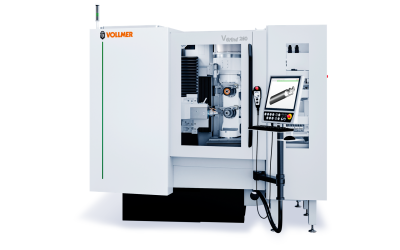
VGrind 260, VGrind Neon and VGrind Argon – these are the names of the three new tool grinding machines from the sharpening specialist VOLLMER. They were presented for the first time at the GrindingHub 2022 trade fair in Stuttgart. All three machines are based on VOLLMER's innovative double spindle concept, which enables precise and efficient multi-level machining thanks to its two vertical spindles. While the VGrind 260 can be configured for specific customer requirements, the VGrind Argon and Neon are two special editions that VOLLMER has designed for fast and cost efficient access to the world of tool grinding.
All three models are suitable for machining rotary tools made from carbide, such as drills, milling cutters or reamers. With these machines, VOLLMER is expanding their range of tool and cutter grinders, which also includes the VGrind 340S and VGrind 360S models.
VGrind 260 can be configured individually
Like the VGrind 340S and 360S models, the new VOLLMER VGrind 260 grinding machine can be configured individually. For example, customers can choose between a direct drive or belt drive for the grinding spindles or equip the machine with a grinding wheel changer for up to eight grinding wheel sets – also including interchangeable coolant nozzles, if required. Several options are possible for the automation for unmanned, round-the-clock machining: The HP 160 pallet magazine offers space for up to 900 blanks or tools made from carbide and the HC4 chain magazine can be loaded with up to 158 shank type tools or 39 HSK-A63 tool holders. As an alternative, the machine is available with an internal pallet loader. It offers space for two compact pallets with a capacity of up to 300 blanks or tools. Furthermore, random loading of different shank diameters is also possible.
Just like all other VGrind models, the VGrind 260 also has outstanding kinematic properties with two grinding spindles situated above each other, with the grinding wheel set positioned at the C axis pivot point for efficient multi-layer machining. This arrangement reduces the machining times thanks to shorter linear axis travel distances.
Enter into the world of tool grinding with VGrind Argon and Neon
The new VGrind Neon and VGrind Argon tool grinding machines are also based on the tried-and-tested "DNA" with the double-spindle concept. VOLLMER has designed the compact machines for cost efficient entry into the world of tool grinding and provided them with functional features as standard: As with all VGrind models, they are equipped with an IoT Gateway (Internet of Things) and have an internal wheel measurement system, which measures the grinding wheels and monitors their wear. The VGrind Argon has a four-wheel grinding wheel changer as well as an internal pallet loader and is designed for fully automatic operation.
"Our unique VGrind approach of multi-level machining has established itself as a reliable and highly precise technology in the global market for tool grinding," says Jürgen Hauger, CEO of the VOLLMER Group. "With our new VGrind models, we are specifically responding to different requirements that tool manufacturers and sharpening services around the world have placed on us: On the one hand, there are individual configurations of the machines with regard to flexibility and precision; on the other hand, there is an outstanding price-performance ratio."
Contact Details
Related Glossary Terms
- coolant
coolant
Fluid that reduces temperature buildup at the tool/workpiece interface during machining. Normally takes the form of a liquid such as soluble or chemical mixtures (semisynthetic, synthetic) but can be pressurized air or other gas. Because of water’s ability to absorb great quantities of heat, it is widely used as a coolant and vehicle for various cutting compounds, with the water-to-compound ratio varying with the machining task. See cutting fluid; semisynthetic cutting fluid; soluble-oil cutting fluid; synthetic cutting fluid.
- gang cutting ( milling)
gang cutting ( milling)
Machining with several cutters mounted on a single arbor, generally for simultaneous cutting.
- grinding
grinding
Machining operation in which material is removed from the workpiece by a powered abrasive wheel, stone, belt, paste, sheet, compound, slurry, etc. Takes various forms: surface grinding (creates flat and/or squared surfaces); cylindrical grinding (for external cylindrical and tapered shapes, fillets, undercuts, etc.); centerless grinding; chamfering; thread and form grinding; tool and cutter grinding; offhand grinding; lapping and polishing (grinding with extremely fine grits to create ultrasmooth surfaces); honing; and disc grinding.
- grinding machine
grinding machine
Powers a grinding wheel or other abrasive tool for the purpose of removing metal and finishing workpieces to close tolerances. Provides smooth, square, parallel and accurate workpiece surfaces. When ultrasmooth surfaces and finishes on the order of microns are required, lapping and honing machines (precision grinders that run abrasives with extremely fine, uniform grits) are used. In its “finishing” role, the grinder is perhaps the most widely used machine tool. Various styles are available: bench and pedestal grinders for sharpening lathe bits and drills; surface grinders for producing square, parallel, smooth and accurate parts; cylindrical and centerless grinders; center-hole grinders; form grinders; facemill and endmill grinders; gear-cutting grinders; jig grinders; abrasive belt (backstand, swing-frame, belt-roll) grinders; tool and cutter grinders for sharpening and resharpening cutting tools; carbide grinders; hand-held die grinders; and abrasive cutoff saws.
- grinding wheel
grinding wheel
Wheel formed from abrasive material mixed in a suitable matrix. Takes a variety of shapes but falls into two basic categories: one that cuts on its periphery, as in reciprocating grinding, and one that cuts on its side or face, as in tool and cutter grinding.
- milling
milling
Machining operation in which metal or other material is removed by applying power to a rotating cutter. In vertical milling, the cutting tool is mounted vertically on the spindle. In horizontal milling, the cutting tool is mounted horizontally, either directly on the spindle or on an arbor. Horizontal milling is further broken down into conventional milling, where the cutter rotates opposite the direction of feed, or “up” into the workpiece; and climb milling, where the cutter rotates in the direction of feed, or “down” into the workpiece. Milling operations include plane or surface milling, endmilling, facemilling, angle milling, form milling and profiling.
- shank
shank
Main body of a tool; the portion of a drill or similar end-held tool that fits into a collet, chuck or similar mounting device.