions of the previous model support complete machining of very long and heavy workpieces without reclamping. A new modular system ensures a variable choice of workpiece sizes up to 6,200 mm during machining. The large work area doors ensure easy loading and unloading of workpieces and fixtures, even when using a crane.
As standard, the machines have 40 stationary tool pockets; these can be increased to up to 120 tool pockets (also optionally alongside column) on request. The MMV 4200/5200 and 6200 feature a rack-and-pinion X-axis drive system that ensures dynamic, fast and precise machining at all times, even with long travels.
With this system, rapid traverses of up to 60 m/min can be achieved.
The machine versions with swivel head (B-axis) and rotary table (C-axis) are ideally suited for 5-axis simultaneous machining. Both the swivel head and the rotary table are driven by dynamic torque motors. The swivel head available in the standard versions has a range of up to ± 120° and a speed of 50 rpm, the rotary table n x 360° has a speed of up to 100 rpm. The rotary table with Ø 900 mm is designed for workpiece weights up to 2000 kg. All linear axes are already equipped with glass scales as standard. The dynamic linear axes and the torque drives of the rotary axis create ideal conditions for 5-axis simultaneous machining of complex workpieces.
State-of-the-art digital control systems from Heidenhain (TNC 640 - 24" monitor*) or Siemens (840D sl - 22" monitor) ensure user-friendly machine operation. The ergonomic design of the MMV series with its movable control panel creates ideal working conditions for the operator, who can swivel and rotate the control panel in the working area as well as move it along the longitudinal axis without interrupting the machining process, while keeping the workpiece in view at all times.
(*Currently only on the new variants of the MMV, after the introduction of to the new design, the MMV 2000 and 3200 will also be equipped with the new monitor).
Options
The machining centres can be equipped with numerous options such as coolant filtering systems with high pressure pumps with up to 60 bar through the spindle, which permit the use of high-performance tools with internal cooling. All guides and rack drives are permanently grease-lubricated via a central lubrication system, while oil films are kept from forming in the coolant system.
State-of-the-art touch probes allow automatic measurement of tools and workpieces. RF or laser touch probes are optionally available for this purpose. This reduces the setup time for tool changes and increases the quality of the workpiece.
Thanks to the large working areas of the MMV series machines, it is possible to optionally add a partition wall for pendulum operation, a second integrated rotary table or and NC axis with counter bearing.
Features such as the automatic door operation or thermal compensation of the milling spindle make the machining centres even more efficient.
Key technical data:
MMV 4200 / 5200 / 6200
Working area
X-axis travel [mm] 4200 / 5200 / 6200
Y-axis travel [mm] 1000
Z-axis travel [mm] 950
Swivel range of the B-axis +/- 120°
Turning range of the C-axis n x 360°
Feed drives
Rapid traverse speed in X/Y/Z [m/min] 60/40 /40
Acceleration X, Y, Z-axis [m/s²] 3/4/4
Table
Length x width [mm] 4400/5400/6470 x 1050
Max. workpiece weight [kg] 6000/7000/8000
Milling spindle
Speed range ISO/BT [rpm] 50 - 15,000
Speed range HSK-A63 [rpm] 50 - 18,000
Spindle power [kW] 46
Max. torque [Nm] 125 (S125 (S1) / 170 (S6)
Stationary tool magazine
Number of tool pockets 40
Tool changeover time (tool-to-tool) [sec] 5*
Max. tool diameter [mm] 75
Max. tool length [mm] 380
Max. tool weight [kg] 8
Alongside column tool magazine
Number of tool pockets 40/60/120
Tool changeover time (chip-to-chip) [sec] 12
Max. tool diameter [mm] 92
Max. tool length [mm] 300
Max. tool weight [kg] 8
* Timing expressed here as tool-to-tool because the chip-to-chip time depends on the X-travel.
Highest precision even for large dimensions: MMV 3200 travelling column machining centre
EMCO creates a 3-, 4- or 5-axis machining centre for heavy chip removal and precision cutting. The user can define the machine design that suits them best by choosing from the many options. The MMV 3200 is available in 3- or 4-axis versions with a B-axis. For 5-axis simultaneous machining an integrated torque rotary table is added as a 5th axis. With the option of adding a second torque rotary table, 5-axis machining can be performed in pendulum mode in two workspaces.
In addition to the stationary tool magazine with 40 pockets (optionally up to 60 pockets) on the left side of the machine, up to a further 60 tool pockets can also be installed on the right. Alternatively, for 4- and 5-axis machines, tool magazines with 40, 60 or 120 pockets can be mounted on the travelling column. The machine also features a high-performance motor spindle with a speed range of 0 - 15,000 rpm, an output of 46 kW and a torque of up to 170 Nm. These are all features that make the MMV 3200 the ideal machining centre for high-quality milling and enable the complete production of complex workpieces with excellent surfaces. The machine is thus equally suited to the requirements of the automotive or aerospace industry as well as to those of machine manufacturers or job shops.
Highlights
The extremely compact machine bed of the moving column machining centre is a heat-treated, welded steel structure that provides a torsion-resistant and stable base for all components and machining operations. The production of large and heavy workpieces up to 5000 kg is possible with a powerful motor spindle with 46 kW spindle power, a torque of up to 170 Nm and a spindle speed of up to 15 000 rpm (18 000 rpm HSK-A63). Both spindle variants are permanently grease-lubricated. The two large work area doors ensure easy loading and unloading of workpieces and fixtures, even when using a crane. The drum magazine of the MMV 3200 has 40 tool pockets as standard; this can be enlarged on request and supplemented by an additional magazine with a further 40 or 60 tool pockets. Likewise, a 40-, 60- or 120-pocket alongside column tool magazine is optionally available for the 4- and 5-axis variants. On the MMV 3200, ball screws, which are directly connected to the motors via backlash-free couplings, transmit the forces and movements in the X, Y and Z axes. This allows axis accelerations of up to 4 m/s² and rapid traverses of up to 50 m/min to be achieved.
The machine version with swivel head (B-axis) and rotary table (C-axis) is ideally suited for 5-axis simultaneous machining. Both the swivel head and the rotary table are driven by dynamic torque motors. The swivel head has a range of up to ± 120° and a speed of 50 rpm, the rotary table n x 360° has a speed of up to 100 rpm. The rotary table with Ø 900 mm is designed for workpiece weights of up to 2000 kg. All linear axes are already equipped with glass scales as standard. The dynamic linear axes and torque drives of the rotary axis create ideal conditions for 5-axis simultaneous machining of complex workpieces.
State-of-the-art digital control systems from Heidenhain (TNC 640 - 19" monitor) or Siemens (840D sl - 22" monitor) enable user-friendly machine operation. The ergonomic design of the MMV 3200 with the movable control panel creates ideal working conditions for the operator, who can swivel, rotate as well as move the control panel along the longitudinal axis in the area of the workspace without interrupting the machining process, while keeping the workpiece in view at all times.
Options
The machining centre can be equipped with numerous options, such as coolant filter systems with high pressure pumps with up to 60 bar through the spindle, which permit the use of high-performance tools with internal cooling. All guides and screw drives are permanently grease-lubricated via a central lubrication system, while oil films are kept from forming in the coolant system.
State-of-the-art touch probes allow automatic measurement of tools and workpieces. RF or laser touch probes are optionally available for this purpose. This reduces the setup time for tool changes and increases the quality of the workpiece.
Thanks to the large working area of the machine, it is possible to optionally add a partition for pendulum operation, a second integrated rotary table or NC axis with counter bearing. Specifications such as automatic door operation or thermal compensation of the milling spindle make the machining centre even more efficient.
Key technical data:
MMV 3200
Work area
X-axis travel [mm] 3200
Y-axis travel [mm] 1000
Z-axis travel [mm] 950
Swivel range of the B-axis +/- 120°
Turning range of the C-axis n x 360°
Feed drives
Rapid traverse speed in X/Y/Z [m/min] 50/40/40
Acceleration X, Y, Z-axis [m/s²] 3/4/4
Table
Length x width [mm] 3500 x 1050
Max. workpiece weight [kg] 5000
Milling spindle
Speed range ISO/BT [rpm] 50 - 15,000
Speed range HSK-A63 [rpm] 50 - 18,000
Spindle power [kW] 46
Max. torque [Nm] 125 (S125 (S1) / 170 (S6)
Stationary tool magazine
Number of tool pockets 40
Tool changeover time (chip-to-chip) [sec] 10
Max. tool diameter [mm] 75
Max. tool length [mm] 380
Max. tool weight [kg] 8
Alongside column tool magazine
Number of tool pockets 40/60/120
Tool changeover time (chip-to-chip) [sec] 12
Max. tool diameter [mm] 92
Max. tool length [mm] 300
Max. tool weight [kg] 8
Contact Details
Related Glossary Terms
- coolant
coolant
Fluid that reduces temperature buildup at the tool/workpiece interface during machining. Normally takes the form of a liquid such as soluble or chemical mixtures (semisynthetic, synthetic) but can be pressurized air or other gas. Because of water’s ability to absorb great quantities of heat, it is widely used as a coolant and vehicle for various cutting compounds, with the water-to-compound ratio varying with the machining task. See cutting fluid; semisynthetic cutting fluid; soluble-oil cutting fluid; synthetic cutting fluid.
- feed
feed
Rate of change of position of the tool as a whole, relative to the workpiece while cutting.
- gang cutting ( milling)
gang cutting ( milling)
Machining with several cutters mounted on a single arbor, generally for simultaneous cutting.
- milling
milling
Machining operation in which metal or other material is removed by applying power to a rotating cutter. In vertical milling, the cutting tool is mounted vertically on the spindle. In horizontal milling, the cutting tool is mounted horizontally, either directly on the spindle or on an arbor. Horizontal milling is further broken down into conventional milling, where the cutter rotates opposite the direction of feed, or “up” into the workpiece; and climb milling, where the cutter rotates in the direction of feed, or “down” into the workpiece. Milling operations include plane or surface milling, endmilling, facemilling, angle milling, form milling and profiling.
- numerical control ( NC)
numerical control ( NC)
Any controlled equipment that allows an operator to program its movement by entering a series of coded numbers and symbols. See CNC, computer numerical control; DNC, direct numerical control.
- rapid traverse
rapid traverse
Movement on a CNC mill or lathe that is from point to point at full speed but, usually, without linear interpolation.
- turning
turning
Workpiece is held in a chuck, mounted on a face plate or secured between centers and rotated while a cutting tool, normally a single-point tool, is fed into it along its periphery or across its end or face. Takes the form of straight turning (cutting along the periphery of the workpiece); taper turning (creating a taper); step turning (turning different-size diameters on the same work); chamfering (beveling an edge or shoulder); facing (cutting on an end); turning threads (usually external but can be internal); roughing (high-volume metal removal); and finishing (final light cuts). Performed on lathes, turning centers, chucking machines, automatic screw machines and similar machines.