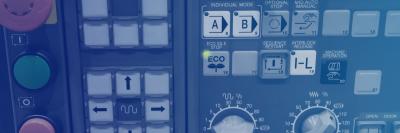
The ECO suite plus technology is the Okuma America Corporation’s latest addition to a suite of products designed to support global and corporate sustainability initiatives. Initial sustainable product developments began in 1963 with the launch of the proprietary Okuma numeric control system. In 2001 the company further advanced sustainability initiatives with the Thermo-Friendly Concept, a technology design to manage thermal temperature ranges during the machining process. In 2014 the company released the inaugural ECO suite system which could monitor and control machine usage as a macro level. Today the company is pleased to unveil the next-generation technology - ECO suite plus - which builds upon the prior technology releases by providing management and control of specific machine operations and peripheral devices during the machining process and in idle mode. Both the Thermo-Friendly Concept and ECO technologies are powered by Okuma’s proprietary OSP control, a Windows-based, open-architecture platform which offers maximum machining capabilities to users.
ECO suite plus Features at a Glance
The ECO suite plus technology harbors several features to aid in energy savings opportunities, including:
- ECO Idling Stop: The application’s ECO Idling Stop function monitors the cooling stays of the milling and turning spindles. It will automatically turn off the coolers for those spindles when spindle temperature is stable.
- ECO Power Monitor: The ECO Power Monitor feature displays the power consumption of various components directly on the machine tool’s display. This includes the power consumption of spindles, feed axes and peripheral equipment, giving the operator a view of the total energy being saved at a glance, without requiring a data export or separate smart device.
- Additional Optional Features
- ECO Hydraulics - utilizing SERVO technology, actively monitors the demand of hydraulics to activate the hydraulic pump only as necessary to maintain pressures as called
- ECO Operation is recommending to users with multiple peripherals, as this function will run peripheral equipment only when needed and turn off peripherals once machining is complete
Contact Details
Related Glossary Terms
- feed
feed
Rate of change of position of the tool as a whole, relative to the workpiece while cutting.
- gang cutting ( milling)
gang cutting ( milling)
Machining with several cutters mounted on a single arbor, generally for simultaneous cutting.
- milling
milling
Machining operation in which metal or other material is removed by applying power to a rotating cutter. In vertical milling, the cutting tool is mounted vertically on the spindle. In horizontal milling, the cutting tool is mounted horizontally, either directly on the spindle or on an arbor. Horizontal milling is further broken down into conventional milling, where the cutter rotates opposite the direction of feed, or “up” into the workpiece; and climb milling, where the cutter rotates in the direction of feed, or “down” into the workpiece. Milling operations include plane or surface milling, endmilling, facemilling, angle milling, form milling and profiling.
- turning
turning
Workpiece is held in a chuck, mounted on a face plate or secured between centers and rotated while a cutting tool, normally a single-point tool, is fed into it along its periphery or across its end or face. Takes the form of straight turning (cutting along the periphery of the workpiece); taper turning (creating a taper); step turning (turning different-size diameters on the same work); chamfering (beveling an edge or shoulder); facing (cutting on an end); turning threads (usually external but can be internal); roughing (high-volume metal removal); and finishing (final light cuts). Performed on lathes, turning centers, chucking machines, automatic screw machines and similar machines.